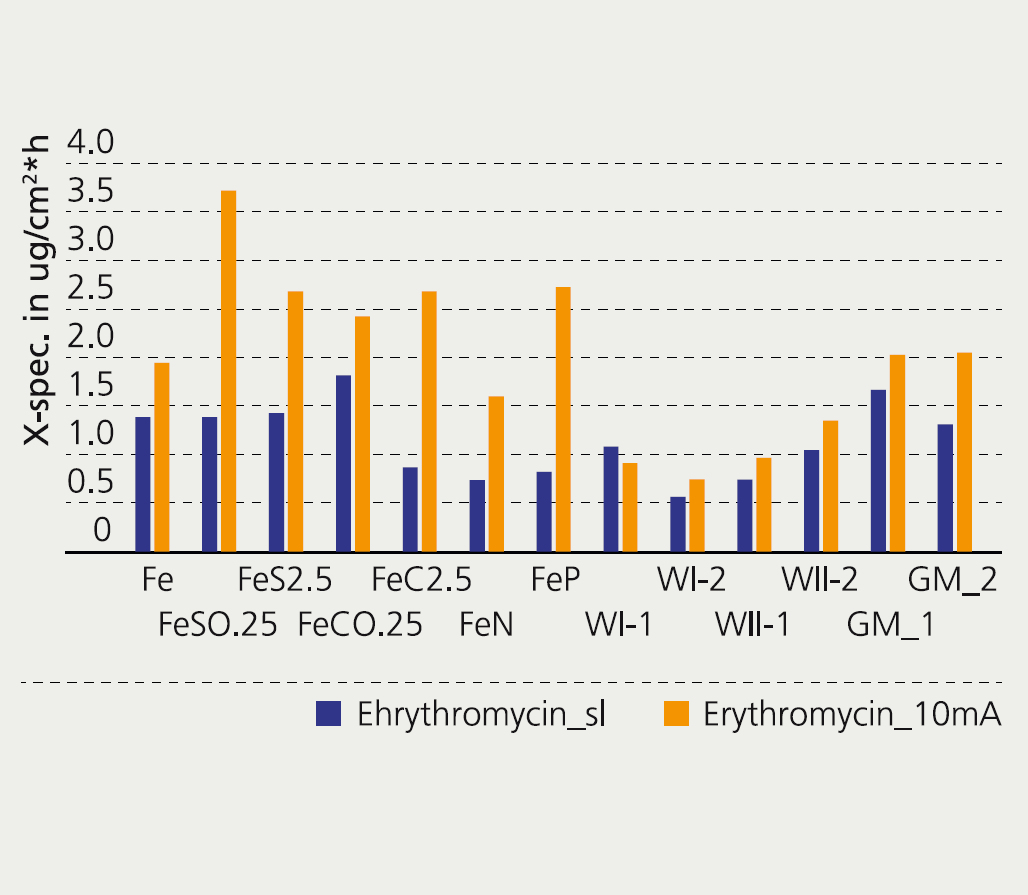
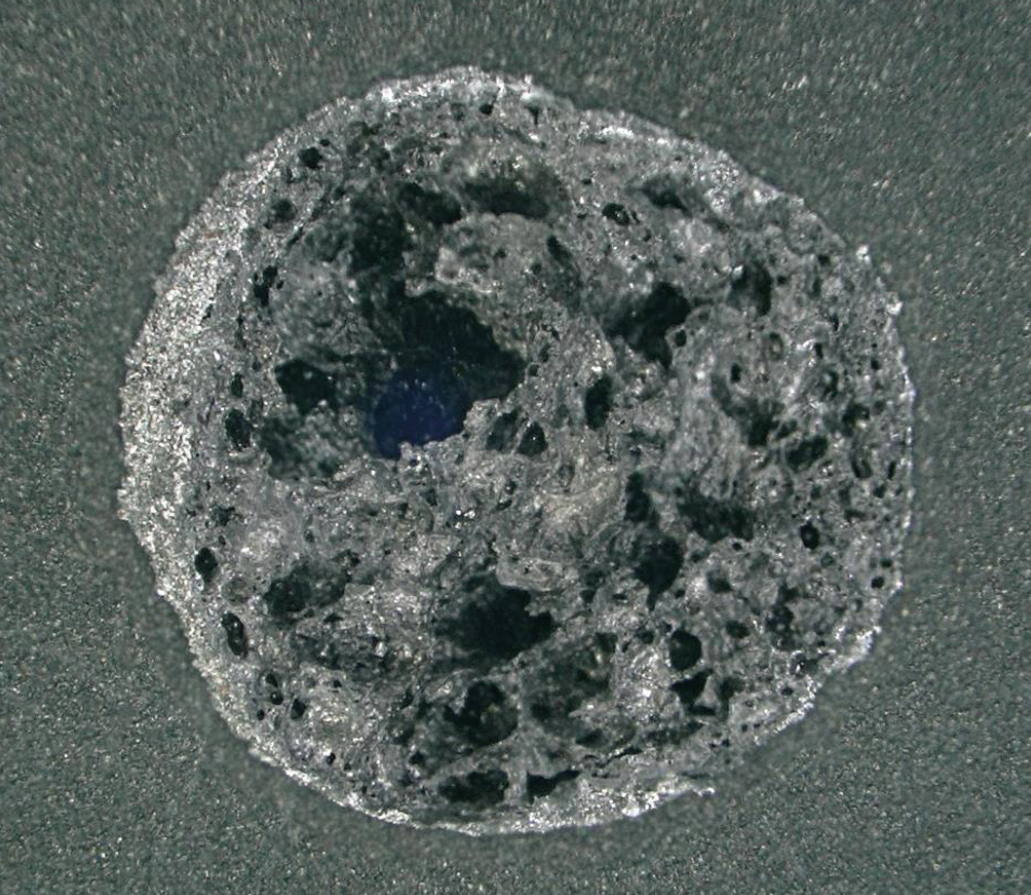
A growing part of pharmaceuticals, pesticides or their residues can be found in ground and surface water, from which our drinking water is also made. This is especially true for urban agglomerations and areas with intensive agriculture. While these substances are only present in very small concentrations, they are nevertheless relatively stable and have undesirable biological effects. For example, antibiotic residues contribute to the development of multi-resistant germs or, as in the case of estrogens, they are considered to be partly responsible for the increase in fertility disorders. Unfortunately, current methods of municipal wastewater treatment – one of the major entry paths into the water cycle – have proven unfit for removing many of these substances.
Our approach: iron alloys on ceramic foam
Within the BMBF joint project KERAMESCH, Fraunhofer IKTS has developed materials with which pharmaceutical and pesticide residues can be removed from the water through the combined action of reduction and adsorption. This can be achieved, for example, with iron alloys with a special composition which are applied onto floatable ceramic foam beads. Extensive investigations regarding the influence of the iron composition show that the sulfur content is the alloys’ most important feature: a high content strongly promotes the removal of pollutants (example: erythromycin in Figure 1). The effect can usually be enhanced through the cathodic polarization of the iron. In the reductive transformation of the active substances, materials such as diclofenac are rendered harmless by cleaving off the chlorine atoms, or by attacking other functional groups. However, the reactivity of the iron decreases rapidly as a result of the formation of a corrosion layer, making it necessary to regenerate the iron surface constantly.
From material to floatable catalyst
The challenge was to develop a mechanically stable ceramic carrier material with a maximum density of 0.5 g/cm³ to make the iron-coated foam beads float. To achieve this, a clay suspension was foamed directly by introducing air while adding a surfactant. The resulting ceramic foam was filled into spherical molds, dried and sintered. The diameter of the beads was defined to be 20 mm so that they would float after being coated with a 500 μm thin layer of iron alloy. A stable suspension of the iron powder was developed for coating the clay foam beads. After drying, the iron layer was sintered at 1150 °C under inert gas. In order to treat larger volumes of water in this way, the next step will be to test the novel catalysts in fluidized bed reactors. Such reactors also have the advantage that the reaction layer is renewed continuously as a result of natural abrasion.