Autorin: Hilde-Josephine Post
Reaktionsharzbeton erhöht Verschleißfestigkeit von Rührern, wovon nicht nur Biogasanlagen profitieren können
Eine clevere Idee macht sich bezahlt: Das Beschichten von Rührern in Biogasanlagen mit speziell entwickelten Reaktionsharzbetonen kann die Lebensdauer der Rührer verdoppeln. Nun beabsichtigen die Forschenden des Fraunhofer IKTS weitere Märkte mit ihrer extrem verschleißfesten Beschichtungstechnologie zu erobern. Enorm profitieren könnten hierbei Industriebranchen, die aggressive Substrate sowie Suspensionen rühren oder pumpen müssen. Im Blickfeld stehen die chemische Industrie sowie die Lebensmittel- und Bauindustrie. Doch auch für Windkraft-Rotorblätter bahnen sich spannende Lösungen an, die Erosionsschäden mindern könnten.
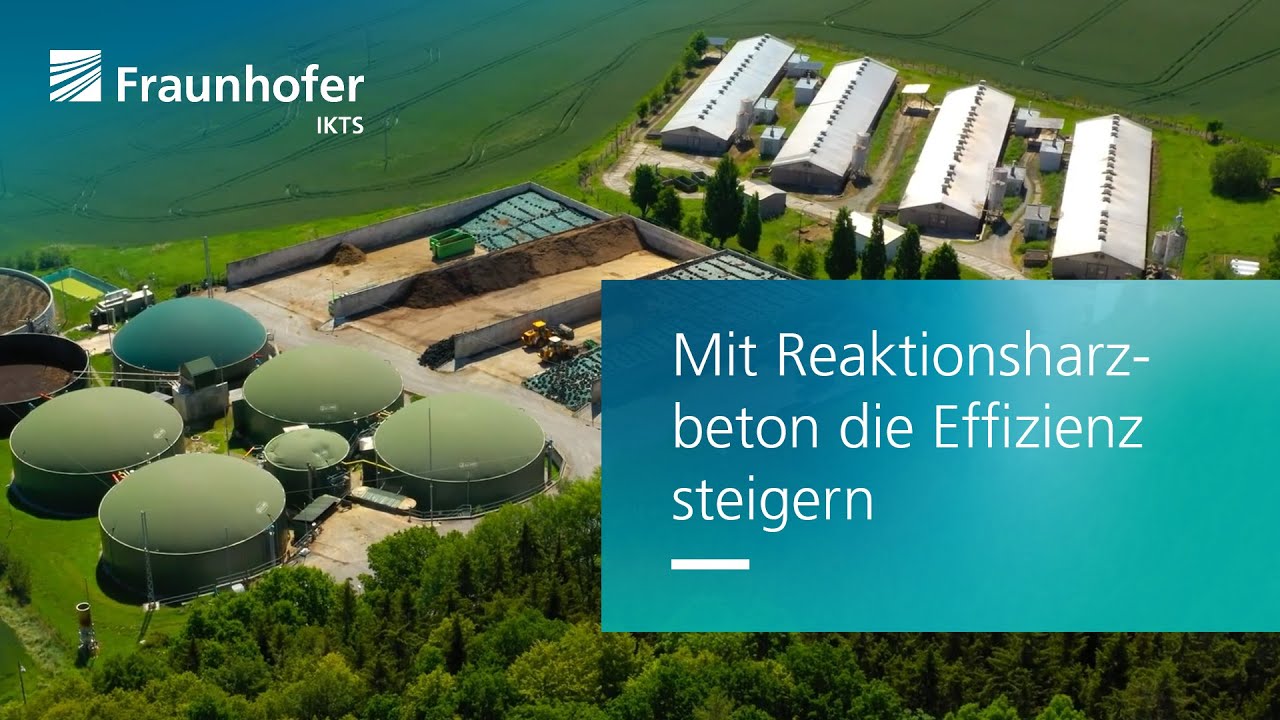
Datenschutz und Datenverarbeitung
Wir setzen zum Einbinden von Videos den Anbieter YouTube ein. Wie die meisten Websites verwendet YouTube Cookies, um Informationen über die Besucher ihrer Internetseite zu sammeln. Wenn Sie das Video starten, könnte dies Datenverarbeitungsvorgänge auslösen. Darauf haben wir keinen Einfluss. Weitere Informationen über Datenschutz bei YouTube finden Sie in deren Datenschutzerklärung unter: https://policies.google.com/privacyGanz klar! Jeder Biogasanlagenbetreiber wünscht sich, dass die Gärprozesse im Fermenter optimal und wirtschaftlich ablaufen. Das bedeutet, der Energieeintrag soll möglichst gering, die Gasausbeute möglichst hoch sein, um daraus dann Strom zu erzeugen. »Hierbei spielt das Rührwerk im Fermenter eine entscheidende Rolle«, sagt Dr. Steffen Kunze, wissenschaftlicher Mitarbeiter am Fraunhofer-Institut für Keramische Technologien und Systeme IKTS, »denn es verbraucht die meiste Energie.« Das Rührwerk durchmischt die biologische Masse im Gärbehälter, um die Bakterien, die das Biogas herstellen, gut zu verteilen. Zudem soll eine Schwimmschicht verhindert werden, welche die Biogasproduktion reduzieren würde.
Hohe Einsparmöglichkeiten durch optimiertes Rührwerk
Im Rahmen des BMBF-Projekts »MaRüFerm« konnten die IKTS-Forschenden um Kunze zeigen, dass sich über die Design-Optimierung des Rührpropellers sowie dessen Standzeitverlängerung enorme Wartungskosten einsparen lassen. Mit am Projekt beteiligt waren der Rührwerkshersteller Repowering Technik Ost GmbH sowie der Mineralgussspezialist SICcast Mineralguß GmbH. »Wir haben hochgerechnet«, so Steffen Kunze, »dass sich bei einigen Tausend Biogasbetreibern, die es in Deutschland gibt, die Verschleißkosten für das Rührwerk im Fermenter auf 80 Millionen Euro pro Jahr aufsummieren. Je Anlagenbetreiber bewegen sich also die jährlichen Einsparmöglichkeiten durch ein optimiertes Rührwerk bis in den fünfstelligen Bereich.«
Hohe chemische und tribologische Beanspruchung minimieren
Bisher stellte der Propeller eines Rührwerks das schwächste Glied in der Biogas-Prozesskette dar. Die Gründe: Hohe tribologische Beanspruchung etwa durch Pflanzenfasern oder Sand in der Biomasse. Zudem besteht Korrosionsgefahr aufgrund chemischer Reaktionen durch Salze oder Säuren, die sich im Gärsubstrat bilden. »Als größter Feind erweist sich hierbei die schweflige Säure – besonders bei Metallpropellern«, erklärt der Forscher. Ein häufiger Austausch von verschlissenen Rührern ist für Biogasanlagenbetreiber sehr arbeits- und zeitaufwendig und damit kostspielig. Steffen Kunze nennt die Gründe: »Abgesehen davon, dass ein neuer Rührer eingebaut werden muss, ist es notwendig, den hermetisch abgeriegelten Fermenter zu öffnen und zu entleeren. Der Wiederanlaufprozess eines solchen Fermenters nimmt einige Tage in Anspruch, da er sein inneres Klima wieder herstellen muss, um effektiv Biogas zu produzieren.«
Reaktionsharzschicht auf Propeller übertrifft Standzeit von Kunststoffrührern
Wie schnell ein Rührer verschleißt, hängt unter anderem von seiner Rotationsgeschwindigkeit ab. Schnellrührer, die bis zu 1000 U/min schaffen, müssen aus Stahl oder Gusseisen sein. »Ein solcher Propeller kann innerhalb von einem halben bis zwei Jahren verschlissen sein und somit keine volle Leistung mehr bringen«, weiß der Wissenschaftler. Hingegen erreichten Langsamrührer mit 2 bis 3 m Durchmesser, die in der Regel mit 60 U/min rotieren und aus gängigen Kunst- oder Faserverbundwerkstoffen bestehen, laut Kunze Standzeiten von maximal fünf Jahren.
Durchschnittlich muss alle zehn Jahre eine große Revision stattfinden. »Deshalb peilten wir als Projektziel an, einen Rührer zu entwickeln, der eine ganze Betriebsperiode bis zur großen Gärbehälterinspektion exzellent, ohne signifikanten Verschleiß funktioniert«, erklärt der Forscher. »Und dieses Ziel haben wir erreicht! Wir haben zusammen mit SICcast einen Reaktionsharzbeton (RHB) entwickelt, der speziell designt ist, um den tribologischen und korrosiven Angriffen in Gärsubstraten standzuhalten, gerade auch gegenüber schwefeliger Säure.« RHB besteht aus zwei Komponenten, überwiegend aus Siliciumcarbid (SiC) als keramisches Material (80 %) und einem speziellen Epoxidharz als Matrix. Das Epoxidharz dient als Binder und sorgt dafür, dass die Beschichtung auch schlagunempfindlich ist.
Verschlissener Rührer kostengünstig selbst instand setzen
Reaktionsharzbeton wird ähnlich wie klassischer Beton angemischt. Er ist kalthärtend und lässt sich ganz einfach auf den Propeller aufspachteln, so wie ein Maurer eine Fassade verputzt. Die Schichtdicken sind variierbar zwischen nur wenigen 100 Mikrometern und mehreren Zentimetern. Nach etwa zwei Stunden beginnt RHB auszuhärten. Einen Tag später ist der Rührer einsatzfähig. Der Clou: So kann ein Anlagenbetreiber seine Propeller selbst wieder instand setzen. Steffen Kunze betont: »So lässt sich ein verschlissener Rührer relativ simpel neu armieren und spart signifikant Kosten.«
Zehn Jahre wartungsfreies Rühren dank Reaktionsharzbeton
In Laborversuchen traten im Vergleich zu den unbeschichteten Rührern aus Kunststoffen wie auf Laurinlactam basiertem Polyamid, das als State-of-the-art-Material derzeit Anwendung findet, bei einer RHB-Beschichtung fast keine Verschleißerscheinungen auf. Auch im Feldversuch konnten die IKTS-Forscher nach zwei Jahren keine signifikanten Strukturveränderungen am Rührwerk feststellen. Steffen Kunze schlussfolgert: »Nun bewährt sich unsere Lösung seit rund vier Jahren in der Praxis. Wir gehen davon aus, dass Reaktionsharzbeton-beschichtete Rührer zehn Jahre wartungsfrei in Fermentern einer Biogasanlage eingesetzt werden können. Das entspricht einer Verdopplung der Standzeit gegenüber den unbeschichteten Kunststoffrührern. Und bei Metallrührern erhöht sich durch die RHB-Beschichtung die Standzeit sogar um den Faktor 5 oder 10.«
Reaktionsharzbeton eröffnet neue Anwendungsfelder: hochinteressant für Chemie-, Bau- und Windkraftindustrie
»Ein Rührwerk zu optimieren, erweist sich als großer Hebel für den Anlagenbetreiber, was mehr Flexibilität in Bezug auf unterschiedliche Gärrest-Substrate, mehr Energieeffizienz sowie Servicefreundlichkeit und letztlich Wirtschaftlichkeit zufolge hat«, schlussfolgert der IKTS-Forscher. Diese großen Vorteile könnten auch für Anwendungen in anderen Branchen interessant sein, nämlich dort, wo aggressive Substrate oder Suspensionen zu rühren oder zu pumpen sind. Der Wissenschaftler Kunze denkt da hauptsächlich an die Chemie- und Bauindustrie: »Die Bauindustrie hat riesige Probleme mit Verschleiß. Es gibt zum Beispiel aggressive Suspensionen, die für das Tunnelbohren verwendet werden.« Aber auch in der Lebensmittelindustrie, so könnten etwa Milch-Verarbeiter von Reaktionsharzbeton profitieren. Aufgrund der einzuhaltenden Hygienestandards müssen aggressive Säuren und Laugen durch Transportrohre gepumpt werden, um diese keimfrei zu halten. Bei Windkraftanlagen besteht das Problem, dass die Rotorblätter erosionsgefährdet sind, zum einen infolge der Witterung und zum anderen wegen der hohen Rotationsgeschwindigkeiten. Steffen Kunze erläutert: »Die Geschwindigkeit der Blattspitzen erreicht über 300 km/h. Ein Regentropfen wirkt dann wie ein Wasserstrahlschneider und erodiert mit der Zeit die Oberfläche der Rotorblätter. Wir befinden uns zurzeit im Gespräch, wie sich Reaktionsharzbeton diesbezüglich sinnvoll einsetzen lässt.« Aufgrund seiner geringen Dichte könnte sich das RHB-Material hier ganz besonders eignen.
Reaktionsharzbeton ist auch recyclebar
Auch Recycelfähigkeit gilt heutzutage als wichtige Eigenschaft. Hier hält das Fraunhofer IKTS mit der ESK-SIC GmbH seit kurzer Zeit ein Patent, um Siliciumcarbid-Bauteile effektiv zu recyceln. Umweltfreundlichkeit ist also noch ein weiterer Grund, auf den Reaktionsharzbeton-Zug aufzuspringen. »Deshalb wollen wir die Bekanntheit dieses phänomenalen Verbundmaterials steigern, damit noch viele Anwender von dessen Vorteilen profitieren können«, so Dr. Kunze abschließend.
5 bestechende Gründe, Reaktionsharzbeton einzusetzen!
|
Das könnte Sie interessieren:
- Carbidkeramik
- Verschleiß- und korrosionsbeständige Rührwerke für Biogasanlagen
- Hochresistente Keramik gegen Temperatur, Korrosion und Verschleiß
- RECOSiC – Recycling von Siliciumcarbid
Bleiben Sie informiert: Melden Sie sich gern für unseren Newsletter an, lesen Sie in weitere Blogbeiträge rein oder folgen Sie uns auf LinkedIn, Instagram und YouTube. Wir freuen uns, mit Ihnen ins Gespräch zu kommen.