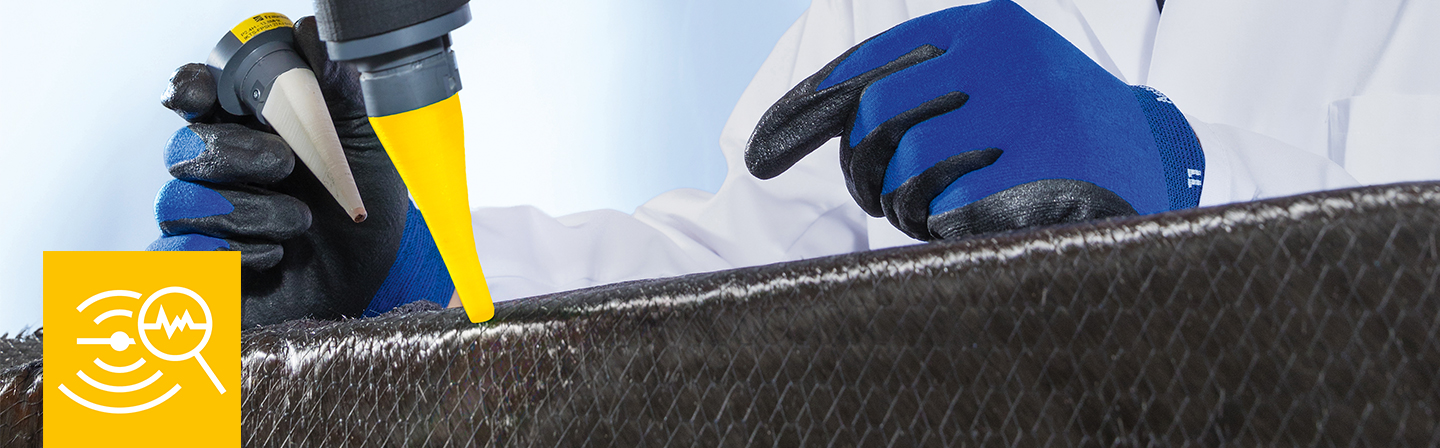
Quality, cost and time are the decisive factors for products and services to succeed in the marketplace. Continuously improving these factors requires deep knowledge of the products: from the development phase, through the production to the application. Quality control through non-destructive testing (NDT) contributes greatly to the accumulation of this indispensable knowledge, its evaluation and use with a view to optimizing processes.
New materials (e.g. composites), manufacturing methods (additive and hybrid methods) and production concepts (flexible production, Industry 4.0) call for novel testing strategies and the necessary components. At the same time, non-destructive testing is expanding its range of application across the entire product life cycle – from raw material evaluation to their usage and recycling.
Testing and monitoring are part of an efficient strategy for making development, production and operation more reliable, economical and competitive. They also meet legal requirements. Fraunhofer IKTS combines its decades of experience in the testing of components and plants with novel measuring technologies, automation concepts and approaches for the interpretation of complex data volumes.
Fraunhofer IKTS is a competent partner for the application and further development of established test methods, such as ultrasonics, eddy current, X-ray and acoustic diagnostics. Depending on the requirements, these can be coupled with or completed by new concepts of laser speckle photometry or optical coherence tomography. If needed, the accredited NDT test lab provides support in the validation and certification of these new methods. The competence portfolio thus goes far beyond that of a classic provider of NDT testing technology.
The traditional strength of IKTS – handling noisy signals – is reflected on the equipment level with adapted sensors and own electronics offering an outstanding signal-to-noise ratio. Own software libraries and the most modern methods of machine learning help to open up the information gained for a more sophisticated use. Measured and operational data collected in experiments are combined with the dynamic simulation model of a component, which enables statements on the performance and expected service life based on a digital twin, leading to specific failure models.
At Fraunhofer IKTS, traditional non-destructive testing is extended consistently to obtain a versatile quality assurance tool. Automation, programmable test manipulators, online visualization of measured values via web clients and the use of standardized interfaces and data formats all ensure the best possible integration with clients’ processes.
In this way, Fraunhofer IKTS supports partners from science and industry in the use of established processes and in achieving a strategic paradigm change towards Industry 4.0.