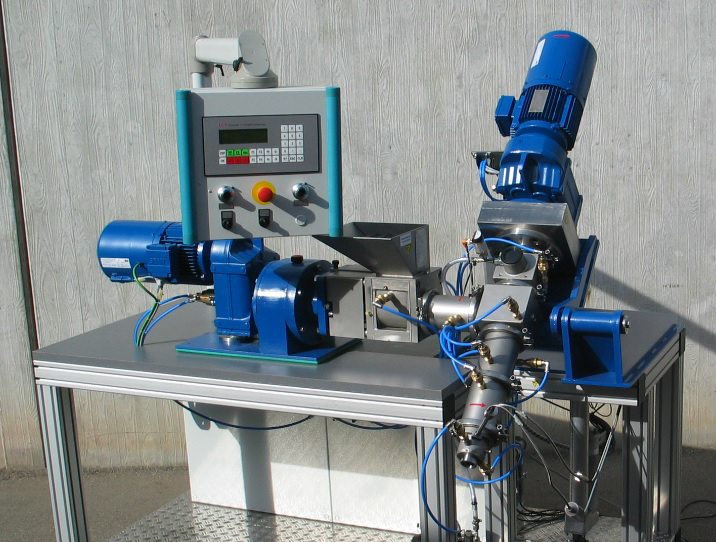
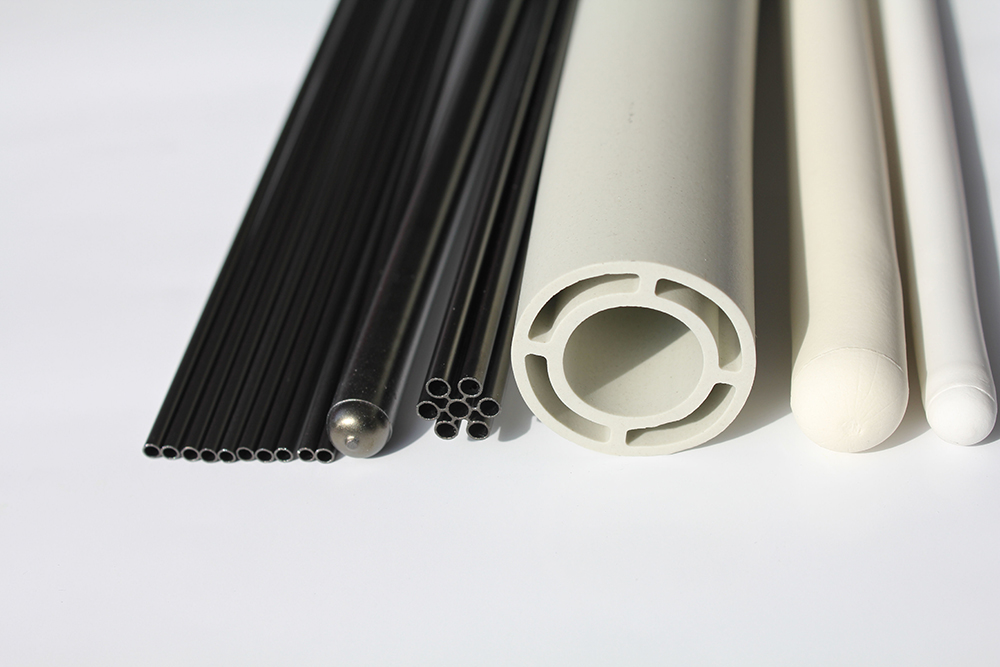
Within our group, the preferred shaping method for ceramics is stiff plastic extrusion of water based plasticized batches. Typically used extruder is shown in Fig. 1. We are working especially on shaping of mixed conducting materials like Sr0.5Ca0.5Mn0.8Fe0.2O3-δ, Ba0.5Sr0.5Co0.8Fe0.2O3-δ, on doped oxide ion conductors like ZrO2:Y, CeO2:Gd or on shaping of catalytic active mixed oxides like LaCoO3 and La1-xSxMn1-yFeyO3-δ) to membranes, pellets and honeycombs. Corresponding to special applications specific requirements have to be realized, e.g. small wall thickness together with high gas tightness, high porosity and sufficient strength or high surface area combined with low pressure drop. To maintain the functionally characteristics of the material by the component realized, the additives used as well as the processing conditions are subjected to strict selection criteria.
Building up of components with optimized fluidic properties requires a narrow interaction between application requirements and the possibilities and limitations of shaping technology. As an example, MIEC membranes (Mixed Ionic Electronic Conductor) needs the lowest wall thickness but a maximal membrane area or packaging density. This is in contradiction to the sensitivity of such filigree components and to the need for a uniform cross section. Therefore, additional manufacturing steps are necessary for building up of complex components, e. g. manual or semi-automatic sealing or joining techniques or a combination of extruded parts to a module. This is illustrated by Fig. 2 showing different membrane tubes and sheath tubes, witch can been combined to modules.
Services offered
- Manufacturing of shaped bodies for catalysis: honeycombs of 200/400 cpsi, mini honeycombs 3 x 3, solid cylinders and hollow cylinders Ø 1–5 mm
- Single-channel membranes for oxygen separation: Ø 3 mm, wall thickness 0.3 mm, Ø 10/15 mm, wall thickness 1 mm
- Multi-channel tubes 7 x Ø 3 mm, wall thickness 0.4 mm
- Special types negotiable
- Processing of customer materials and materials synthesized by ourselves
Technical equipment
- 350-ml-Brabender-lab kneader
- 2-l-Linden-kneader
- 19-mm-Brabender-lab extruder
- 50-mm-ECT-extruder
- Kilns for debinding and sintering, 5 l bis 2.5 m3