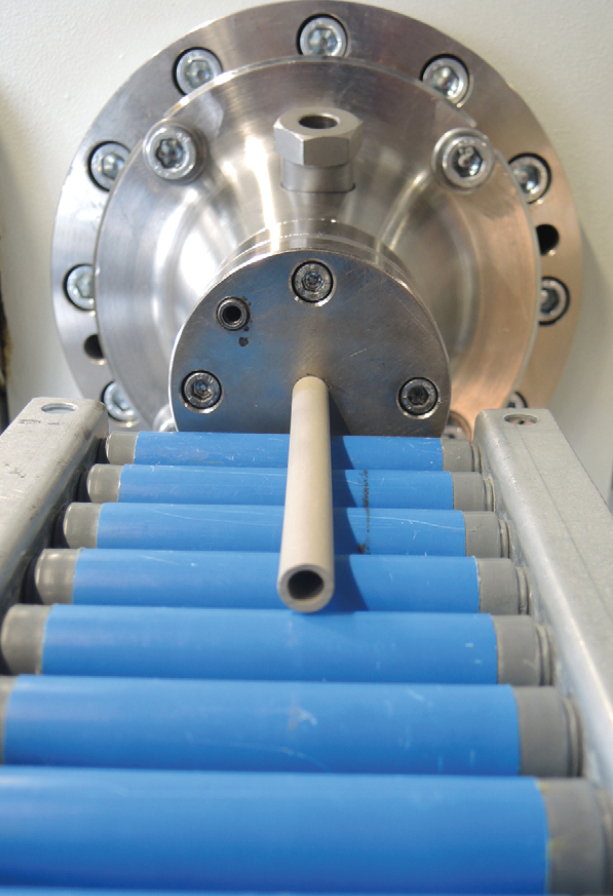
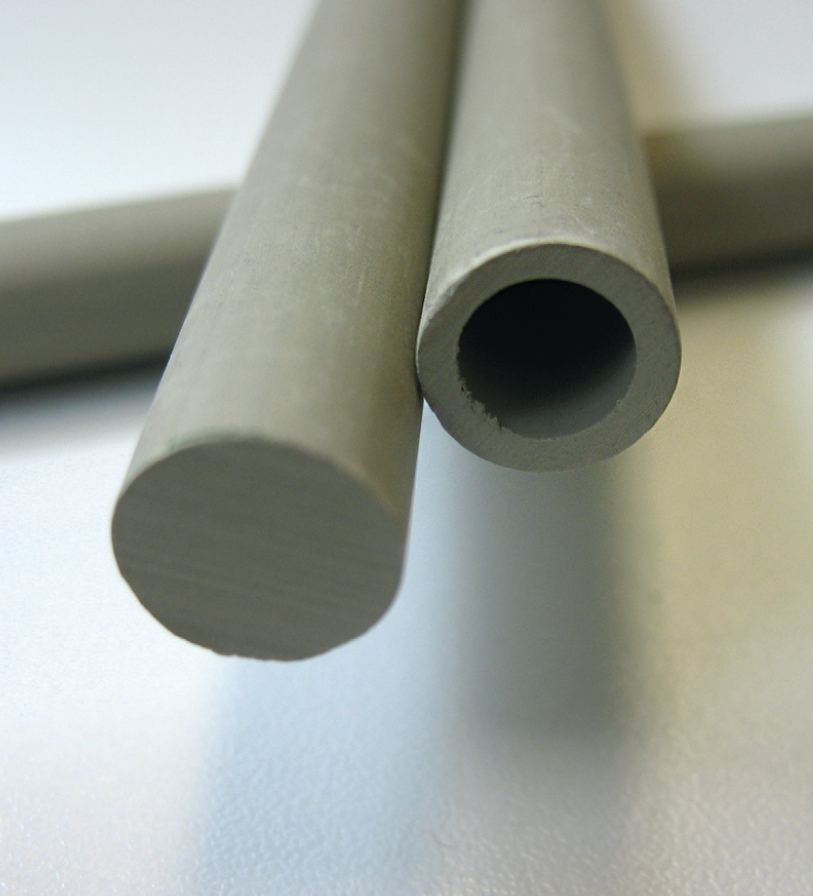
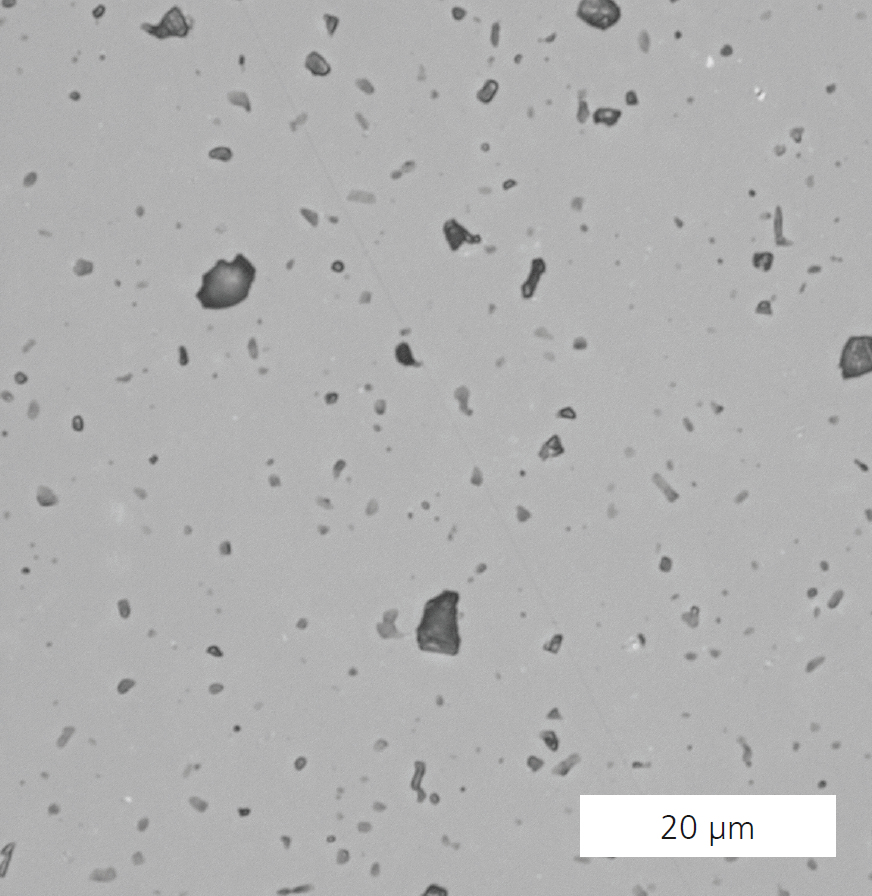
Silicon carbide sintered in a pressureless process (SSiC) can have sintered densities of up to 98 %. Due to ist monophasic structure and purity, SSiC is characterized by a better high-temperature stability and corrosion resistance compared with more traditional SiC materials, such as RSiC, SiSiC, LPS-SiC and NSiC. Up to now, SSiC components have been produced predominantly through uniaxial or isostatic pressing, which has its limitations regarding possible shapes. Long and filigree profiles with a constant cross section, such as rods, tubes and honeycombs, can only be realized by extrusion which, up to now, has not been available for SSiC, or has been possible only with significant quality losses regarding density and mechanical strength. Challenges in handling the ceramic extrusion compound are the primary reason for this situation. The compounds have to contain fine, submicron powders in combination with comparatively high amounts of binders and process aids, resulting in relatively low green densities in the extruded parts. In addition, the necessary sintering aids – boron and carbon – have to be dosed accurately and distributed homogeneously within the compound. Since established additives, such as black carbon or resins, impede the dispersion and, ultimately, the shaping, they are less suited for this kind of shaping. Furthermore, the crack-free drying and the pyrolysis and sintering processes prove to be very demanding, too. It is necessary to facilitate a linear sintering shrinkage of up to 20 % in order to prevent deformation or even the creation of defects. As part of a feasibility study at Fraunhofer IKTS, a cold-plastic compound for the SSiC processing was developed. As a result, the extrusion of various geometries, such as rods, tubes and honeycombs, was successfully demonstrated. The SiC particle size and the inserted additives were chosen to attain good processability with low wear on the die and high green density in the extruded parts. The organic binders have been adapted in order to reach a high concentration of well dispersed carbon after the pyrolysis. Within the scope of this study, test parts with densities up to 96 % of theoretical density and a linear shrinkage of up to 17 %, were prepared through pressureless sintering. Based on the results achieved, even higher densification might be possible by further modifying the cold-plastic compound composition and adapting the process parameters.
Services offered
- Development and optimization of cold-plastic compounds for the production of SSiC extrudates
- Application-related design and development of extrudable SSiC components