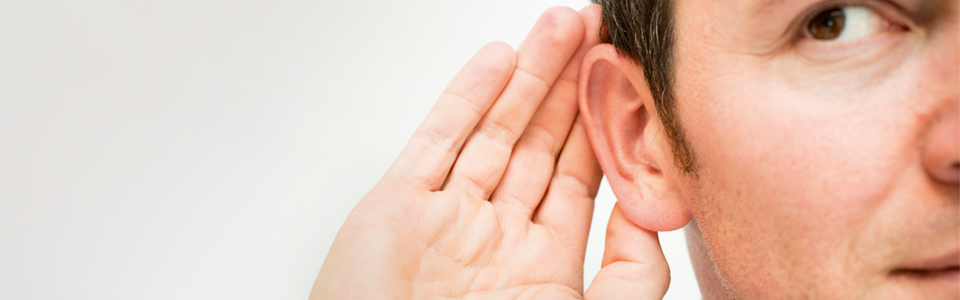
As the complexity of products and processes in manufacturing and operations increases, so does the need for cost-effective and reliable approaches in quality assurance, repair, and maintenance. This challenge can easily be met with acoustic diagnostic methods. Defective components and critical plant and operational processes have unique noise patterns, which can be detected quickly and accurately with acoustic methods. In this brochure, Fraunhofer IKTS presents a selection of easy-to-integrate, low-cost acoustic diagnostic solutions, which can be combined with state-of-the-art artificial intelligence (AI) methods to enable optimization over the entire product life cycle.
Fraunhofer IKTS is a proven specialist for non-destructive test systems and processes and can draw on extensive experience in the area of acoustic diagnostics. Operational malfunctions and component damages can be detected using active or passive methods. Acoustic diagnostics comprises quality assessment of parts and materials, monitoring of wear parts in machines and plants, and damage detection in parts and components. Analysis and evaluation can be performed on a wide variety of materials, including iron, aluminum, glass, fiber-reinforced composites, and paper. Acoustic diagnostics can be used during and after production as well as for condition monitoring of wear and other parts in a host of industries (automotive and aerospace engineering, mechanical engineering, paper and food industry, energy sector, etc.). The technology can also be applied to non-technical sound signals, e.g., for pest detection in grain storage facilities or for realizing secure and operationally reliable voice control of industrial equipment. At the heart of acoustic diagnostic techniques are state-of-the-art artificial intelligence methods, such as pattern recognition and machine learning, which allow for automatic and reliable analysis of even highly complex signals or signals with significant noise, in real time. Determination of damage extent or residual life is also possible.
Innovation and development are the cornerstones of a promising corporate future. In order to create a competitive edge, Fraunhofer offers tailored options for cooperation, so that small and medium-sized companies can work together in the best possible way. This also allows to utilize development skills at short notice and as needed.