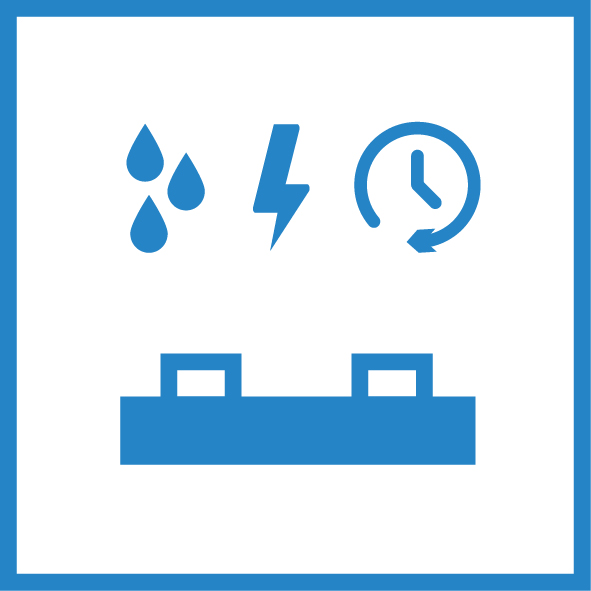
Layer manufacturing and characterization
A comprehensive range of equipment is available to manufacture the required functional layers (various printing and firing technologies), used in line with the client requirements. Some of the printing technologies available are screen printing (planar, tubular, hot-melt) or aerosol-jet, ink-jet, gravure, dispense and dispense-jet printing (see Downloads).
All relevant functions are determined and collated with the target criteria defined in the statement of work in the context of the subsequent layer characterization, which takes place in accordance with DIN 41850. For this purpose, numerous geometric, mechanical and electric variables are routinely determined following firing, in order to verify and optimize the tailored properties targeted.
The Thick-Film Technology group with its focus on functional printing has a large number of measuring stations and equipment available to achieve this. In addition to the standard tests (coat thickness, roughness, temperature-dependent resistance, suitability for soldering, etc.), specific process effects (e.g. variations in firing, screen-printing tolerance values) can also be examined and modified in order to be able to represent the effect on the resulting layer properties.