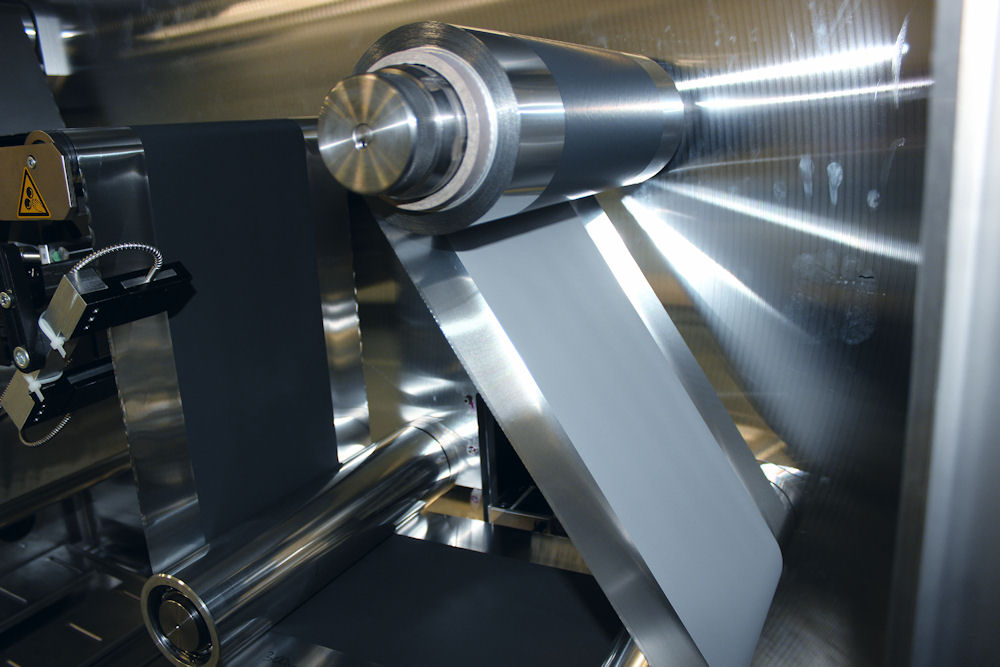
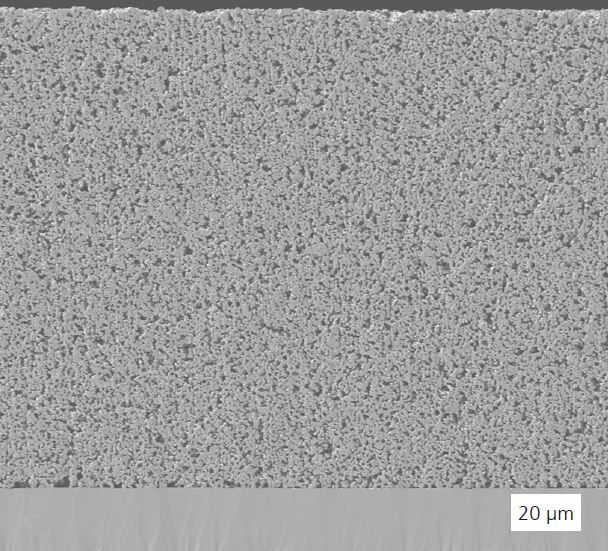
Fraunhofer IKTS has been cooperating with partners from industry and research in the development of large-format bipolar batteries (EMBATT concept) for several years now. Focus is on both materials development and targeted process modifications to address manufacturing-related challenges.
The bipolar construction of lithium-ion vehicle batteries can potentially enable a significant reduction in system complexity and thus an increase in the energy density and the range of electric vehicles. Optimization of the energy density starts with the electrode development. High surface loading with active material is important for increasing the proportion of storage material in the cell. At the same time, the mechanical workability and the necessary flexibility of the electrode tape have to be maintained.
Thick lithium titanate (LTO)-based electrodes made using waterbased processes and LTO-LFP bipolar electrodes have recently been developed and characterized. The first LTO electrodes produced showed very stable behavior for discharging up to approx. 1 C and reached the specific capacity (> 150 mAh/g) expected for LTO. For more detailed investigation of the rate capability, additional tests were carried out and electrodes with a layer thickness of up to 102 μm (calendered) were analyzed.
The specific challenges of water-based manufacturing of LTO electrodes mainly result from the fact that the aqueous LTO slurries have a high pH of 11.2–11.8. It has been shown that the alkaline pH is an intrinsic property of the active material and is not only due to the presence of synthesis contaminants. The high pH places high demands on the stability of the binder components for the aqueous LTO anodes and leads to corrosion of the aluminum collector foil during the coating process. In particular, pH values above 8.5 result in the formation of aluminum hydroxide and hydrogen (2Al + 6H2O = 2Al(OH)3 + 3H2↑). In the first aqueous LTO casting experiments, pore and crack formation as well as aluminum pitting corrosion was observed during electrode drying. As a result, the mixing process was adapted in such a way that the LTO slurry preparation was completely carried out at a pH of approx. 11, the normal pH for LTO. The pH of the slurry was shifted to the neutral range just before the casting process. In this way, stable electrodes with the described electrochemical properties could be realized.
This process has now been transferred to the pilot scale at the Battery Technology Application Center in Pleissa. The LTO anodes in combination with the aqueous lithium-iron-phosphate (LFP) electrodes already being manufactured at the center form the first bipolar electrodes produced on a pilot scale for the further development of the EMBATT bipolar battery.