Polymer-ceramic housing for high-temperature microsystems
Project
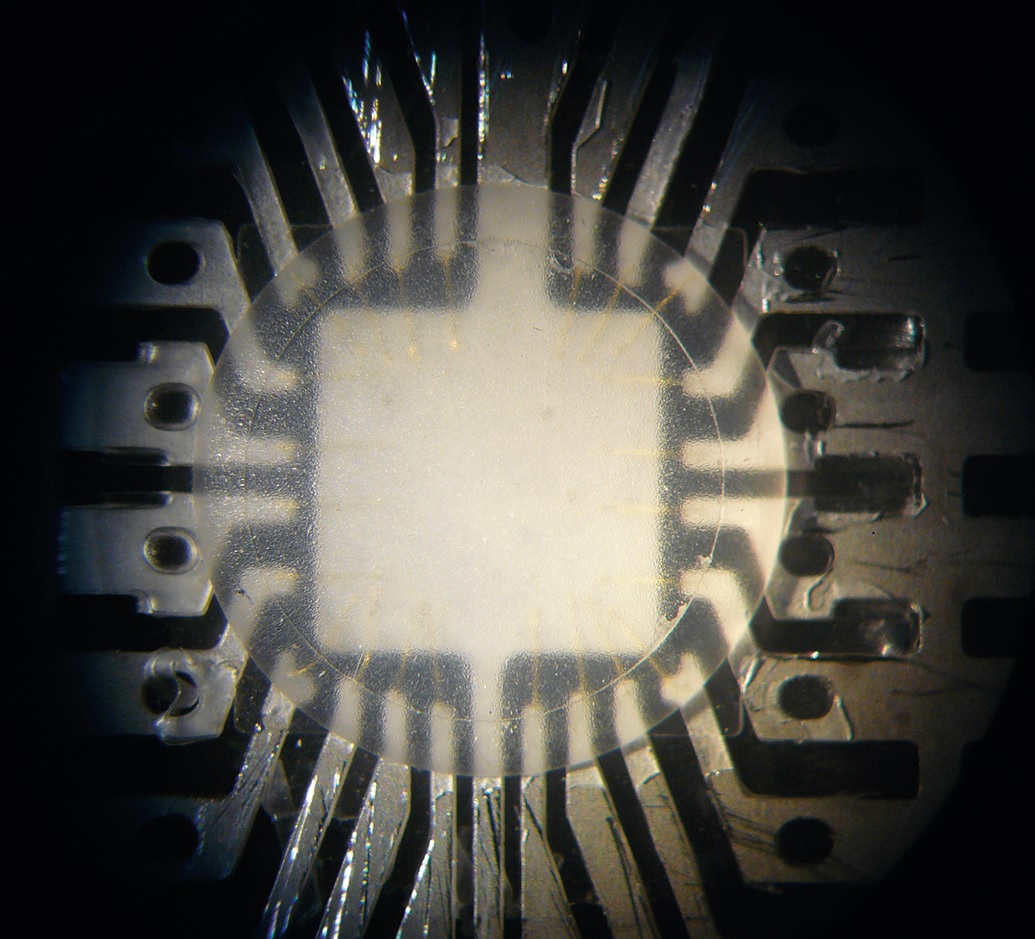
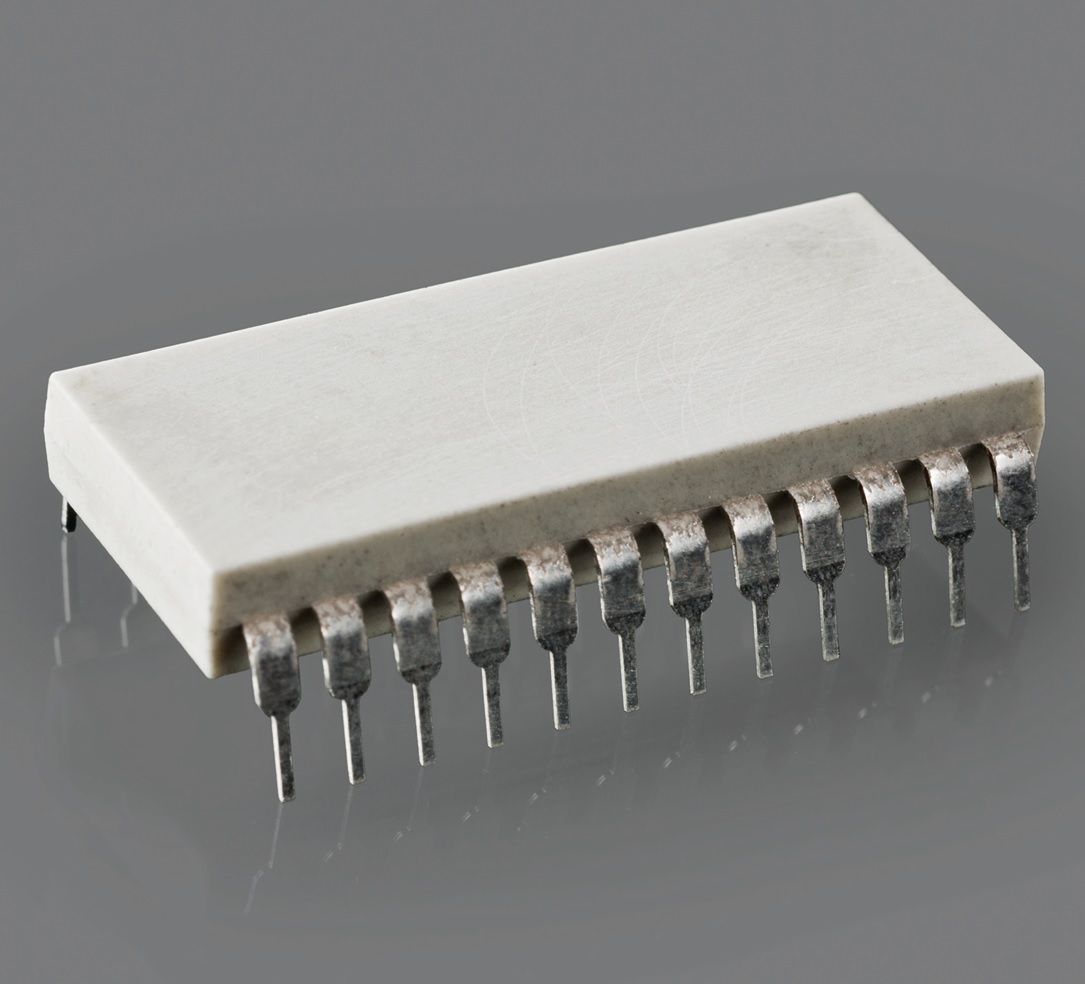
Modern electronic and mechatronic systems have to comply with strict environmental regulations while simultaneously facing growing cost pressures. Thus, a higher service temperature of up to 300 °C is being pursued in many fields, including the automotive industry, power engineering, and industrial metrology. This requires new solutions for the development of materials and technologies for packaging of integrated circuits, with hermetic housing being a key aspect.
Polymer-ceramic composite materials developed at Fraunhofer IKTS are used for the implementation of thermally stable hermetic housings. Polymer-ceramic composites consist of ceramic fillers and a matrix of organosilicon polymers. The polymer matrix can be transformed into a ceramic-like structure by heat treatment, resulting in a composite with enhanced thermal stability.
Following the selection of appropriate systems of silicone resins and optimized filler combinations, two composite systems for a two-step housing technology were developed. The first step comprises the encapsulation of the mechanically sensitive microelectronic component and bonding wires with a low-viscosity, cold-plastic pourable material by dip coating and subsequent thermal crosslinking. In the following step, a mechanically stable housing is formed out of a highly filled polymer-ceramic composite by thermoplastic joining and thermal crosslinking of two housing shells.
Investigations regarding the thermomechanical stability of the polymer-ceramic housing materials during heat treatment showed an initial reduction in flexural and tensile strength up to 300 °C but a sufficient and stable mechanical strength at higher temperatures.