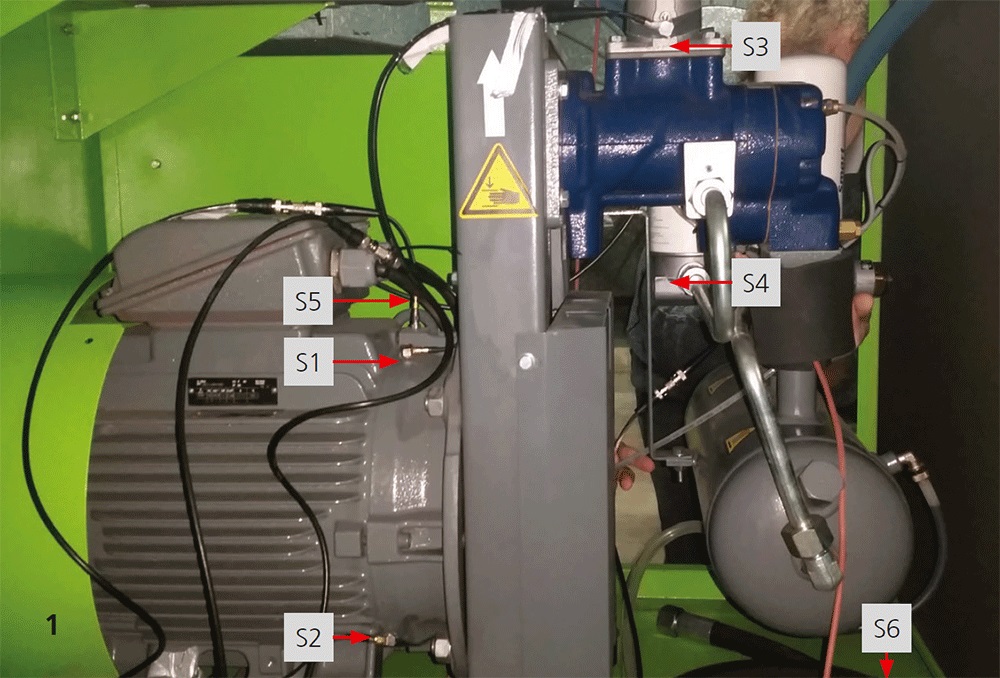
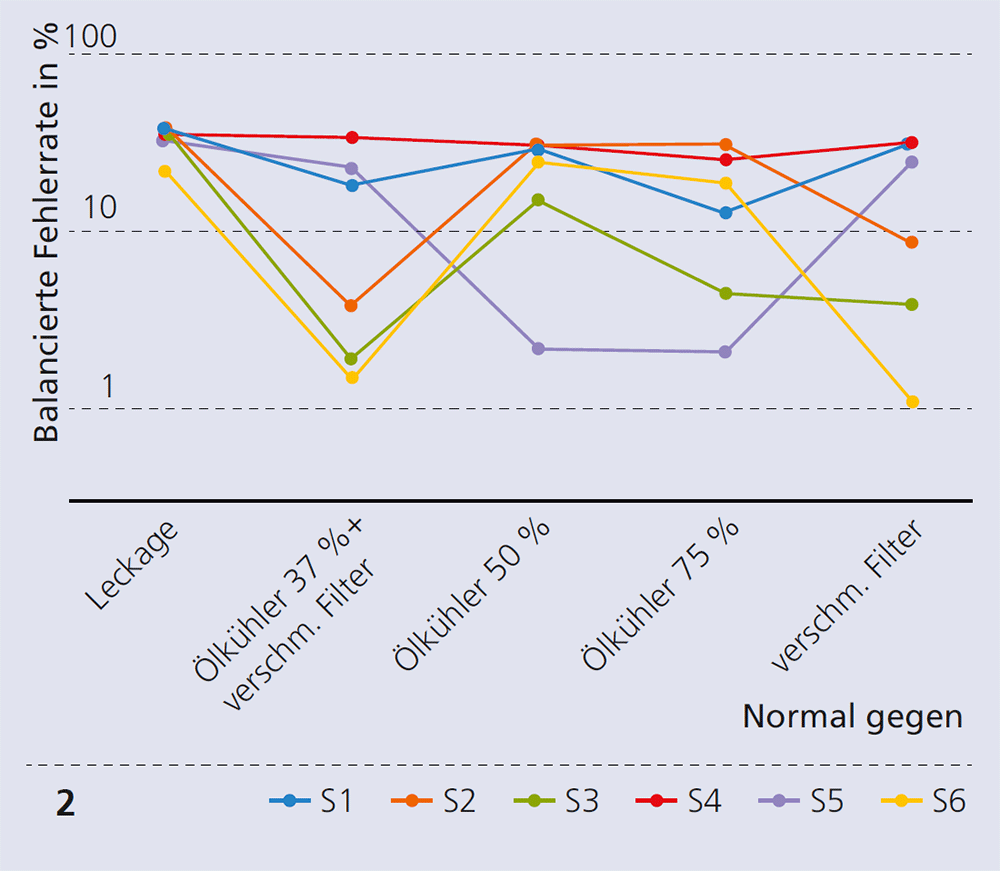
Many processes in industry, transport and other areas of society require the stable operation of compressors. If a compressor fails, this leads to downtimes and repair times and thus to considerable economic damage. The operational stability, however, is not very well developed with regard to maintenance, which requires a new approach that integrates various technologies.
Less repair and servicing, more cost and energy efficiency
As part of the "CompWatch" project, we are working with the companies Petko GmbH and SONOTEC GmbH to develop sensors and processes that enable event-oriented maintenance intervals instead of fixed ones. The aim is the early detection of possible failures so that downtimes and repair times are reduced and unnecessary service work is avoided. This leads to cost savings. Due to the energetic relevance of the compressors, the project also makes a contribution in the area of energy efficiency. In addition, the underlying process should be applicable to other products across all technologies.
Anomaly detection through acoustic signals, artificial intelligence and machine learning
Acoustic signals and vibration data contain signatures that allow conclusions to be drawn about the condition of the compressor and its trend. The data is evaluated using methods of artificial intelligence and machine learning. Oftentimes all errors must be known while designing the models in order to be able to recognize them later. Our approach is that we predict and determine abnormal conditions (anomalies) without such prior knowledge. This would facilitate quick and easy integration into new environments and running systems.
Different types of sensors for anomaly detection were used in the experiments conducted in the project. The sensor positions (Figure 1) were chosen in such a way that as many components as possible could be monitored. Figure 2 shows the failure rates (scaled logarithmically) for differentiating between an error and the normal state for each sensor. The lower the failure rate, the fewer false alarms occur and the better the detection of defects works. A leak in the compressed air system and contamination of the air filter can be found particularly well with the airborne sound sensor. The leak in the cover of the oil cooler was also easily detected. The individual components are currently being integrated into a demonstrator and will then be evaluated on compressors.
Funding body: Bundesministerium für Bildung und Forschung (BMBF)
Project sponsor: Projektträger Karlsruhe (PTKA)
Funding reference: 02K18K012
Project partners: Petko GmbH, SONOTEC Ultraschallsensorik Halle GmbH