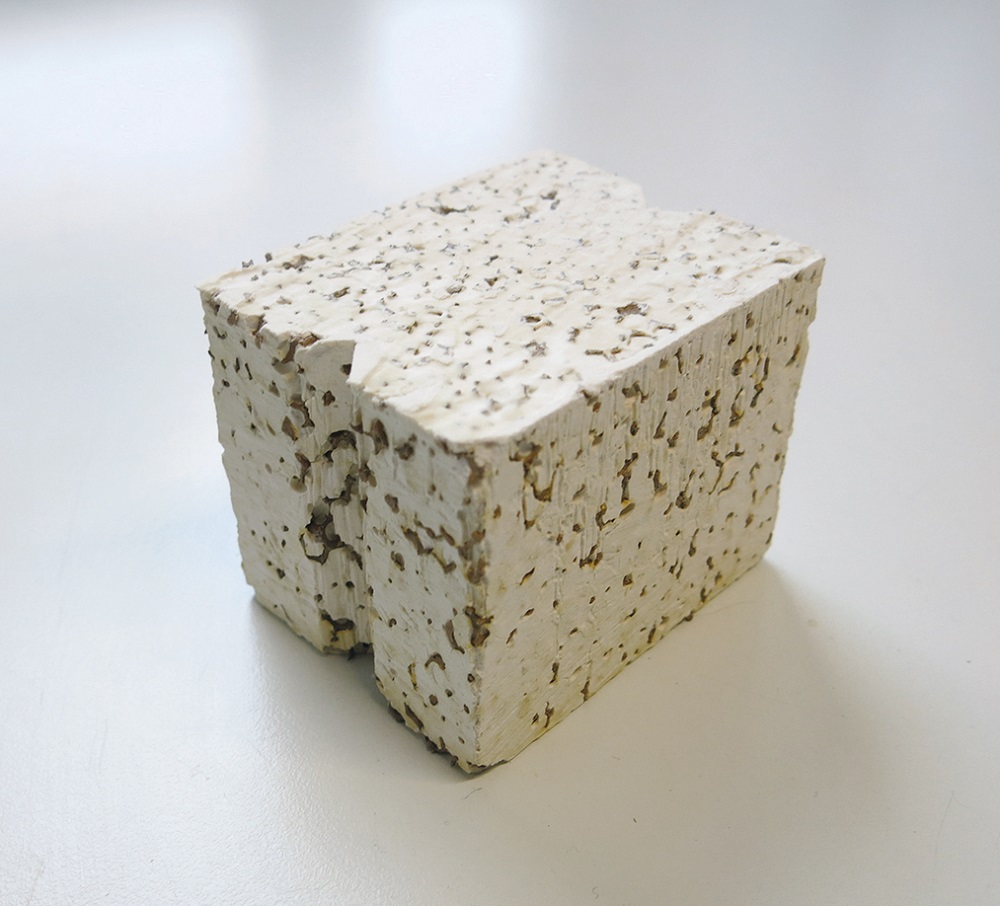
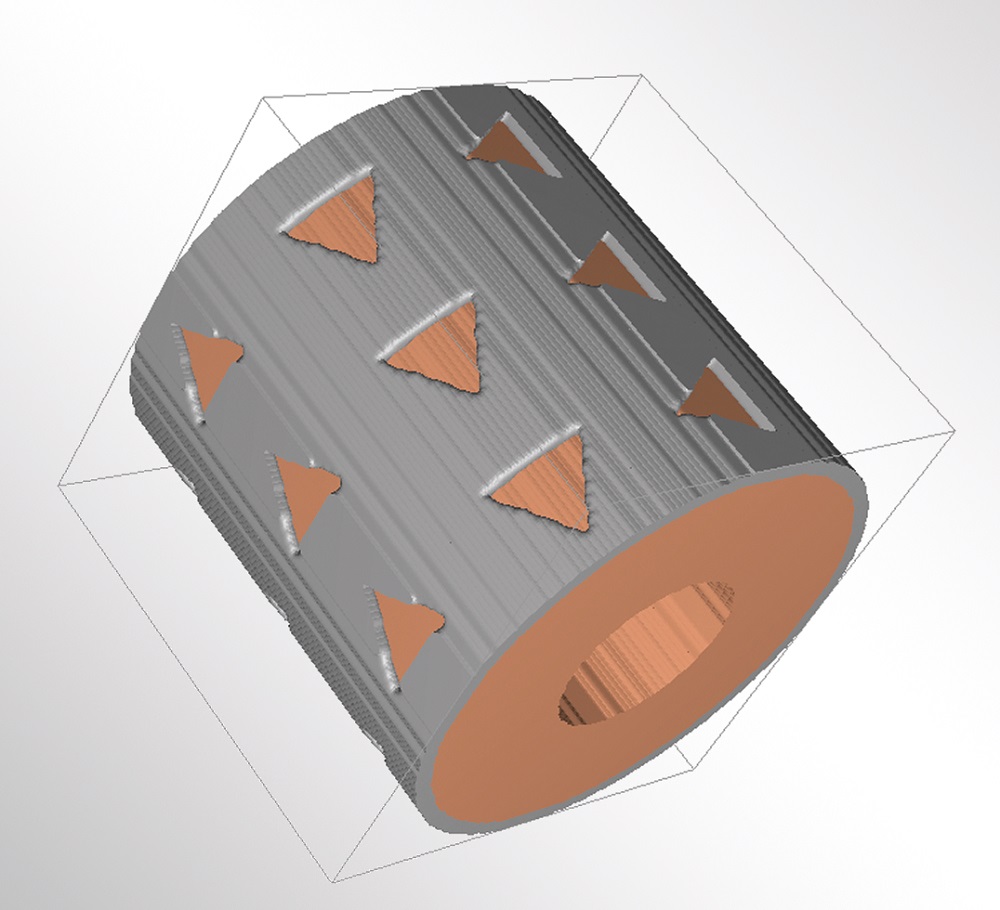
Thermochemical heat storage is a promising alternative to sensible or latent storage technologies based on water tanks. The heat is stored by means of a chemical potential, which enables high thermal energy storage densities and low energy storage losses, and can be retrieved at any time. Unlike with hot water tanks, insulation to prevent heat loss over time is not required. Typical materials for thermomechanical heat storage are silica gel and zeolites in the form of pellets, which offer a relatively low price and a high energy density. One disadvantage of these highly porous adsorbents, especially in packed beds, is their poor heat conductivity, which leads to a high loss in performance during charging and discharging and the need for complicated heat exchanger structures. Fraunhofer IKTS has extensive capabilities in modification and processing of highly porous ceramics and has applied them in different projects for the development of materials and components for heat storage applications. Within the scope of a Fraunhofer project, cylindrical pellets were covered with a good thermal conductor, such as copper or aluminum. These metal-covered pellets showed a thermal conductivity that was five times higher than that of conventional pellets and thus allowed for faster charging and discharging cycles. A different technological approach, taken within the BMWi project “MoGeSoWa“, was the development of heat storage bricks enabling a higher heat storage system filling degree and better contact with the heat exchanger than was achievable with packed beds. The network-like permeation of the bricks improved the accessibility of the adsorbate to the inner volume of the adsorbent. Another subject of this BMWi project was the development of so-called composite adsorbents. These materials consist of a mesoporous support structure that is impregnated by an inorganic salt. In contact with water, the salt forms different hydrate phases and thereby releases heat. The advantage of these materials is the comparatively low loading temperature (~ 90 °C). Typical support structures are silica gel, attapulgite, and carbons of large surface area. Investigations within this research field were concentrated on the generation of support structures with a high specific surfacearea and a tailored pore structure.
Services offered
- Development of ceramic materials for heat storage applications
- Development of composite materials for sorbent and catalytic applications
- Development of manufacturing methods for industrial production of developed composites
- Application tests
- Manufacturing and analysis of test samples and small batches
Acknowledgments
The authors gratefully acknowledge BMWi for the funding of the project “MoGeSoWa“ (project number: 03ESP259E).