Author: Hilde-Josephine Post
Polymer concrete increases wear resistance of stirrers, benefiting not only biogas plants
A clever idea is paying off: coating stirrers in biogas plants with specially developed polymer concretes can double their service life. The researchers at Fraunhofer IKTS now intend to conquer other markets with their extremely wear-resistant coating technology. Industries that have to stir or pump aggressive substrates and suspensions could benefit enormously. The focus is on the chemical industry and the food and construction industries. But exciting solutions are also on the horizon for wind power rotor blades, which could reduce erosion damage.
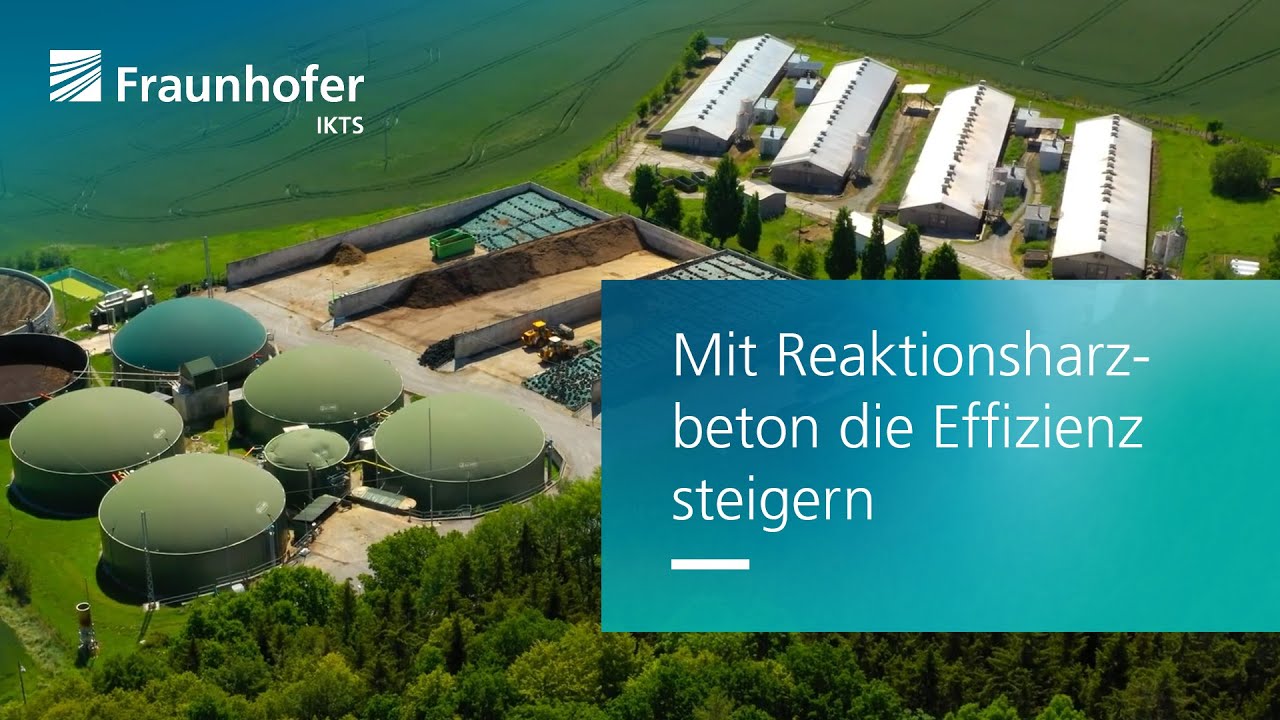
Privacy warning
With the click on the play button an external video from www.youtube.com is loaded and started. Your data is possible transferred and stored to third party. Do not start the video if you disagree. Find more about the youtube privacy statement under the following link: https://policies.google.com/privacyAbsolutely clear! Every biogas plant operator wants the fermentation processes in the digester to run optimally and economically. This means that the energy input should be as low as possible, but the gas yield as high as possible, so that electricity can then be generated from it. “The stirrer in the fermenter plays a crucial role here,” says Dr. Steffen Kunze, research associate at the Fraunhofer Institute for Ceramic Technologies and Systems IKTS, “because it consumes the most energy.” The stirrer mixes the biological mass in the fermenter to ensure that the bacteria which produce the biogas are well distributed. It also aims to prevent a floating layer, which would reduce biogas production.
High savings potential through optimized agitator
As part of the project “MaRüFerm”, funded by the German Ministry of Education and Research BMBF, the IKTS researchers around Kunze were able to demonstrate that enormous maintenance costs can be saved by optimizing the design of the stirrer propeller and extending its service life. The stirrer manufacturer Repowering Technik Ost GmbH and mineral casting specialist SICcast Mineralguß GmbH were also involved in the project. “We have projected,” says Steffen Kunze, “that for the several thousand biogas operators in Germany, the wear costs for the stirrer in the fermenter add up to 80 million euros per year. For each plant operator, therefore, the annual potential savings from an optimized agitator are in the five-digit range.”
Minimizing high chemical and tribological loads
Until now, the propeller of a stirrer represented the weakest link in the biogas process chain. The reasons: high tribological load due to plant fibers or sand in the biomass, for example. There is also a risk of corrosion due to chemical reactions caused by salts or acids that form in the fermentation substrate. “The biggest enemy here turns out to be sulfurous acid – especially in metal propellers,” the researcher explains. Frequent replacement of worn stirrers is very labor-intensive and time-consuming for biogas plant operators, making it costly. Kunze explains: “Apart from the fact that a new stirrer has to be installed, it is necessary to open and empty the hermetically sealed fermenter. The restarting process of such a fermenter takes several days, as it has to re-establish its internal climate to effectively produce biogas.”
Polymer concrete layer on propeller exceeds service life of plastic stirrers
How quickly a stirrer wears out depends, among other things, on its rotational speed. High-speed stirrers capable of up to 1000 rpm must be made of steel or cast iron. “Such a propeller can wear out within half a year to two years and thus no longer provide full performance,” the scientist knows. In contrast, slow-moving propellers with a diameter of 2 to 3 m, which usually rotate at 60 rpm and are made of common synthetic or fiber composite materials, achieved service lives of five years at most, according to Kunze.
On average, a major overhaul must take place every ten years. “Therefore, our project goal was to develop a stirrer that would function excellently, without significant wear, for an entire operating period until the major fermenter inspection,” the researcher explains. “And we have achieved this goal! We worked with SICcast to develop a polymer concrete that is specifically designed to withstand the tribological and corrosive attacks in fermentation substrates, especially against sulfurous acid.” This polymer conrete consists of two components, predominantly silicon carbide (SiC) as the ceramic material (80 %) and a special epoxy resin as the matrix. The epoxy resin serves as a binder and ensures that the coating is also impact-resistant.
Cost-efficient self-repair of a worn stirrer
Polymer concrete is mixed in a similar way to conventional concrete. It is cold-hardening and can be easily spread on the propeller, just as a bricklayer plasters a facade. The layer thicknesses can be varied between just a few 100 micrometers and several centimeters. After about two hours, it begins to cure. One day later, the mixer is ready for use. The trick is that plant operators can repair their propellers themselves. Steffen Kunze emphasizes: “In this way, a worn agitator can be re-armored relatively simply and costs are significantly lowered.”
Ten years of maintenance-free stirring thanks to polymer concrete
In laboratory tests, almost no signs of wear occurred with a polymer concrete coating compared to uncoated stirrers made of plastics such as laurinlactam-based polyamide, which is currently used as a state-of-the-art material. In field tests, the IKTS researchers were also unable to detect any significant structural changes in the stirrer after two years. Steffen Kunze concludes, “Now our solution has proven itself in practice for about four years. We assume that polymer concrete-coated stirrers can be used maintenance-free for ten years in fermenters of a biogas plant. This corresponds to a doubling of the service life compared with uncoated plastic stirrers. And in the case of metal stirrers, the new coating even increases the service life by a factor of 5 or 10."
Polymer concrete opens up new fields of application: highly interesting for chemical, construction and wind power industries
“Optimizing a stirrer proves to be a great lever for the plant operator, resulting in more flexibility with regard to different digestate substrates, more energy efficiency as well as ease of service and ultimately profitability,” the IKTS researcher concludes. These major advantages could also be interesting for applications in other industries, namely where aggressive substrates or suspensions need to be stirred or pumped. Kunze is thinking mainly of the chemical and construction industries: “The construction industry has huge problems with wear. For example, there are aggressive suspensions used for tunnel boring.” But the food industry, such as milk processors, could also benefit from polymer concrete. Because of the hygiene standards that must be met, aggressive acids and alkalis must be pumped through transport pipes to keep them germ-free. The problem with wind turbines is that the rotor blades are at risk of erosion, partly as a result of the weather and partly because of the high rotational speeds. Steffen Kunze explains: “The speed of the blade tips can reach more than 300 km/h. A raindrop then acts like a hydrojet cutter and erodes the surface of the rotor blades over time. We are currently in discussions about how polymer concrete can be usefully employed in this regard.” Due to its low density, the material could be particularly suitable here.
Polymer concrete is also recyclable
Recyclability is considered an important property these days. Here, IKTS has recently been holding a patent with ESK-SIC GmbH to effectively recycle silicon carbide components. Being eco-friendly is thus yet another reason to jump on the polymer concrete bandwagon. “That's why we want to increase awareness of this phenomenal composite material so that many more users can benefit from its advantages,” concludes Dr. Kunze.
5 compelling reasons to use polymer concrete!
|
Das könnte Sie interessieren:
- Carbide Ceramics
- Wear- and corrosion-resistant stirrer for fermenters in biogas plants
- Ceramics highly resistant against temperature, corrosion, and wear
- RECOSiC – recycling of silicon carbide
Stay informed: You are welcome to subscribe to our newsletter, read our other blog articles and follow us on LinkedIn, Instagram and YouTube.