Working together for the industrialization of bipolar batteries with Lithium-ion technology
Better batteries for a greater range of electric vehicles – this is the goal of the “EMBATT-goes-FAB” project sponsored by the Federal Ministry for Economic Affairs and Energy. For that reason, the four project partners thyssenkrupp System Engineering GmbH, IAV GmbH, Daimler AG and the Fraunhofer Institute for Ceramic Technologies and Systems IKTS are developing bipolar batteries and processes for their fabrication. Thanks to their unique stacked layout, a higher storage capacity and, ultimately, a greater range of the vehicle are achieved using the same surface area. The innovative battery technology will now be taken to the next level of maturity and thus one step closer to industrialization.
More energy. Greater range. Greater comfort. This is the logical chain. But it also describes the most important challenges of electromobility, both in terms of technical and economic viability. The key to solving these issues is the use of an optimized vehicle battery.
Innovative layout of bipolar batteries makes greater range possible
In their joint project “EMBATT-goes-FAB”, thyssenkrupp System Engineering GmbH, IAV GmbH, Daimler AG, and Fraunhofer IKTS want to make a contribution to improving future vehicle batteries. By researching scaled manufacturing technologies and integration solutions, the project aims to advance the industrialization of so-called bipolar batteries. These are Li-ion batteries, which, like fuel cells, consist of stacked electrodes connected in series. In contrast to conventional Li-ion batteries, these electrodes are, as the name indicates, bipolar. This means that the active materials for the battery cathode and, overleaf, the active materials for the anode are applied to a common electrode carrier. The individual Li-ion cells are then no longer packed separately in aluminum housings. Only the finished stack of electrodes is given a fixed housing. This eliminates housing components and connecting elements, which saves costs and space in the vehicle. Instead, the freed-up space can be filled with more active material. As a result, the battery can store more energy and the vehicle can drive further. This is the charm of Li-ion bipolar batteries, which have so far only been investigated on a laboratory and pilot scale.
Pooling competencies: Joint drive for industrialization
The motivation for the four project partners to take this technology to the next level of maturity is obvious, as is the incentive for the Federal Ministry of Economic Affairs and Energy, which will provide financial support for the “EMBATT-goes-FAB” project over a period of two years.
But it is not only motivation and framework that matter. The partners involved in the project must also be closely interlinked in order to master the new challenges. These range from the production of improved bipolar electrodes based on lithium-nickel-manganese-cobalt oxides and graphite as storage materials (Fraunhofer IKTS), to the scaling of assembly technology up to a size of 1000 x 30 cm² (thyssenkrupp System Engineering), the incorporation of an electric battery monitoring system (IAV GmbH), and safety simulations to address specific vehicle requirements (Daimler AG). The competencies complement each other perfectly. These are good prerequisites for taking a big step towards the ambitious goal of providing tomorrow's car drivers with more electric range and thus greater comfort.
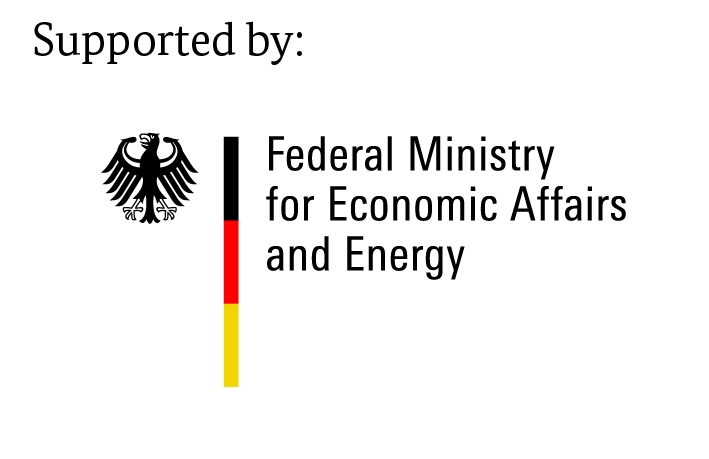