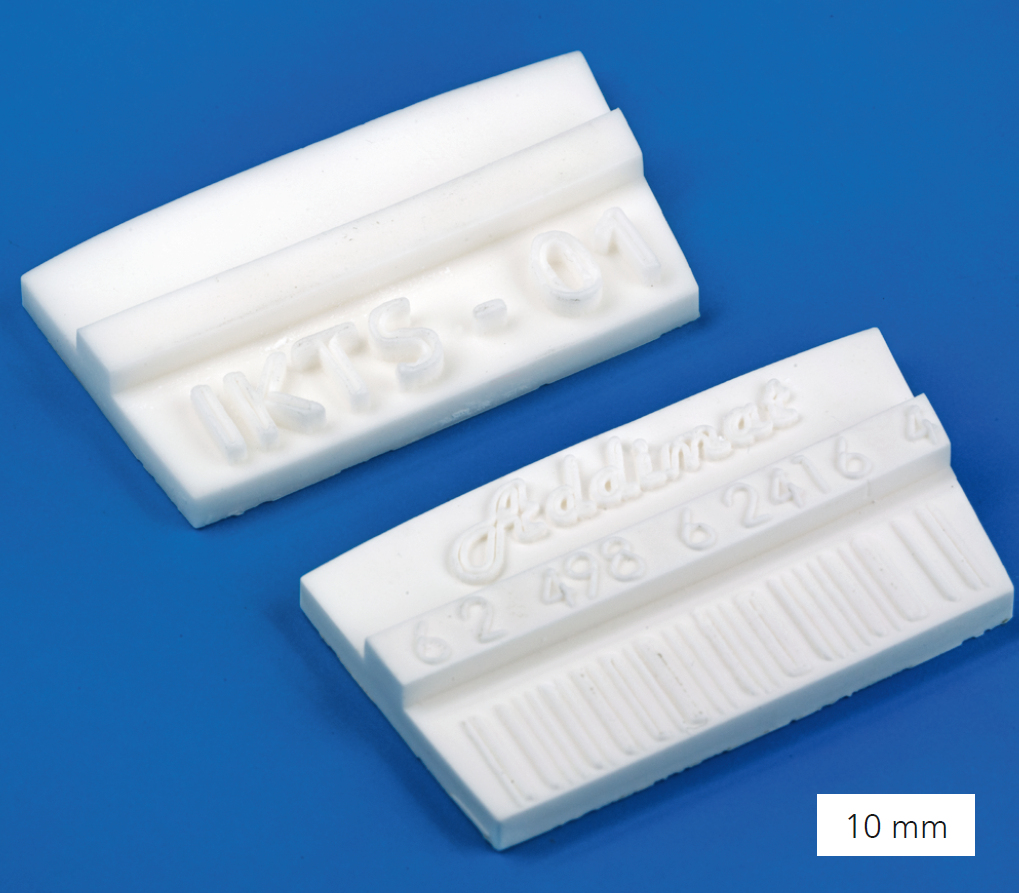
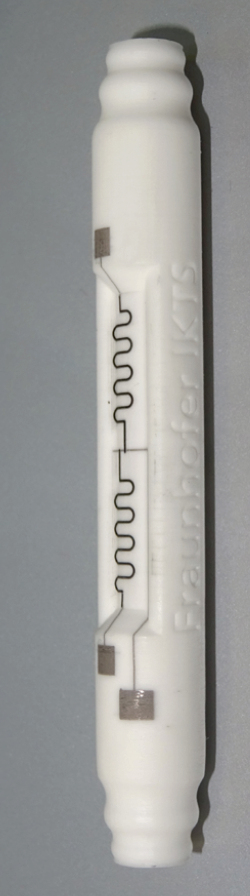
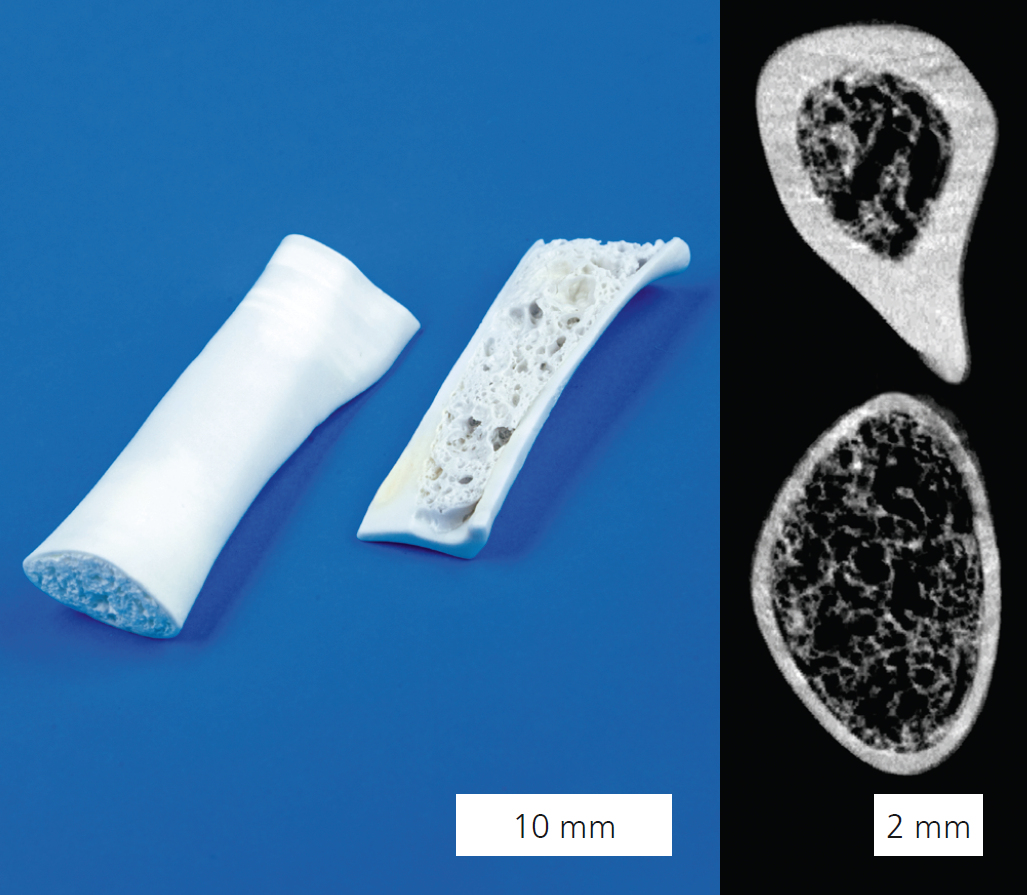
Few manufacturing methods have grown as fast in recent years as additive manufacturing. Fraunhofer IKTS develops additive manufacturing methods and adapts them to be suitable for the 3D printing of ceramic materials. Efforts currently focus on the production of multi-functionalized components. The thermoplastic processes of CerAM FFF (Fused Filament Fabrication) and CerAM MMJ (Multimaterial Jetting) were developed at IKTS. These methods allow to achieve highly complex geometries with varying structural properties, as well as co-manufacturing by combining different complementary materials within one layer. The materials are deposited only where they are required, meaning that no additional tools are needed and less material is required. In accordance with client requirements, material systems can also be characterized and developed for multi-component printing. By combining additive manufacturing with conventional and industrially well-established manufacturing processes, the advantages of each individual process are used to better effect. Functionalized and individualized components or component series can be created cost-efficiently. As part of the CerAMfacturing (EU, GA 678503) and Addimat (ZIM, ZF 4076417EB6) projects, components produced using ceramic injection molding (HP-CIM and LP-CIM) were individualized afterwards by means of the additive manufacturing processes CerAM FFF and CerAM MMJ (Figure 1). A green body, produced by ceramic injection molding, was later supplemented by an individual structure using additive manufacturing. The hybrid component was then debinded and sintered. Thus, it is possible to retroactively modify bulky bodies produced by ceramic injection molding with a functionalized material or to individually mark these components. By combining different manufacturing methods, electrically conductive and insulating properties (Figure 2 – CerAM VPP | aerosol-printing) can be realized within a component in a cost-effective and quick manner. Furthermore, dense-porous structural hybrids (Figure 3 – CerAM VPP | freeze foaming) can be manufactured as potential bone replacement materials. CerAM VPP technology (VAT photopolymerization) is suitable for producing such complex, highly structured and small ceramic components with very good surface properties. It is based on the hardening of light-sensitive suspensions by selective irradiation with light. The project has received funding from the European Union’s Horizon 2020 Research and Innovation Programme under Grant Agreement No 678503.
Services offered
- Suspension, filament as well as feedstock development for multi-material applications
- Technology development and transfer based on additive manufacturing processes or process hybrid