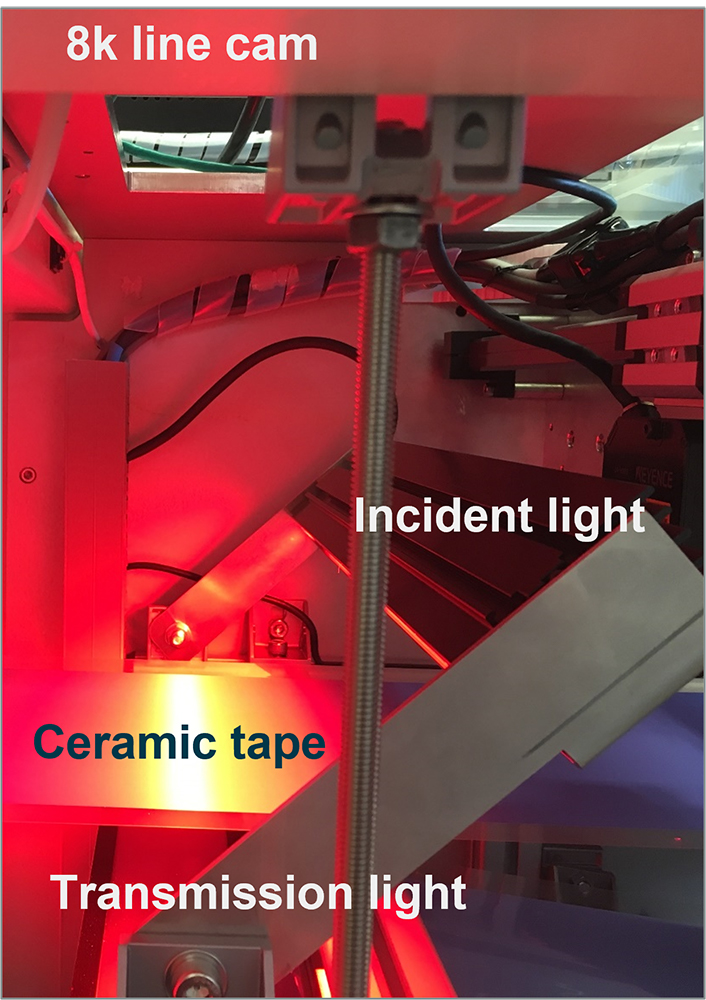
Optical process monitoring is an established method for in-line monitoring of production and manufacturing processes. The fast, non-contact and non-destructive method is applied in numerous industries, such as the automotive industry, food industry, packaging industry or additive manufacturing. Fraunhofer IKTS is currently working on solutions for in-line monitoring of ceramic tape casting processes and moisture measurement in the processing of cardboard packaging.
In-line monitoring and process control of ceramic tape casting processes
Ceramic tape casting is a high-throughput technology for the efficient and cost-effective production of planar ceramic structures which, depending on the material, form the basis for numerous applications. Quality assurance of the casted tapes currently takes place mainly downstream in the context of manual quality control. Therefore, fluctuations in density or certain defects (holes, streaks, agglomerates, etc.) cannot be reacted to directly by adjusting the casting parameters. For this purpose, Fraunhofer IKTS has integrated an in-line monitoring system with laser triangulation for wet and dry film thickness measurement, a line scan camera with alternating incident and transmitted light illumination for defect detection, and an eddy-current system for determining dielectric properties into an existing tape casting line at the Hermsdorf site. The focus is also on automatic defect detection and classification of the defects that occur. In a next step, the research results obtained so far will be implemented directly in the tape casting plant to enable immediate process control.
Moisture measurement using organic infrared detectors to control cardboard converting machines
The moisture content of cardboard has a significant influence on its processability, especially in forming processes. Currently, residual moisture is only determined on a random basis since the costs for measuring systems are very high compared to the material costs. To address this issue, Fraunhofer IKTS uses novel, commercially available and cost-effective NIR detector elements based on organic electronics. These detector elements are used in a miniaturized optoelectronic interrogation unit developed at IKTS, which can simultaneously interrogate two wavelengths (absorption wavelength of the solvent and reference wavelength). On this basis, a complete near-infrared spectroscopic measurement system was built and it was demonstrated that this approach is suitable for monitoring board webs with moisture contents in the range of 0 to 20 mass percent. The key advantage is the lower cost per measurement point (by a factor of 10–100). This makes it economically viable for the first time to set up line detectors for monitoring board webs of large width (up to 1 m).