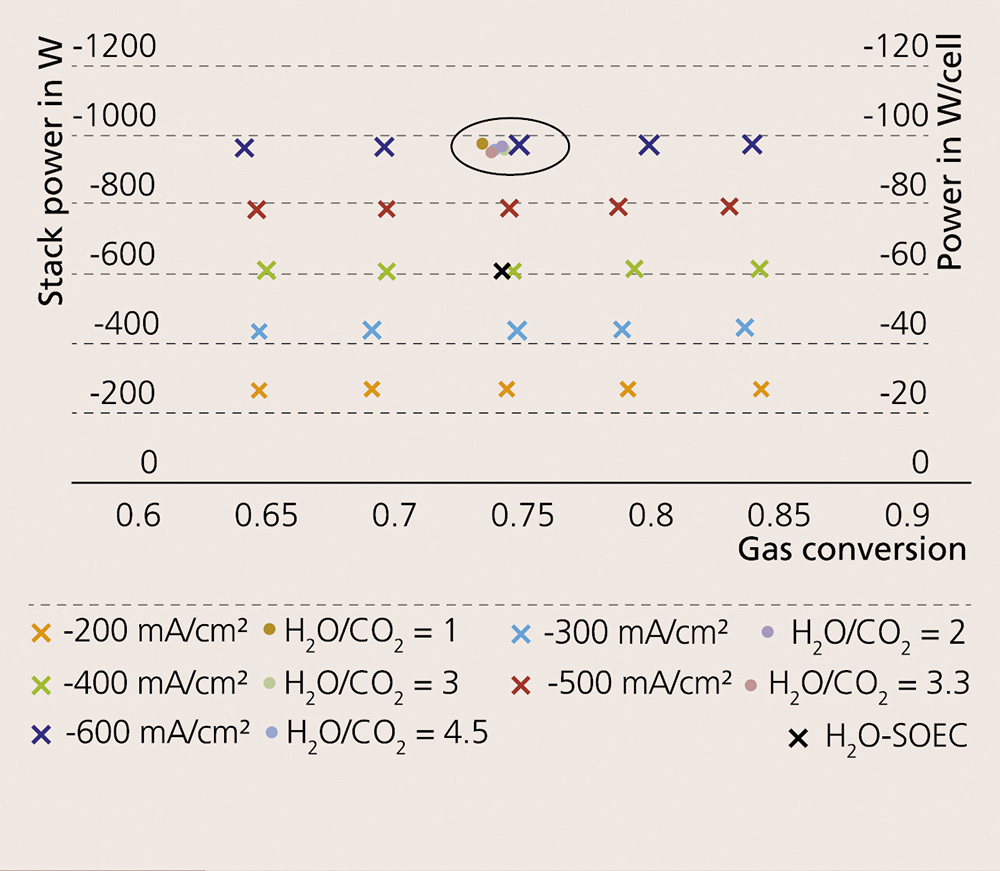
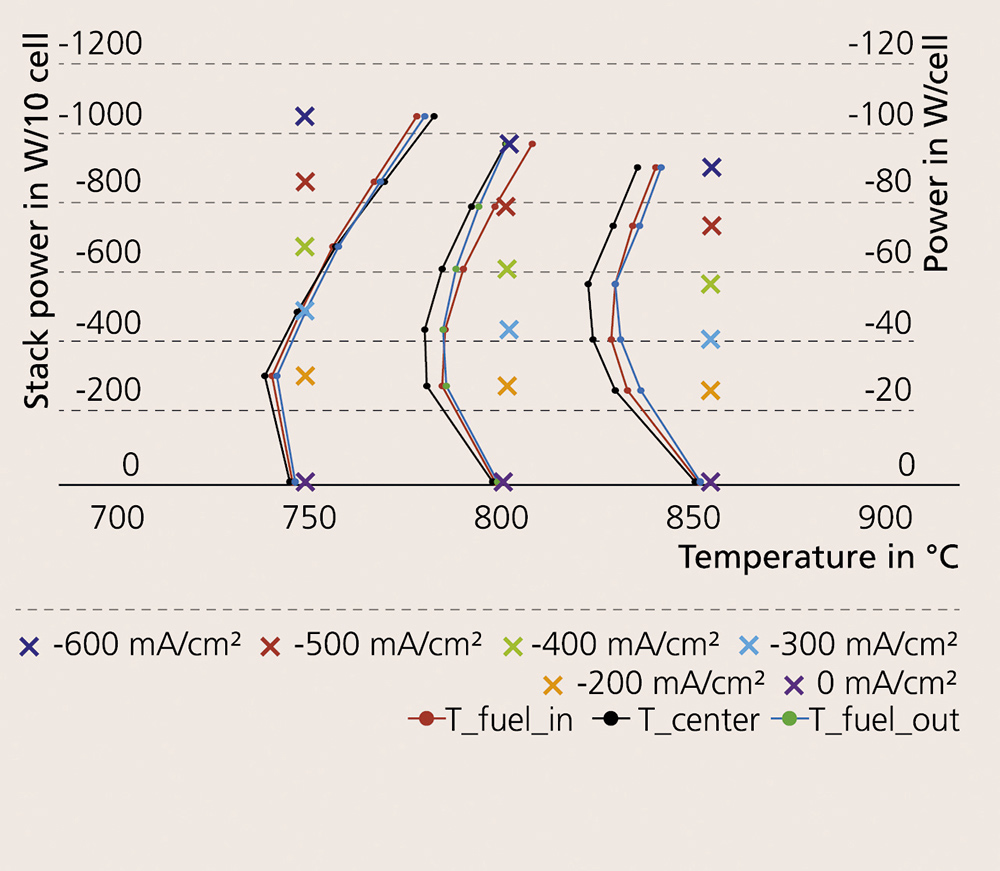
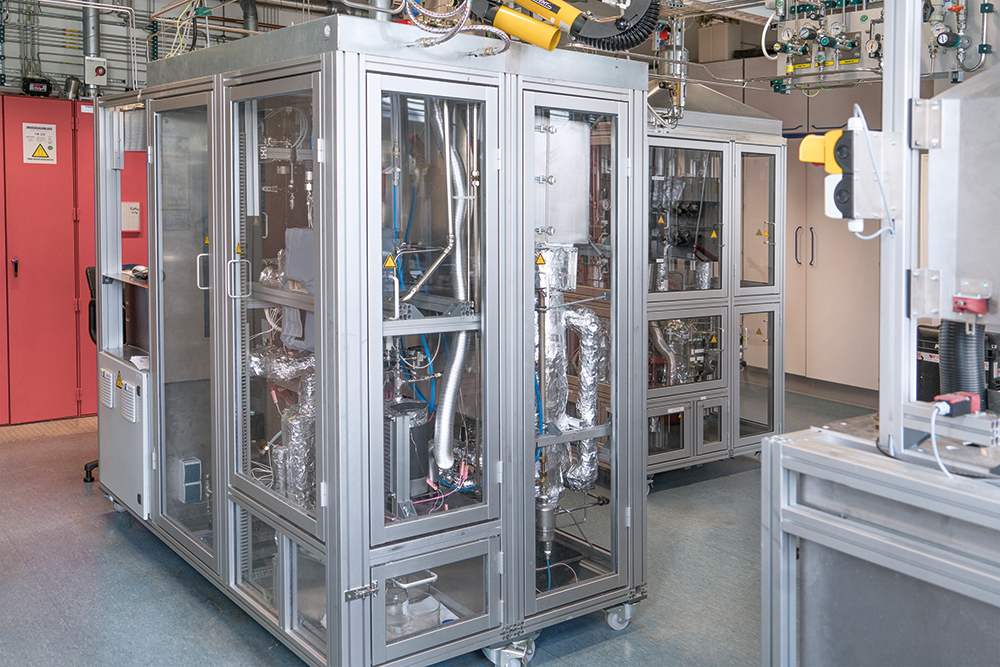
SOE technology
The possibility of substituting crude oil with synthetic hydrocarbons produced from CO2 and H2O is of increasing interest worldwide as a way to decrease dependence on fossil resources and to limit CO2 emissions. The coupling of solid-oxide electrolysis (SOE) technology and Fischer-Tropsch synthesis (FTS) is especially promising for the production of various types of hydrocarbons thanks to the possibility of integrating heat and utilizing by-products.
The reliable operation of solid-oxide cell (SOC) stacks in the co-electrolysis of H2O and CO2 is still considered a challenging technical task. Results on cathode-supported cells (CSC) reported in the literature show that operation in steam electrolysis and co-electrolysis modes below 800 °C brings with it considerable degradation rates. In contrast, electrolyte-supported cells (ESC) exhibit higher durability for electrolysis operation. Scientists at Fraunhofer IKTS have devised a CFY stack design that utilizes up to 40 high-power-density ESCs based on scandia-doped zirconia electrolytes. To prove their long-term stability, ten-cell stacks were tested in water electrolysis and co-electrolysis modes. A comparative analysis of the performance depending on operating temperature, feed composition and utilization was conducted for typical gas compositions for FTS (H2O:CO2 = 2) and methanation (H2O:CO2 = 3.3). The stack performance with a gas conversion rate up to 85 % at different temperatures in water and co-electrolysis modes at -600 mA/cm2 is visualized in Figure 1. A comparison between water and co-electrolysis modes at similar operating conditions yields similar power consumption figures: at 830 °C and -600 mA/cm2, 946 Wel are consumed in co-electrolysis mode and 943Wel in steam electrolysis mode. A higher Nernst potential of the H2O/H2/CO2/CO-containing gas system was identified as the primary reason for the difference.
High-temperature electrolysis is an endothermal process, consuming not only electric energy but also heat. The heat can be provided internally by the cell resistance (i.e. ohmic and electrochemical losses) for thermally self-sustaining operation. The voltage needed for such an operation is called thermoneutral voltage (UTN). In a system context, operating near UTN is beneficial for practical applications. For this reason, the temperature distribution inside the stack in co-electrolysis at a gas conversion rate of 75 % was investigated. Figure 2 shows a performance map and the temperature distribution within the CFY stack. It is possible to conclude, based on the temperature distribution, that at low current densities most of the steam is converted at the stack inlet, acting as a heat sink. At current densities close to UTN, the temperature profile inside the cell is homogenized.