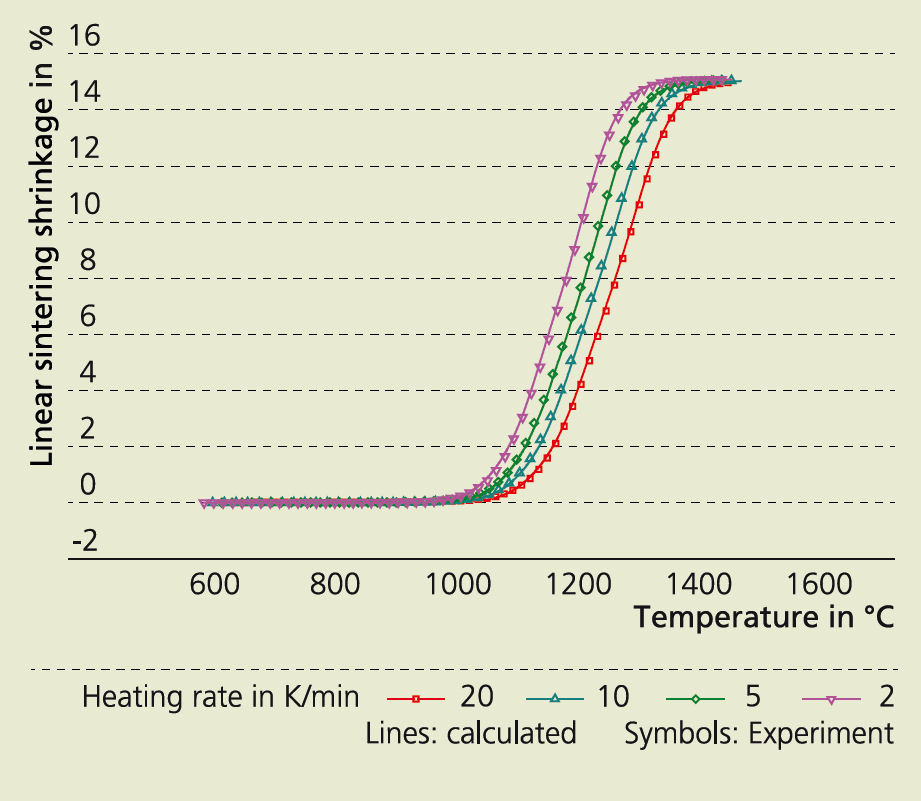

The processing conditions during sintering of large and/or complex parts have significant influence on the reliability of the product and the efficiency of the manufacturing process. Consequently, it is desirable to optimize sintering processes. However, due to the variety of influencing factors, this is associated with significant effort if the approach pursued is purely experimental. It is expected that this effort can be reduced by computer simulations. Hence, suitable methods for the model-based optimization of sintering processes have been developed at Fraunhofer IKTS.
Before simulations can be performed, an experimental characterization of the relevant material properties is generally necessary. With regard to this aspect, a methodology has been established which allows for the collection of the required data with minimal effort. Essential to the experimental procedure is the measurement of material-specific shrinkage curves (Figure 1).
The actual simulations do not only cover the modeling of the sintering process of a component but also account for the impact of the sintering furnace, which generally cannot be neglected. Figure 2 exemplarily shows the calculated temperature field in a gas pressure sintering furnace including the sintering body. The temperature field exhibits inhomogeneity, resulting in inhomogeneous shrinkage and mechanical stresses. This aspect is incorporated by a thermodynamically and kinematically consistent constitutive model, which has been implemented into a standard simulation package. The following figure exemplarily demonstrates the predicted influence of the processing conditions on the residual stresses remaining in the body after sintering.
As can bee seen from the Figure, a modification of the temperature- time history during cooling, while keeping all other parameters of the process constant, can cause a dramatic reduction of residual stresses in the component.
The methodology described above allows for an efficient and economic optimization of sintering processes in regard to the reduction of residual stresses, with processing times being minimized. At the same time, the estimation of the sintering warpage becomes much more accurate.