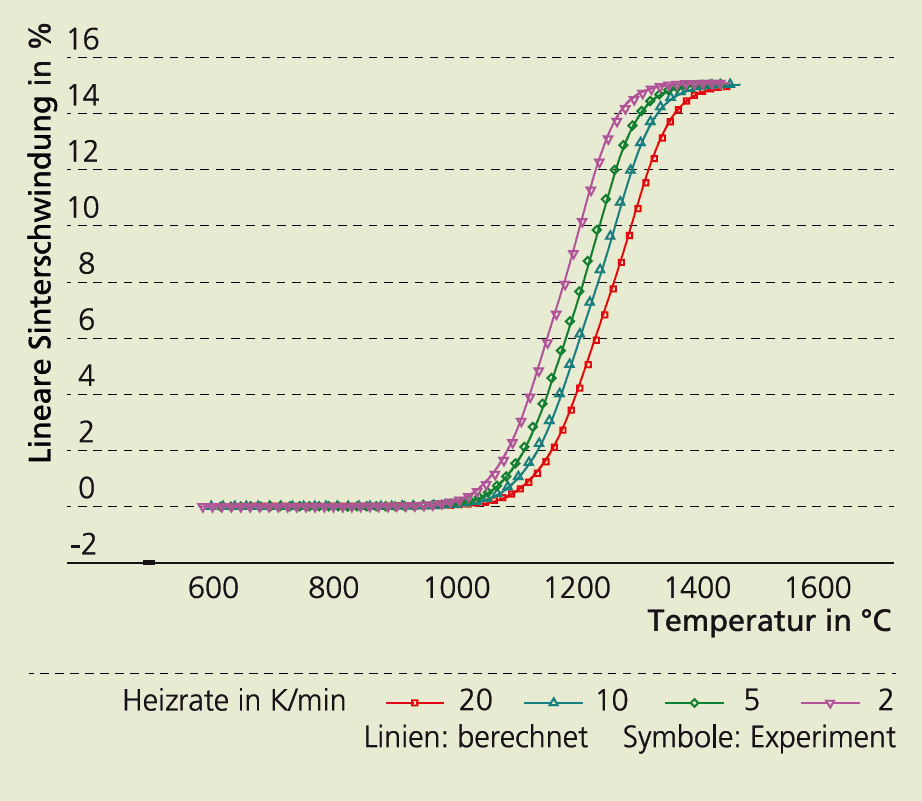
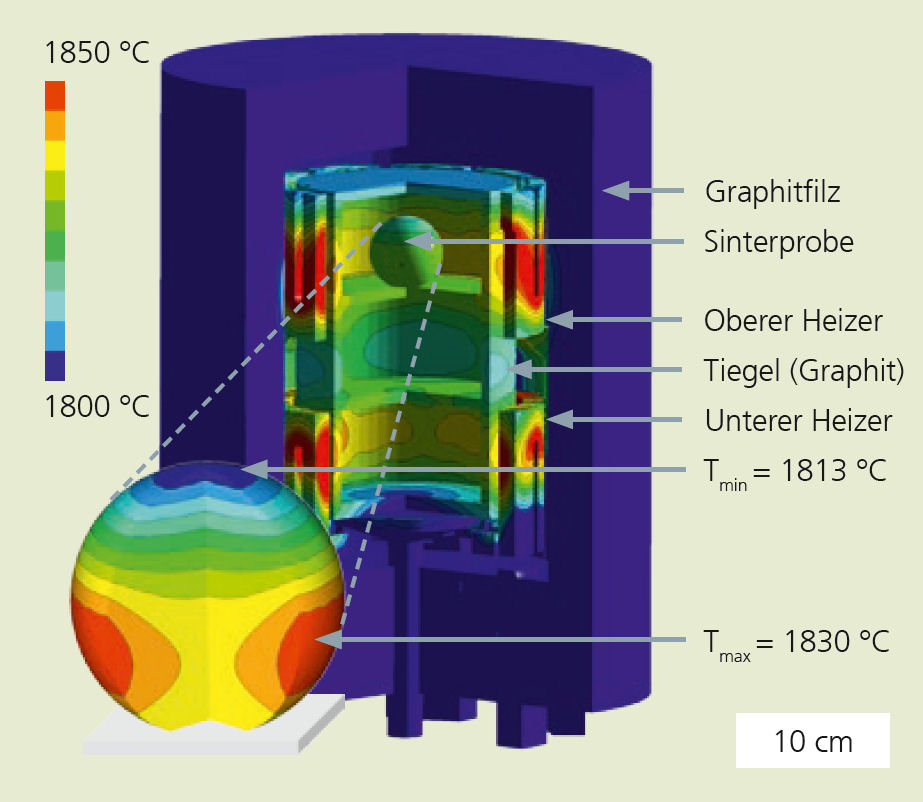
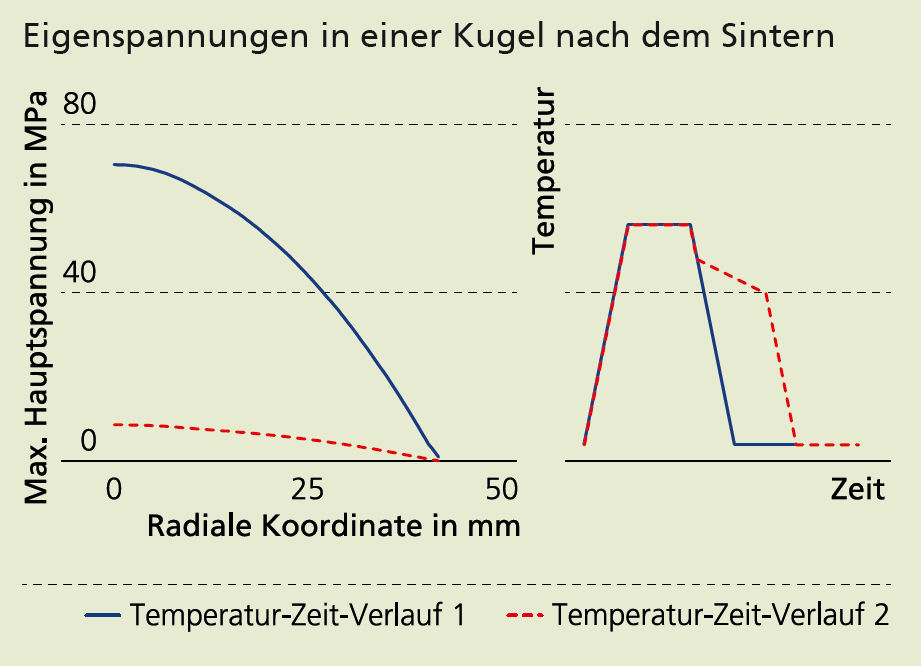
Die Prozessführung bei der Sinterung großer bzw. komplexer Bauteile beeinflusst entscheidend die Zuverlässigkeit der gefertigten Komponenten sowie die Herstellungseffizienz. Daher ist die Optimierung von Sinterprozessen anzustreben. Allerdings ist dies aufgrund der Vielzahl an Einflussfaktoren bei einem rein experimentellen Vorgehen mit hohem Aufwand verbunden. Durch Simulationen kann dieser Aufwand deutlich gesenkt werden. Deshalb wurden am Fraunhofer IKTS geeignete Methoden zur modellgestützten Optimierung von Sinterprozessen entwickelt.
Eine unverzichtbare Grundlage für die Durchführung von Modellrechnungen ist die Charakterisierung der relevanten Materialeigenschaften. Hierzu wurde eine experimentelle Methodik erarbeitet, mit der die benötigten Daten mit minimalem Aufwand erfasst werden können. Wesentlicher Bestandteil ist dabei die Bestimmung der materialspezifischen Schwindungskurven (Bild 1) sowie der thermischen und elastischen Materialeigenschaften.
In der eigentlichen Simulation wird mithilfe der Finite-Elemente-Methode nicht nur der Sinterprozess des Bauteils modelliert, sondern auch der nicht unbedeutende Einfluss des Sinterofens selbst berücksichtigt. Bild 2 zeigt exemplarisch die berechneten signifikant inhomogenen Temperaturfelder in einem Gasdrucksinterofen sowie in der Sinterprobe. Diese inhomogenen Temperaturfelder führen sowohl zu einem inhomogenen Schwindungsverhalten als auch zu mechanischen Spannungen. Diesem Sachverhalt wird mit einem am Fraunhofer IKTS entwickelten thermodynamisch und kinematisch konsistenten Werkstoffmodell Rechnung getragen, welches in ein Standardsimulationspaket implementiert wurde. In der nachfolgenden Abbildung wird beispielhaft der mit dem Modell vorhergesagte Einfluss der Prozessführung auf die nach dem Sintern im Bauteil vorliegenden Eigenspannungen aufgezeigt.
Anhand der Darstellung ist zu erkennen, dass eine Veränderung des Temperatur-Zeit-Verlaufs während des Abkühlens bei sonst gleicher Prozessführung zur drastischen Reduktion der Eigenspannungen in der Komponente führen kann.
Mit der beschriebenen Methodik lassen sich Sinterprozesse effizient und wirtschaftlich optimieren: Eigenspannungen im Bauteil können reduziert und Prozesszeiten gleichzeitig minimiert werden. Zudem wird eine realistische Abschätzung des Sinterverzugs möglich.