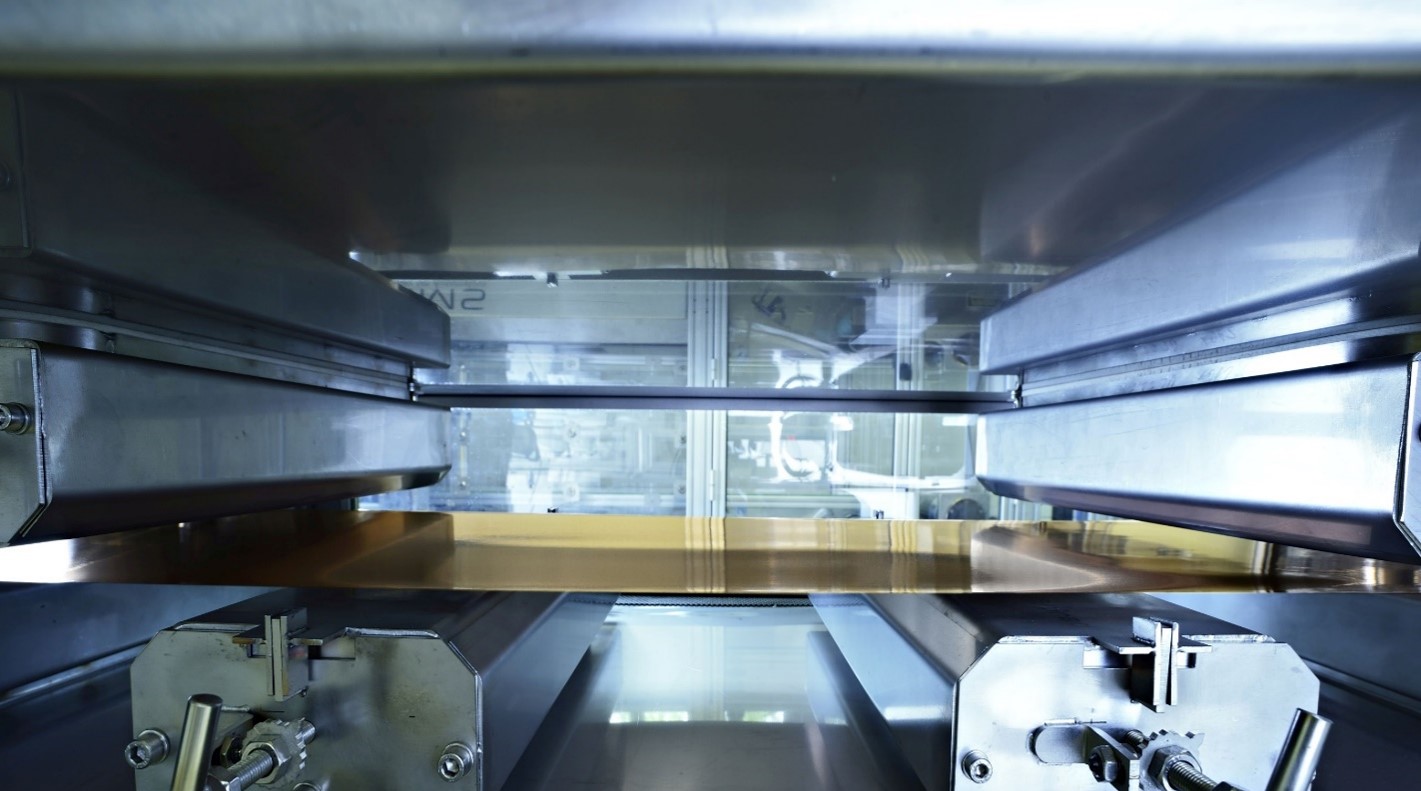
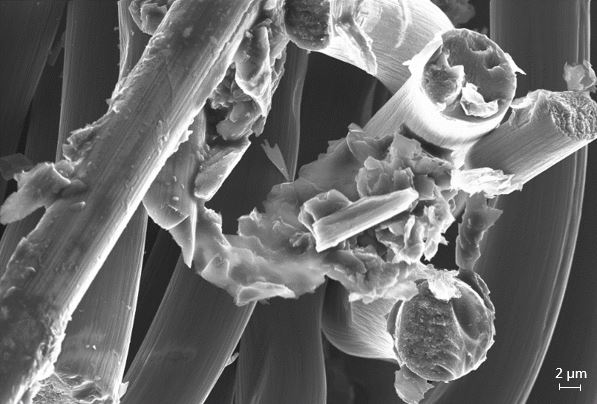
For the mobility sector in particular, increasing the energy density of lithium-ion batteries is important for reducing battery costs and increasing both the range and acceptance of electric vehicles. One approach has been to increase the mass loading of the active materials by increasing the thickness of the electrode layers. However, thicker electrode layers can lead to delamination of the active layer of the current collector, more difficult electrolyte penetration or higher electrical resistance, among other things.
Against this context, Fraunhofer IKTS and its research partners are pursuing new development approaches in the "LiBaStrom" project to increase the energy density of lithium-ion batteries. Innovative electrode architectures are being realized on the basis of three-dimensional current collectors, such as metal and graphite foams, carbon papers or expanded metals. The advantage of a 3D-structured current collector is the increased surface-to-volume ratio and thus a large contact area to the active material. As a result, a 3D conductivity network is formed, which enables fast electron transport through the entire electrode even at high active material loading. Compared to electrodes with metal tapes as current collectors, a 22 to 35 % higher gravimetric energy density can thus be expected.
In the project, customized electrode pastes are being developed for coating the 3D-structured current collectors. A silicon-based composite material (Si/C) is used for the anode and lithium nickel cobalt manganese oxide (NCM) for the cathode. The aim here is to realize high loadings of 70 to 100 mg/cm² on the NCM cathode and about 10 mg/cm² on the Si/C anode. This would significantly exceed the state of the art.
The formulations determined on a laboratory scale are then transferred to industrial coating processes for electrode production. Both the doctor blade and slot die processes, which are suitable for large-scale production, are used for this purpose. Depending on the 3D-structured current collector used, different process parameters are determined and optimized. This relates on the one hand to the actual coating of the current collector with the active component (wet film thickness, nozzle spacing, casting speed and pump power) and on the other hand to the management of the drying process.
The performance and stable operation of the pilot-scale 3D battery electrodes will be demonstrated for the first time in near-application pouch cells with electrode areas of 25 cm² and over 1500 cycles.
Funding: German Federal Ministry for Economic Affairs and Climate Action BMWK, Industrielle Gemeinschaftsforschung (IGF), AiF-Forschungsallianz Energie
Funding code: 58 EWBG
Project period: June 1, 2020 until November 30, 2022
Project partner: Universität Duisburg-Essen (UDE), Zentrum für Brennstoffzellen Technik GmbH (ZBT)