Author: Anika Peucker | Translation: Anna Knollmann, Stephanie Anderseck
Barkhausen noise - looking into the skeleton of aging steel
Imagine a steel bridge. You walk across it almost every day. Today you stop in the middle. One thought plagues you: How can I always be sure that the bridge will hold when I cross it? Are such steel structures maintained? Can engineers "look inside" steel and detect its aging and wear at an early stage? And what about other steel components and buildings? Is their quality checked?
Well, you probably don't have to feel unsafe on Germany's bridges and steel structures. Due to a lack of non-destructive testing facilities, many components and structures are taken out of service long before they can no longer perform their task. This is a justified precautionary measure to date, but unfortunately it is neither cheap nor environmentally friendly.
This is where the Barkhausen noise - a nondestructive testing method researched by the Fraunhofer IKTS - comes into play. The Barkhausen noise can be used to measure residual stress in steel structures. The testers use these values to determine the remaining service life. They use them to make predictions and determine maintenance intervals both intelligently and in a way that conserves resources. An estimable factor in terms of sustainability. Because according to the Federal Ministry of Transport and Digital Infrastructure (BMVI; as of 09.2018), there are about 39,500 bridges in Germany alone in the network of federal highways. They span a total length that is roughly comparable to the distance from Flensburg to Naples. In relation to the bridge area and according to the currently valid guidelines, almost 20 percent of the bridges are in a structural condition in need of repair (BMVI, status 9.2018). And that only applies to bridges on federal highways, not including other buildings or structures made of steel.
How does Barkhausen Noise record residual stresses to determine component fatigue?
About 80 percent of all damage in steel structures can be attributed to fatigue. Component fatigue involves various processes that take place in the material while it is subjected to thermal or mechanical stress. Fatigue impairs the function of the component during its loading until it fails completely. It is therefore important to diagnose fatigue damage at an early stage. Accidents or extensive repairs can be prevented in this way.
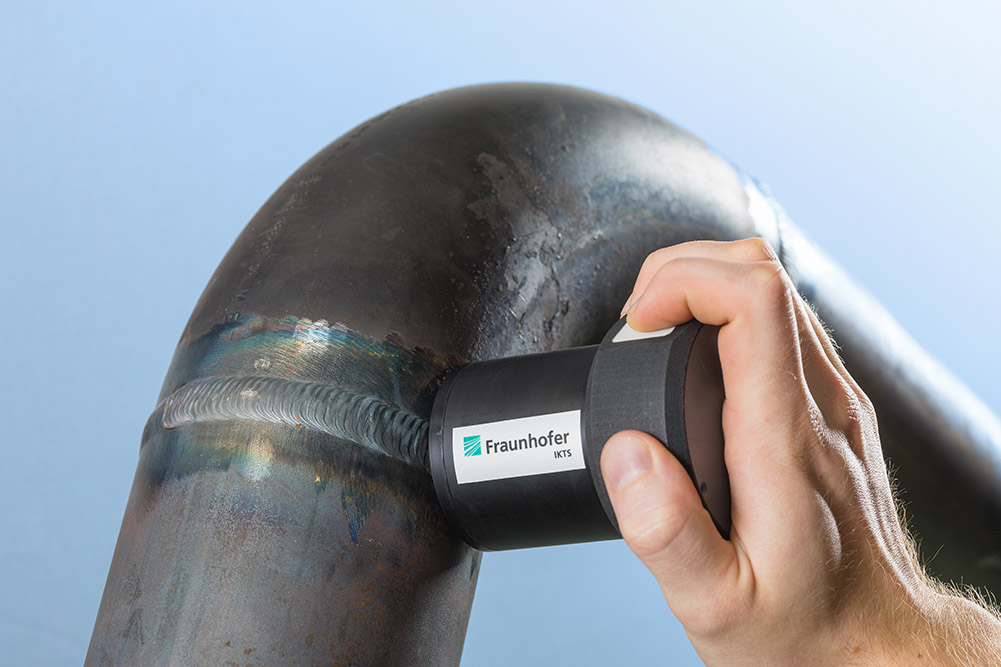
Mechanical stresses are a dominant factor in the fatigue of components and the associated functional losses of the component. Such residual stresses are caused by external loads or internal stresses. We cannot see them with the naked eye. They can only be detected by examining the microstructure of the component or structure, which can be very costly depending on the method used. The Barkhausen noise detects the changes in the microstructure and evaluates the stress state without lengthy preparations at the measuring point or cutting out material samples.
Let's return to the steel bridge: To measure the residual stress on such complex structures as bridges, we need a digital and compact testing system. It must be light, portable and easy to operate. In addition, the probes that record the measurement signal should be interchangeable so that the engineer can measure in narrow corners and on surfaces of different geometries and sizes. Such a mobile device based on the Barkhausen noise method did not exist until now, although Barkhausen noise effects have been known for more than 100 years. For this reason, the designers recently planned the components to be both life-safe and material-intensive. However, this design method requires more space, resources and costs correspondingly more.
Versatile: the compact, digital Barkhausen noise measurement system
Against this background and on the basis of many years of research experience on Barkhausen noise, algorithms and sensors, the scientists of Fraunhofer IKTS developed a sophisticated measurement technology together with SURAGUS GmbH and dresden elektronik (DDE). The pilot measurement system closes the gaps and limitations left by previous Barkhausen Noise devices. Besides a more user-friendly concept for hardware, software and the probes, the researchers implemented new calibration algorithms. In the past, calibration was a central hurdle in daily operation. The complex calibration effort was one of the main reasons why Barkhausen Noise, as a non-destructive testing method, hardly penetrated the field and occupied only a niche. The calibration-free pilot measuring system - made possible by auto-calibration - can now ensure that the method can be safely handled under construction site conditions. The former considerable inaccuracies and high operating costs that discouraged many
potential users are a thing of the past. As a result, the measurement results provide operators and authorities with a well-founded basis for decisionmaking, which they can use to plan the remaining service life or rehabilitation. The next steps can be initiated in a controlled manner. Maintenance measures are neither started prematurely nor too late.
The Barkhausen-Noise-Analyzer - a decision for economy
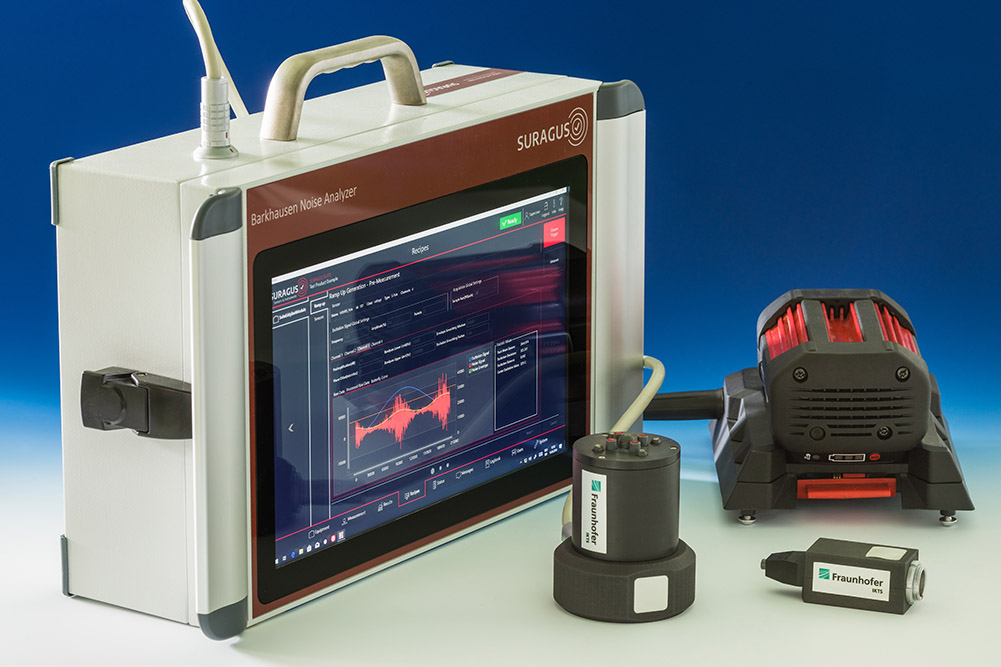
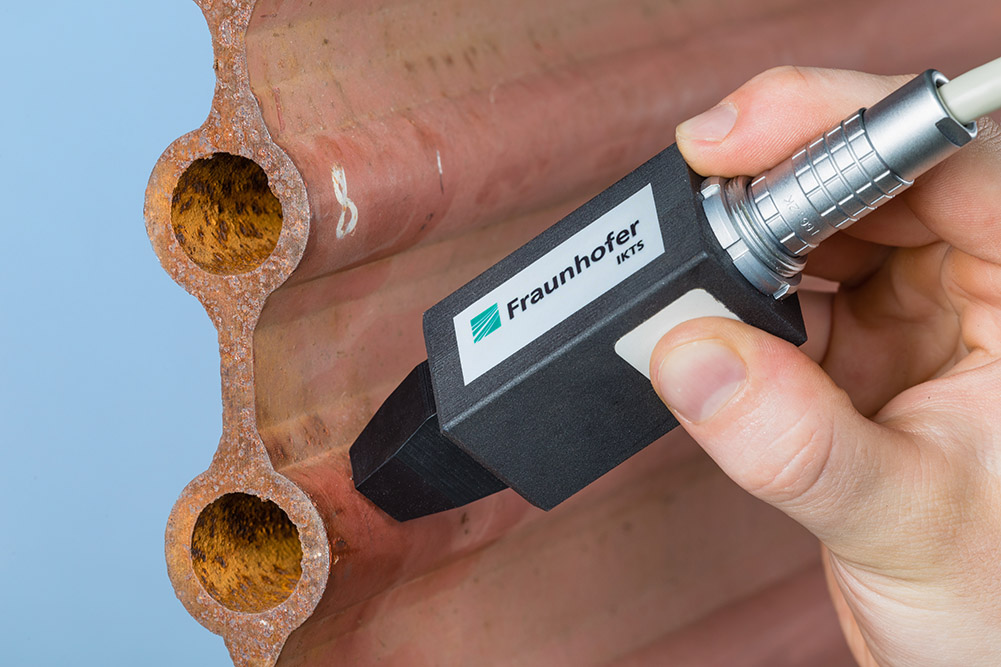
Companies from the energy and mobility sector as well as companies from the environmental, raw materials, micro- and nanoelectronics or advanced production technologies and new materials sectors can benefit from reactive maintenance of industrial buildings and facilities. They optimize their costs for quality assurance of manufacturing processes, reduce their scrap rates and maintain more viable structures more economically. As a user of structures such as bridges or as a consumer of products
manufactured on steel and steel alloy plants, I feel more hope and confidence when I know that such technologies exist and will find their way into the market.
Hope, because there is a way to use resources in line with demand. And confidence that quality and safety will be available to the extent possible. With this thought in mind, I drive across German bridges in a relaxed manner. How is that with you?
Stay informed! You are welcome to subscribe to our newsletter, read our other blog articles and follow us on Facebook, Instagram, LinkedIn, YouTube and Twitter.