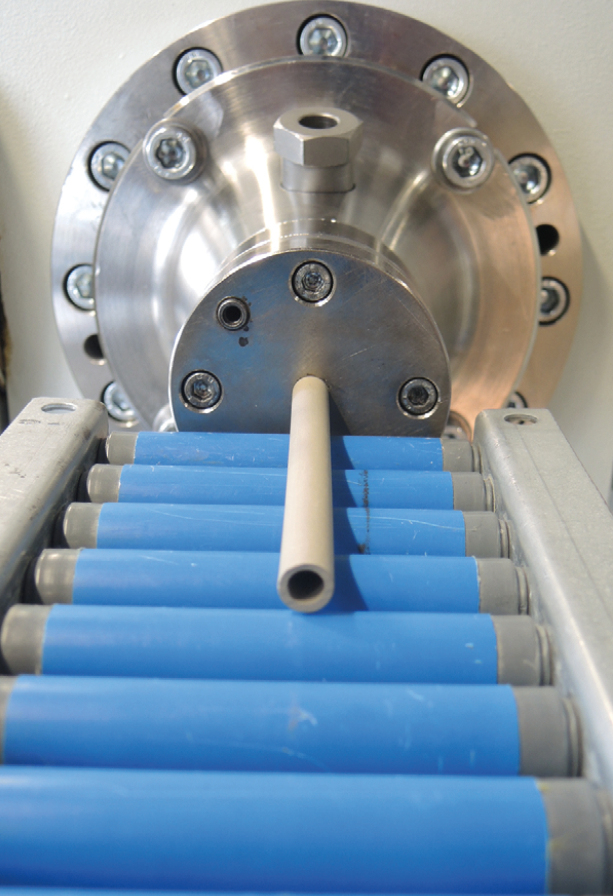
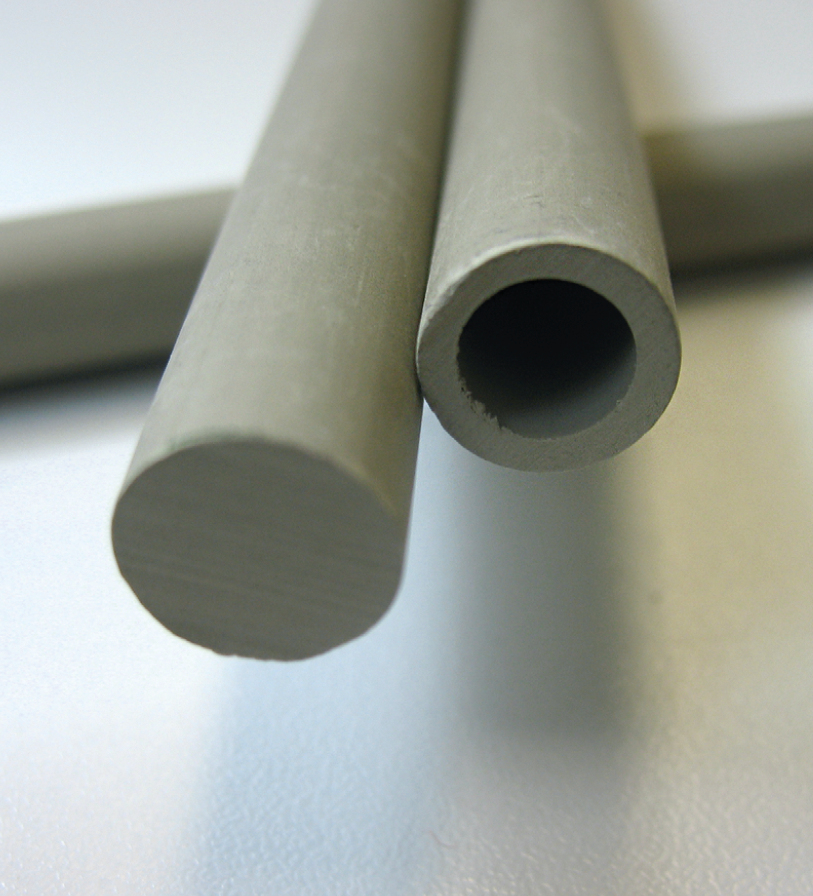
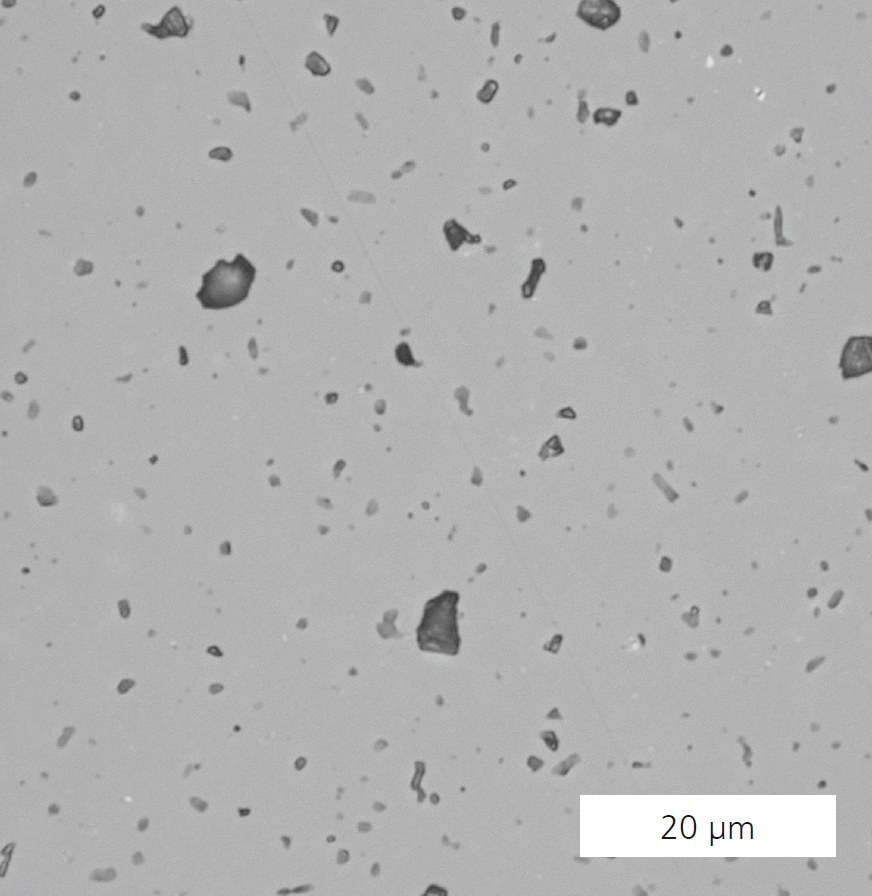
Drucklos gesintertes Siliciumcarbid (SSiC) kann Sinterdichten von bis zu 98 % aufweisen und ist durch seinen einphasigen Aufbau und seine Reinheit anderen klassischen SiC-Werkstoffen, wie RSiC, SiSiC, LPS-SiC und NSiC hinsichtlich des Hochtemperaturverhaltens und der Korrosionsstabilität deutlich überlegen. Bisher erfolgt die Formgebung von SSiC-Bauteilen überwiegend mittels uniaxialem oder isostatischem Pressen, was Einschränkungen in der Geometrie mit sich bringt. Lange und filigrane Profile mit konstantem Querschnitt, wie Stangen, Rohre und Waben können nur über Extrusion in Form gebracht werden. Das war bisher für SSiC nicht oder nur mit deutlichen Qualitätseinbußen bzgl. Dichte und Festigkeit möglich. Die Ursache liegt in der anspruchsvollen Verarbeitung der keramischen Extrusionsmassen. Diese müssen feine Submikronpulver in Kombination mit relativ hohen Anteilen an Binde- und Prozesshilfsmitteln enthalten. Daraus resultieren vergleichsweise geringe Gründichten im extrudierten Bauteil. Die für das drucklose Sintern erforderlichen Additive Bor und Kohlenstoff müssen zudem sehr genau dosiert und in der Extrusionsmasse homogen verteilt sein. Mit gängigen Additiven wie Ruß oder Harz ist dies nur eingeschränkt möglich, da beide die Dispergierung und letztlich die Formgebung erschweren. Sehr anspruchsvoll sind neben der rissfreien Trocknung auch die Pyrolyse und Sinterung. Dabei gilt es vor allem die lineare Sinterschwindung von bis zu 20 % nicht zu behindern und dadurch einen Verzug oder gar die Bildung von Defekten zu riskieren. Am Fraunhofer IKTS wurde im Rahmen einer Machbarkeitsstudie eine kaltplastische Masse für die SSiC-Herstellung entwickelt, mit der sich unterschiedliche Geometrien, wie Stangen, Rohre und Waben extrudieren lassen. Die Wahl der SiC-Partikelgröße und der eingesetzten Additive zielt dabei auf eine gute Verarbeitbarkeit mit geringem Werkzeugverschleiß und eine möglichst hohe Gründichte ab. Die Anpassung des organischen Bindersystems ermöglicht nach der Pyrolyse eine ausreichend hohe Konzentration fein verteilten Kohlenstoffs im Bauteil. Im Ergebnis dieser Arbeiten ist es gelungen, homogene Testkörper zu extrudieren und mittels drucklosem Sintern bis zu 96 % der theoretischen Dichte zu erreichen – bei einer linearen Schwindung von bis zu 17 %. Zusätzliche Anpassungen hinsichtlich der Zusammensetzung der kaltplastischen Masse und der Prozessparameter können zu einer weiteren Verdichtung des Gefüges führen.
Leistungsangebot
- Entwicklung und Optimierung kaltplastischer Massen zur Herstellung von SSiC-Extrudaten
- Anwendungsangepasste Konstruktion und Entwicklung extrudierbarer SSiC-Bauteile