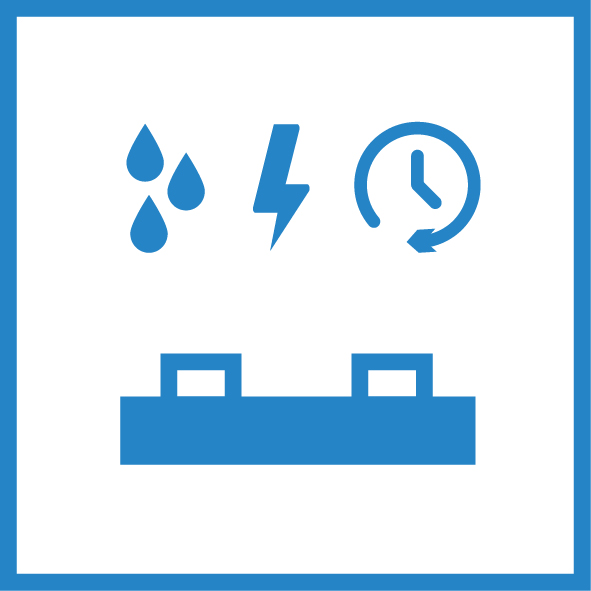
Schichtherstellung und -charakterisierung
Für die Herstellung der benötigten funktionellen Schichten steht ein umfangreicher Gerätepark zur Verfügung (verschiedene Druck- und Einbrandtechnologien), der entsprechend der Kundenanforderungen genutzt wird. Verfügbare Drucktechnologien sind beispielsweise Siebdruck (planar, tubular, Hot-Melt) oder Aerosol-Jet-, Ink-Jet-, Gravur-, Dispens- und Dispens-Jet-Druck (siehe Downloads).
Innerhalb der anschließenden Schichtcharakterisierung nach DIN 41850 werden alle relevanten Funktionseigenschaften ermittelt und mit den im Lastenheft definierten Zielkriterien abgeglichen. Dabei werden nach dem Einbrand zahlreiche geometrische, mechanische und elektrische Größen routinemäßig bestimmt, um die angestrebten maßgeschneiderten Eigenschaften der Schichten zu verifizieren und zu optimieren.
Dazu verfügt die Gruppe Dickschichttechnik mit Schwerpunkt Functional Printing über ein umfangreiches Angebot an Messplätzen und Ausrüstungen. Neben den Standardtests (Schichtdicke, Rauheit, Widerstand in Abhängigkeit der Temperatur, Löteignung, etc.) können auch Prozesseinflüsse (z. B. Einbrandvariationen, Siebdrucktoleranzen) gezielt untersucht und verändert werden, um den Effekt auf die resultierenden Schichteigenschaften abbilden zu können.