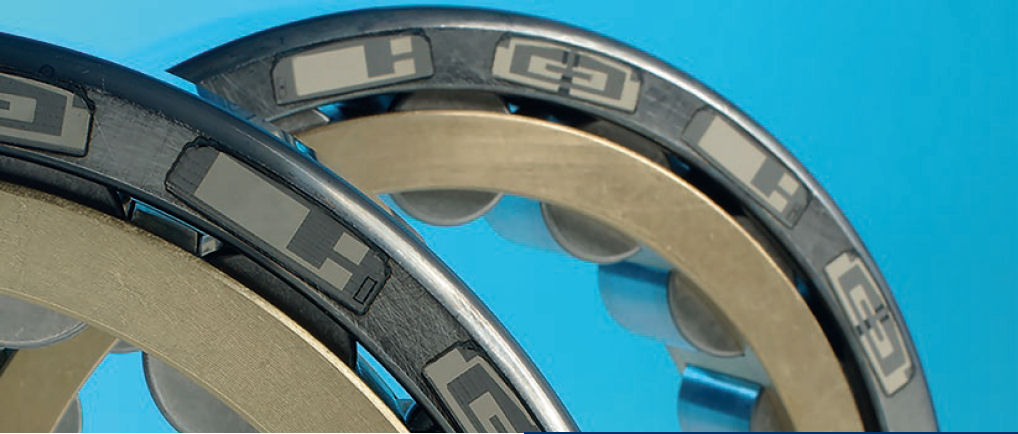
Ceramic thick-film technology is typically used to produce functional layers, e.g. for ceramic circuit boards or sensors. The technology uses pastes and is based on the typical process sequence of screen printing, drying, and firing. Continuous furnaces are used for high-throughput firing. The deposition of the required functional pastes is currently limited to planar or tubular substrate bodies due to technological and plant-related reasons. For the first time, researchers at the Fraunhofer Institutes IKTS, ILT and IZM have now succeeded in printing sensor layers directly onto large steel components, thus functionalizing them locally. Due to their size and heat sensitivity they would melt if sintered in the furnace.
3D thick films without screens and sintering furnaces
The objective of the Fraunhofer “InFuroS – Integrated functionality on robust structural elements” research project was to overcome the restrictions of classic thick-film technology by using modern 3D printing technologies (dispensing, aerosol-jet printing). Instead of the usual furnace processes, we use fast laser treatments to sinter the required functional layers. The focus is on the development of adapted paste systems and laser processes for the deposition and sintering of insulation, conductor, resistor and piezoelectric layers on solid steel components (1.4016, 1.3035) to generate strain, temperature and body sound sensors.
For the development of laser-sinterable insulation pastes, we selected suitable thick-film glasses of different compositions which differed in terms of their glass transition temperatures. We optimized specific glass properties by adding different dispersing phases which affect, among other things, the absorption properties or glass viscosity during laser treatment. At Fraunhofer ILT, the glass composites were characterized in terms of their optical properties (absorption) and at IKTS in terms of shrinkage and other layer properties (adhesive strength, insulation resistance).
Over the course of the project, we developed more laser-sinterable pastes, such as conductor path pastes (Ag-based), resistance pastes (RuO2-based) for temperature and strain sensors, as well as piezoelectric pastes based on lead zirconate titanate (PZT) for structure-borne sound sensors. Thanks to their significantly reduced interaction times in laser sintering, piezoelectric layers combined with steel, as well as insulation and electrode layers, showed particularly improved material properties compared with furnace-sintered structures.
To demonstrate the project results, sensors for measuring strain and structure-borne sound were printed and laser-sintered onto the shell of a roller bearing.