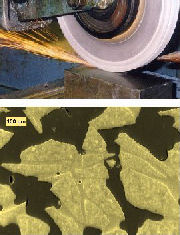
Improved grinding tools by modified ceramic binding.
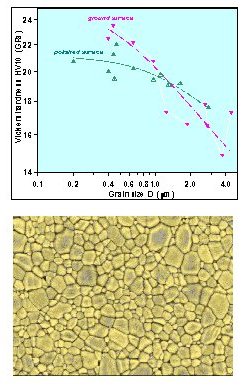
Increased hardness by smaller grain sizes of sintered corundum. Example of a microstructure of pressureless sintered (1230 °C/2h) sub-µm corundum grit (Al2O3), grain size 0.24 µm, hardness HV1 = 22 GPa.
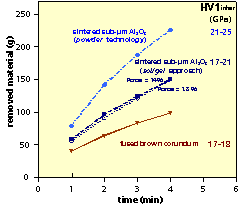
Improved grinding power of sub-µm Al2O3-grits compared with fused corundum, with an additional benefit from new powder processing.
Sub-µm and nano-technologies for tools with improved grinding power by micro-structures with increased mechanical, thermal and chemical stability
Most available grinding tools are composed of grits with coarse microstructures (fused corundum). An optimized modification of the ceramic bonding process improves the tool power even when using these traditional grits. Further progress is obtained when fused materials are substituted by tools with sintered (polycrystalline) grits with a leap in hardness due to microstructures which associate a sub-µm grain size with a highest density.
Advantages
- Grinding rate increased by more than 100 % on machining (e.g.) steel
- Tuning of grit hardness and microfracture performance depending on the application
- Improved mechanical stability of tools by advanced ceramic bonding
- Minimum defect population in tools manufactured by new shaping technologies
Products and services offered
- Development of sintered polycrystalline grits with increased grinding power
- Alternative development of improved sol/gel processes and of new powder technologies
- Development of new ceramic bonding compositions and technologies
- Technological investigations for upscaling supporting the development of new products screening of raw materials and development of new shaping approaches
- Investigations of the technical performance in various applications