Author: Fanny Pohontsch, video: Marie Kaden
#diensttalk with software developer Stephan Heilmann
The Tuesday feature. In the #diensttalk series, our employees give a brief insight into their activities and reveal what vision drives them.
Stephan Heilmann develops software for test systems with the aim of ensuring maximum operational reliability – and this job has already taken him high up on wind turbines, on the railways, into the Paris sewers and to the bottom of the sea.
You came to the institute 13 years ago for your diploma thesis in media computing. Back then, you were working on the visualization of ultrasound data during the inspection of wheelsets and shafts in high-speed trains. How did that turn out?
If you have ever been on an ICE train in Germany, you can be sure that the wheels and shafts were tested non-destructively with our software and our equipment. Non-destructive means, here we are talking about the maintenance of all these components of our modern world that are too important to be allowed to break. And they are also too expensive to be allowed to break to see if they would still have worked – like these wheelsets, for example. This can also be rail infrastructure such as tracks, bridges, or overhead lines; or completely different applications such as underground pipelines, power plants, tanks in oil production facilities, or composite structures in wind turbines from foundations, including offshore, to blades. Our inspection systems detect defects in the structure before they spread and become dangerous.
»It's very fulfilling for me to see the practical opportunities that come from digitizing the entire lifecycle."
I now act as an active link between the industry and our development teams. My job is to translate the customers’ requirements for us as a solution provider. To do this, I spend a lot of time at trade fairs and conferences, and especially at the various plants, where I explore possibilities for the use of testing technologies, conduct trainings and install testing equipment.
What is the attraction of these activities for you and what are the challenges?
The exciting thing about the task and this entire system development is that I can accompany a product from the cradle to its use in the field, in the best case until it is ready for serial production. That is the core of Fraunhofer – closing the gap between research and industry and making sure that prototypes are used. And this step is often underestimated.
After all, a technology is not ready for use when it functions in the laboratory, but when it runs reliably 24/7 under the most adverse conditions, i.e. in dirty production environments, in rain, in snow, at minus ten as well as at well over 40 degrees. Together with the rail company Vossloh, for example, we developed a rail testing device that is now ready for series production and will also be used in the desert.
»We are not the workbench of the world, we need to be a knowledge carrier."
Access to high-maintenance components in industry is not always easy and without danger – how digital can it be? What is your vision as a software developer?
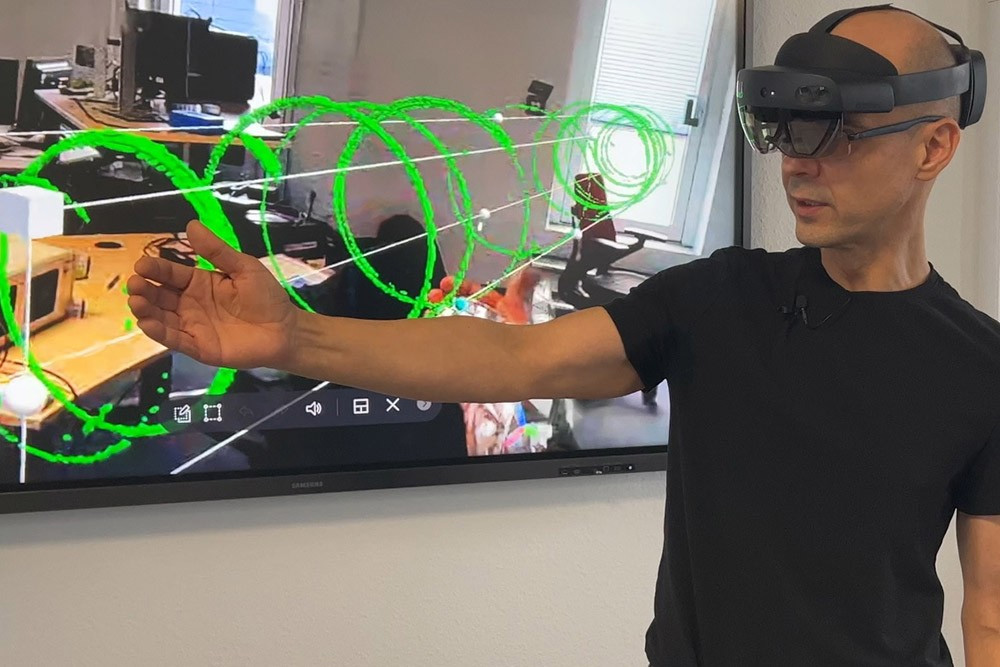
My vision is to increase efficiency and improve the entire production process. And that, in the end, the users are also happy with it. To achieve this, we use or translate virtual and augmented reality as well as artificial intelligence into concrete use cases. And it makes me very happy when this works and we see the new possibilities that arise in practice through the digitization of the entire life cycle, for example of a wheelset in a high-speed train.
That is also, I believe, what will enable us to hold our own here in Europe in the future: We are not the workbench of the world, we need to be a knowledge carrier. This transfer of knowledge, and thus also the increase in the efficiency of the components, ultimately benefits everyone. Production costs go down, maintenance costs go down, the reliability of the components themselves goes up, and the higher the load, both on people and on components in our world, which is constantly increasing in speed, that's the big challenge. That's a lot of fun for me! And a colleague always says: Find a job you enjoy and you'll never have to work a day in your life!
You spend a lot of time on the road, commuting between the IKTS sites in Berlin and Dresden, between commissioning, explorations and specialist conferences: How do you find a balance?
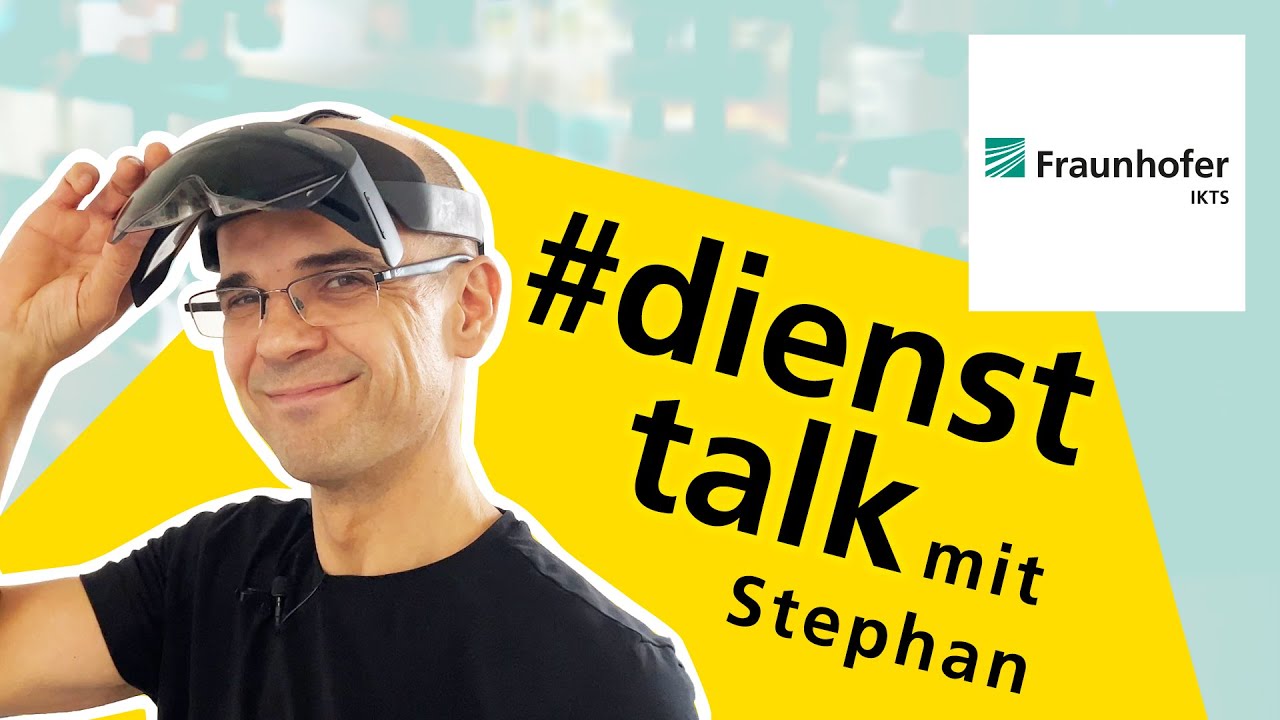
Privacy warning
With the click on the play button an external video from www.youtube.com is loaded and started. Your data is possible transferred and stored to third party. Do not start the video if you disagree. Find more about the youtube privacy statement under the following link: https://policies.google.com/privacyStephan Heilmann develops software for test systems with the aim of ensuring maximum operational reliability – and this job has already taken him high up on wind turbines, on the railways, into the Paris sewers and to the bottom of the sea
I find a balance through my family. I have two sons, six and nine years old, and they keep me busy. Apart from that, as an IT nerd, I'm also involved with computers and technology in my private life. I like diving, I go to concerts, and I find a special balance in medieval reenactments. And yes, I always find it hard to believe that there are only 24 hours in a day, and I always wonder how two years could have passed in the last two weeks.
Here you can find more #diensttalks. Take a look behind the scenes of Fraunhofer IKTS.
Further information
- Industrial solutions "Non-destructive testing"
- Augmented reality for rapid development and easy operation of NDT test equipment
- Industrial solutions "Ultrasonics"
- Quick introduction "Railway technology"
Also stay informed: You are welcome to subscribe to our newsletter, read our other blog articles and follow us on LinkedIn, Instagram and YouTube.