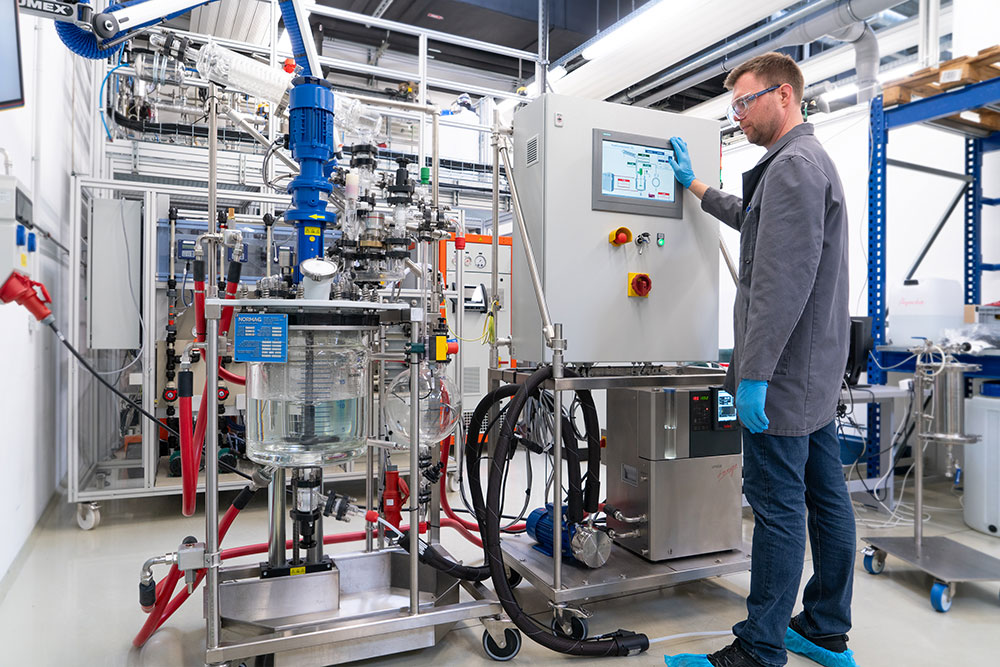

Efficient energy converters and energy storage systems are key components of the energy transition. In order to achieve a circular and green economy, it is necessary to optimize recycling processes in these areas. The aim is to close material cycles and secure sources of domestic materials. This is where the "Recycling and Green Battery" working group comes in.
We are working on environmentally friendly and efficient recycling processes for batteries, electronic components, photovoltaic panels, fuel cells and electrolyzers. We pursue the zero-waste principle, a low CO2 footprint and energy and resource efficiency, as well as monitoring and automation for effective process control. We want to offer holistic solutions that range from the initial idea to development and optimization on a pilot plant scale.
Recovery of critical raw materials
The "Recycling and Green Battery" working group focuses on the development of holistic, raw material-independent approaches to increase recovery and recycling rates. At the same time, the purity and quality of the recycled products are to be increased. The aim is to provide products in primary quality that meet the needs of the industry and thus the necessary requirements. To this end, we operate pilot plants at our Freiberg site that can be used to recover critical raw materials using hydrometallurgical approaches.
Evaluation of recyclates
Another area of expertise at Fraunhofer IKTS is determining the influence of various impurities on the recovered product. Here we determine the limit of impurities that the product can tolerate for the market requirements of a specific application. This helps to reduce certain purification steps and thus maximize the efficiency of the entire value chain.
Sustainability through design
Sustainable assessments, which include economic, technical and ecological aspects, can be carried out not only for the overall recycling process, but also for individual key processes that help to make a recycling approach more efficient. In addition, Fraunhofer IKTS develops design guidelines for various applications with a focus on batteries to ensure a cycle-oriented and recycling-friendly design.