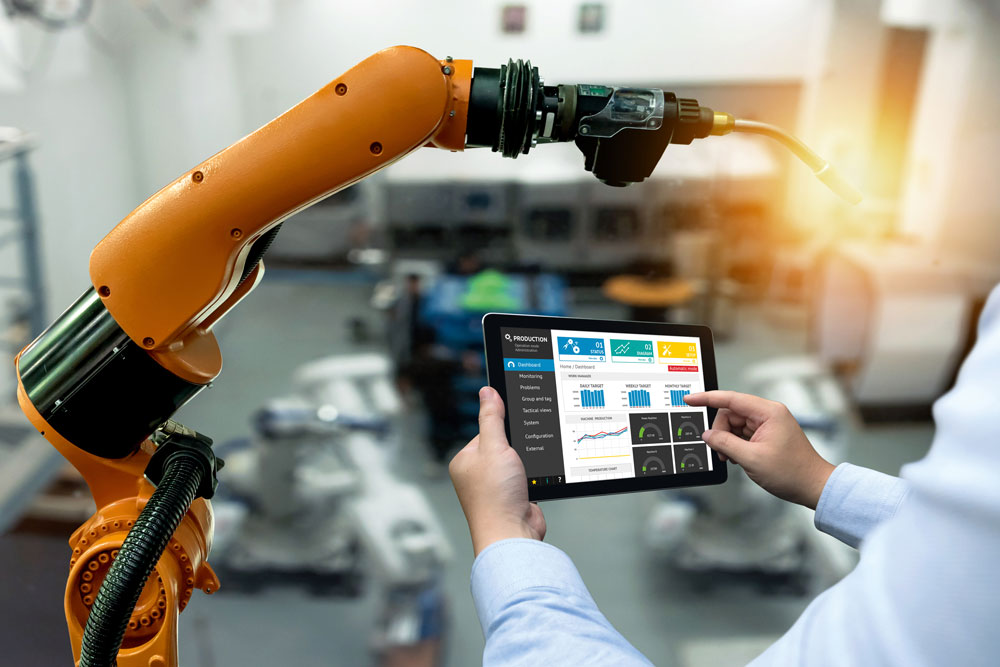
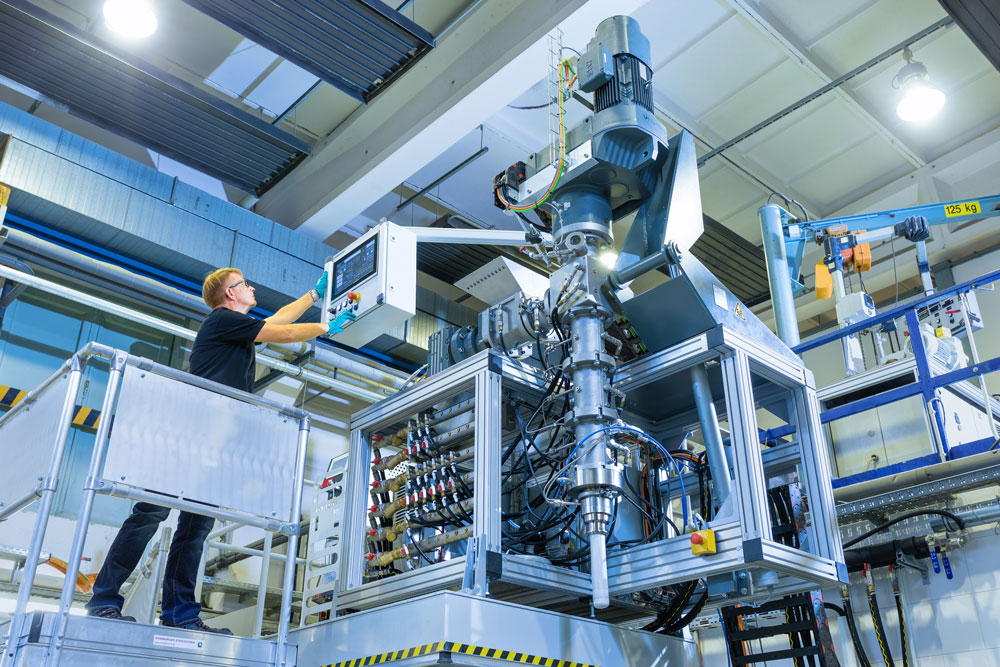
The comprehensive digitization of industrial production is key to optimizing the entire production chain and thus increasing the competitiveness of companies. This is particularly true for growth segments such as the large-scale production of energy storage devices and converters. The Battery Innovation and Technology Center BITC in Arnstadt is therefore working on solutions for the networked, digitally supported production of energy storage devices in an area of more than 5300 square meters. Researchers are testing innovative data-driven approaches to process monitoring, control and quality assurance on industry-scale pilot lines. Application-oriented training and further education programs ensure that companies along the entire value chain are involved and qualified at an early stage.
In order to ensure the highest possible quality in battery production with minimum waste, defects must be identified early on in the production process. Using innovative non-destructive measuring and testing technology, all relevant process parameters can be recorded at BITC. For the data volumes obtained, AI-based concepts for intelligent aggregation, structuring, evaluation and storage are used. Consequently, it is possible to recognize error patterns, optimize production flows and establish a holistic production data management. This opens up new quality criteria and standards in battery production.
Within the scope of production research for energy storage systems, the BITC focuses on the development of software (Data Systems work group) as well as the transfer into hardware components (Smart Machine and Production Design).
In addition to specific battery development issues, Fraunhofer IKTS is developing basic routines for a scalable production of complex energy storage devices and converters. The experience gained from battery research is currently being transferred into digitally supported production technologies for electrolyzers in the hydrogen economy as part of the hydrogen application center "Industrial Hydrogen Technologies Thuringia (WaTTh)".
Services offered
Production research for energy storage systems
- Data management
- Computing concepts
- Evaluation and analysis methods
- Workflow management
- Instrumentation and networking of process steps
- Evaluation of digitally supported production processes