Author: Maria Kaminski
The future today – New technology approaches for the manufacture of ultrasonic transducers
In a matter of life and death, every minute counts. If patients are treated on-site, for example at the scene of an accident, their chances of survival are increased significantly. To ensure that emergency physicians can make the right diagnosis quickly, mobile ultrasound equipment is used, among other things. This means that necessary treatment steps can be initiated at the scene of the accident. Ultrasound equipment is not only used in medical diagnostics, however, but also in imaging for non-destructive materials testing. They have distinct advantages over X-ray analysis due to their non-ionizing nature and the fact that additional physical as well as structural information of the examined media can be derived from the images and measurements obtained. However, it is precisely this miniaturization trend in transducers that presents Fraunhofer IKTS construction engineers with huge challenges – especially in the development of innovative manufacturing processes.
The conventional manufacturing process for ultrasonic transducers consists of several stages. The main component is a piezoceramic plate, which is ground down to the target thickness, electroded on both sides and polarized. The plate is then bonded to a damping body, sawed and fitted with matching layers. Not only is this process cumbersome, but it results in adhesive layers that interfere with acoustic sound. This disadvantage can be eliminated using printing techniques. Various printing processes are being developed at IKTS for the manufacture of application-specific ultrasonic transducers, which in the future should replace the complex production of ultrasonic transducers using assembly techniques.
From screen printing to nozzle-based printing processes
The screen-printing process allows the printing of structures with a resolution of up to 100 µm and a thickness of 30 to 150 µm – so-called thick films – on planar and tubular substrates. The print image, and thus the structure of the ultrasonic transducers, is specified by the screen opening through which the paste is pressed during the printing process: this happens not only very quickly, but also with high reproducibility. Piezoceramic screen-printing pastes, as developed at IKTS, are the basis for this. This process facilitates the serial production of components in large quantities but is limited in the component geometry that can be realized.
Complex component structures with multiple curvatures, as are advantageous for self-focusing ultrasonic transducers, for example, require the use of nozzle-based printing processes. For this purpose, aerosol-jet and ink-jet printing are available at Fraunhofer IKTS. Special inks or pastes are developed for these processes, which allow nozzle-based application. This technological approach allows the realization of much finer structure resolutions of up to 40 µm at a thickness of 5 to 30 µm.
Realization of ultrasonic transducers with printing processes
Several printing and bonding steps are necessary for the construction of ultrasonic transducers. First, the basic electrode is applied in line or ring form and burned in. The lateral dimension of the structures determines the focus of the emitted ultrasonic lobe and thus the possible image resolution of the transducer. The piezoceramic layer is then printed. Depending on the desired layer thickness, several pressure cycles are run. Insulation layers for overcontacting as well as cover electrode and matching layers are then printed.
Future implementation in a single process chain
The aim is to ensure the undisturbed transmission and reception of ultrasonic waves. The porosity of the substrate plays a decisive role here. The targeted adjustment of the porosity of the substrates should enable complete attenuation of the backscattered ultrasonic echo and thus undisturbed transmission and reception of ultrasonic waves in the frequency range between 5 and 40 MHz. Demonstrators based on screen-printing technology are currently being manufactured at Fraunhofer IKTS. For example, line transducers for medical technology but also ring arrays for non-destructive materials testing are printed on different substrates. In the future, attenuators, ultrasonic transducers as well as assembly and interconnection technology will be realized in one process chain. Fraunhofer IKTS is already in close contact with various industries that would like to use the transducers developed, printed and manufactured at IKTS for non-destructive testing of silicon wafers in the semiconductor industry as well as for medical technology.
Cost-effective production in large quantities
Compared with previous assembly methods, the use of print-based processes allows ultrasonic transducers to be manufactured in large quantities at low cost and in a reduced time. Their compact design is in line with the trend toward miniaturization, price reduction and electronic densification. This predestines them for use in portable and ultra-portable devices for laptop or smartphone-based applications.
The printed ultrasonic transducers are also free of unwanted intermediate layers and offer the advantage of integrated assembly and connection technology. While conventional ultrasonic transducers are further contacted by wiring and soldering or bonding contacts, the conductive paths can be applied directly using printing technology. This avoids the application of bulky solder or bond pads, which have a negative impact on the vibration behavior of the transducer.
Applications range from medical technology to non-destructive testing
Conventional ultrasound imaging systems are typically operated at frequencies between 1 and 15 MHz. The aim of the research at IKTS is the development of high-frequency ultrasonic transducers with frequencies above 15 MHz in order to achieve an improvement of the image resolution. With increasing ultrasound frequency not only the resolution increases, but also the acoustic penetration depth into the tissue decreases. Therefore, high-frequency ultrasound transducers are particularly suitable for structures close to the surface or accessible by catheters, e.g., in the context of dermatological, ophthalmological or intravascular examinations. This property makes them interesting not only for medical technology, but also for preclinical laboratory animal examinations and the non-destructive testing of fiber-reinforced plastics, cohesive joints and electronic components in the semiconductor industry.
Further information: Piezoceramic Thick Films
The project was funded by the German Federation of Industrial Research Associations Otto von Guericke e.V.
Stay informed: You are welcome to subscribe to our newsletter, read our other blog articles and follow us on LinkedIn, Instagram and YouTube.
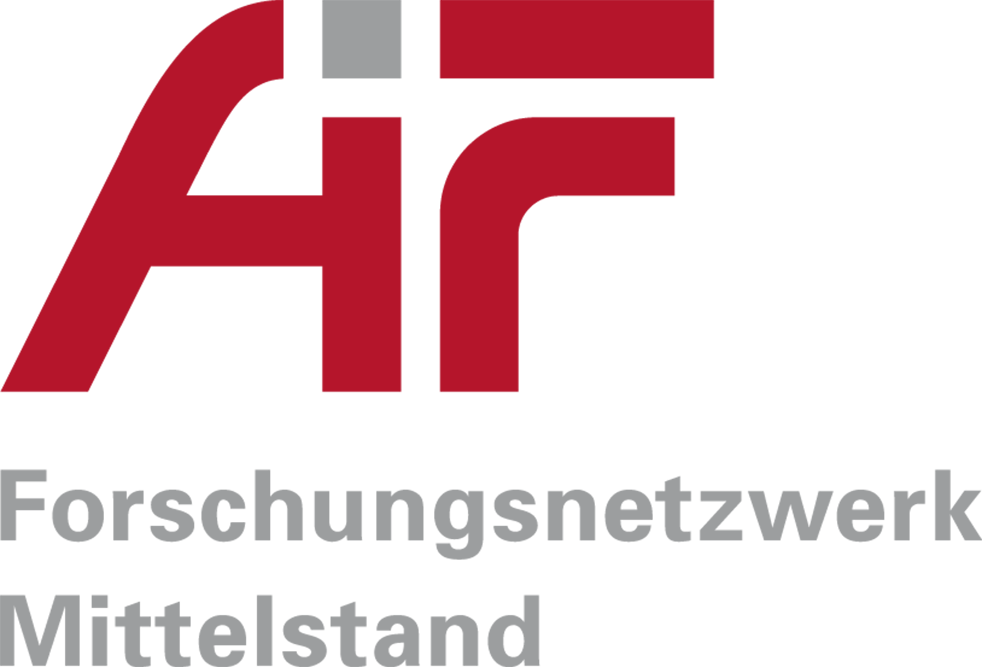