Author: Hilde-Josephine Post | Translation: Stephanie Anderseck
Clever hardmetal developments address critical raw material dependency and CMR health requirements
Hardmetals will celebrate their 100th anniversary next year and have now been largely optimized. Nevertheless, there are current challenges that lead to novel developments and competitive advantages through higher wear resistance and lower costs, as well as to the efficient use of resources.
"Two fundamental challenges are currently triggering our research work," reports Dr. Johannes Pötschke, head of the Hardmetals and Cermets Group at Fraunhofer IKTS. "Binder metals such as cobalt have been classified as CMR (cancerogenic, mutagenic, reproductive toxicant) substances that are critical to health. This is currently a major concern for hardmetal manufacturers. It entails complex protective measures during production, which makes the production of conventionally composed hardmetals seriously more expensive," continues Dr. Pötschke. The group manager sees the second challenge in the uncertain procurement of raw materials: "Critical raw materials (CRM) such as tungsten are a concern for many manufacturers, which has become even more pertinent this year due to the political situation." Fraunhofer IKTS has novel solutions ready to meet these challenges, which are also economical, powerful and suitable for a wide range of applications: from mining and construction machinery to agricultural and construction vehicles and the tool industry.
Intelligent solutions: Substitution of CMR materials and optimization of microstructure design or hardmetal composition
Three basic approaches to solving this problem have been identified: "On the one hand, we can substitute the CMR raw materials, which are critical to health, or we can also produce binder-free hardmetals, with at least the same performance of the novel hardmetals. On the other hand, we increase the service life of hardmetals by changing the compositions in a defined way. And finally, we are also able to specifically adjust the structural local chemical makeup by means of "microstructure design" of the hardmetal component."
Hardmetals are composite materials that conventionally consist of two classes of materials: a ceramic hard material and a metal. The hard materials are formed from carbide or nitride powders. The metal serves as a binder that holds the hard material together and is largely responsible for the toughness characteristics as well as the elastic deformation of the material.
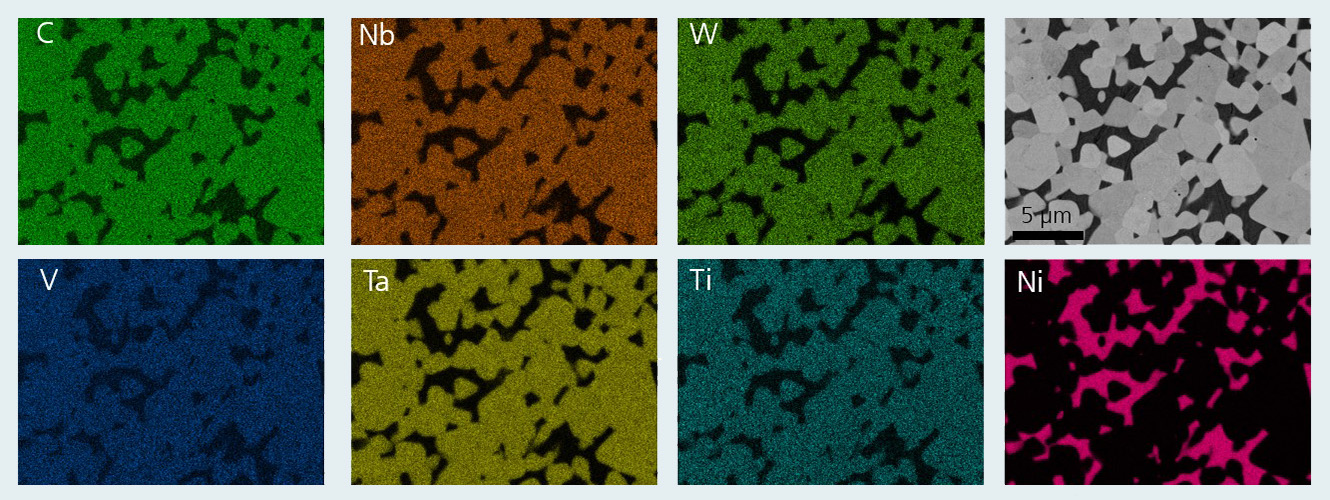
High-entropy hard materials solve resource and CMR problems at the same time
High-entropy hard materials composed of several metal elements are among the new developments at IKTS. Dr. Pötschke explains: "Until now, we only used the compound of two elements as a hard material in a hardmetal, typically tungsten carbide (WC) made from the elements tungsten (W) and carbon (C). Now, we build a novel hard material from at least five metal elements of the 4th to 6th subgroup of the periodic table plus carbon as carbide former." Tungsten, which is considered a raw material critical to procurement, can thus be substituted or its content significantly reduced. The researchers use elements such as titanium, niobium, tantalum, chromium and molybdenum in the same ratio. "In this way, we generate the state of high disorder and create stresses in the material that lead to higher hardness, for example," the group leader continues. These novel hard material grains can be processed into high-entropy hard material composites by mixing them with metal binders such as nickel or iron-based substances and then sintering. The health-critical binder cobalt can also be substituted and comparable hardnesses and toughnesses are achieved. "With our high-entropy hard material composites, we offer powder and blank manufacturers the possibility of solving the CMR health issue. This even leads to lower production costs, as the separate CMR protection measures can be omitted," Dr. Pötschke is pleased to say.
Varying the metal elements and bonding with carbon or nitrogen allows a high variety of hard materials with user-specific properties in terms of hardness, strength, toughness, and resistance to oxidation and high temperatures. A tunnel boring machine in mining, for example, has wear plates on the sides that keep out rockfall when drilling. High-entropy hard materials are suitable here because the focus is primarily on high hardness and less on impact stresses. Higher composite hardness extends the service life of components. "In this way, we are making a contribution," says Dr. Pötschke, "to reducing the hardmetal manufacturers' dependence on resources."
Less weight thanks to high-entropy hard materials saves energy for heavy equipment in the construction and mining industries
In some applications, the weight of the carbides, i.e. components, comes to the fore. Conventional hardmetals, which consist of tungsten carbide, have a very high density. Dr. Pötschke compares: "One liter of hardmetal weighs around 15 kg. This is where the high-entropy hard materials show their advantages because they are much lighter. A liter then weighs only 8 kg or less. And moving less mass for the same amount of work helps save energy." This can be relevant for mining, construction or agricultural machinery.
Graded hardmetals with adapted microstructure design extend the service life of mining buttons and punching tools enormously
The second, already mentioned hardmetal optimization method adjusts the microstructure design of hardmetals while keeping the material composition the same over the entire part compared to conventional solutions. The resulting success: improved mechanical properties such as increased hardness by several 100 HV units (Vickers hardness) with the same fracture toughness. The problem of "either hard or tough" is therefore a thing of the past!
Where, for example, high-strength steel strips are cut, tools are required that have a tough core as well as a hard surface. Hardmetals with a hardness-fracture toughness gradient turn out to be favorites here. The differences in mechanical properties between the edge and the core are determined by the content of the metal binder, the hard material grain size or the structural composition. "Our gradient hardmetals are also proving beneficial in mining, for example for tools such as buttons that sit on the front of tunnel boring machines and crush the rock. We have already been able to test this successfully with a customer. It led to an increase in the service life of the buttons of over 30 percent," reports the Group Manager. According to Dr. Pötschke, graded hardmetals with an adapted microstructure design can also be very advantageous for punching tools: "This can increase punching times by a factor of 10 to 100. The tool thus has to be changed much less frequently, which saves immense man-hours and thus costs." Material usage is also reduced, which conserves resources.
Binder-free hardmetal tools cut titanium and last 10 x longer
In order to solve the CMR health problem, Fraunhofer IKTS is pursuing new approaches, namely using binder-free hardmetals. An adapted microstructure design plus nanoscale hard materials results in high-performance tools whose hardness is several 100 HV units higher than that of commercial ultrafine hardmetals for the same fracture toughness. "Binder-free hardmetals are ideal for wear protection, for example as a starting material for press punches or focusing tubes for waterjet cutting. We have already implemented the latter with customers," says Dr. Pötschke. "By developing binder-free hardmetals that have hardnesses of 3000 HV, we have helped develop the hardest type of hardmetal in recent years," states Dr. Pötschke proudly. These can be used for cutting extremely hard nickel- and titanium-based materials. The group leader explains, "We were able to optimize the hardmetals in such a way that the service life of the cutting tools increased at least tenfold."
Application-specific hardmetal solutions hold great potential and open up competitive advantages for mining, construction and agricultural machinery
Fraunhofer IKTS supports manufacturers and users with regard to energy and cost savings and thus to achieve more competitiveness. "We help to develop, optimize and test application-specific solutions. We are able to produce prototypes or pilot series for field trials. Our unique selling proposition results from many years of experience coupled with a holistic view of the process chain, including in-depth characterization," says Pötschke. When it comes to complex-shaped hardmetal components, the research team also uses additive manufacturing processes, such as binder jetting for prototype production. For example, helical cooling channels can be integrated into cutting tools or spaces for sensors. Additive processes also offer enormous potential when near-net-shape hardmetal blanks need to be made available quickly. "New partners with new applications are very welcome, also with regard to the promising additive manufacturing of hardmetal components," concludes Dr. Pötschke.
Further information
- IKTS-Group "Hardmetals and Cermets"
- Project: "Novel hard phases for hardmetals, MMC and thermal spraying"
- Project: "3D printing of hardmetals"
Stay informed: You are welcome to subscribe to our newsletter, read our other blog articles and follow us on LinkedIn, Instagram and YouTube.