30 years Fraunhofer IKTS
Analytic competence: Far beyond ceramics production
In Germany, almost 70 percent of the energy used in industry is spent on thermal processes. Especially with regard to energy efficiency, CO2 reduction and resource conservation, complex questions must be answered. This almost always involves interactions – for example between temperature, time and gas atmosphere – and what influence these have on product properties and manufacturing processes. The “Thermal Analysis and Thermophysics” working group at Fraunhofer IKTS has been investigating thermal processes for 30 years. Since then, a lot has also happened in the laboratories: The simple measuring instruments with analog data output for thermoanalytical and thermophysical parameters have been replaced by modern, digital equipment. In the course of digitization, data is increasingly being coupled and made usable for modeling thermal processes and component properties.
“As the group name suggests, we have two main pillars: thermal analysis and thermophysics,” explains Dr. Mathias Herrmann, who heads the “Characterization” department. On the one hand, the researchers help other departments at IKTS with their developments; on the other hand, they are available to industrial companies as research and technology service providers.
The first pillar: Thermal analysis
The field of thermal analysis traditionally emerged from the development of ceramics and hard metals. “We work with devices that enable defined thermal treatment with simultaneous measurement of weight or length changes or even energy flows in the temperature range from -160 to 2400 °C. One of our specialties is working in special atmospheres,” explains group leader Dr. Tim Gestrich. The researchers know exactly when gases form in the ceramic component from the change in weight during the heating process. Then, the process temperature must be increased only slowly. Otherwise, the molded part could burst in the worst case due to the expanding gas. In addition, energy can also be saved in this way since the energy-intensive heating process can be precisely controlled. Further analyzers are available to characterize the gases released. In this way, the processes can be understood and optimized.
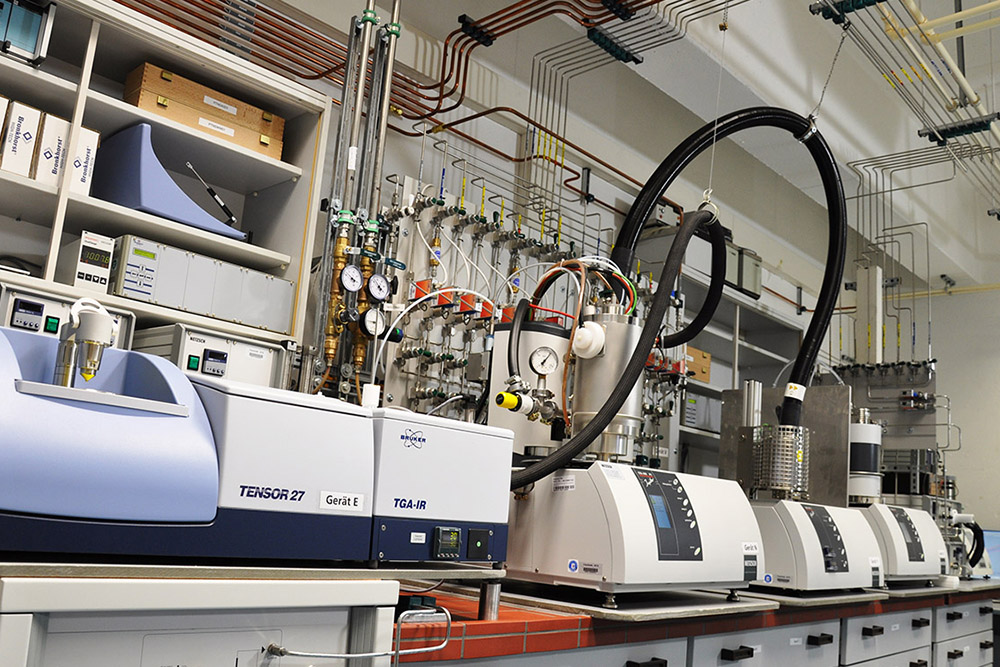
From the optimal ceramic firing process to CO2-free raw material production
The precise analysis of thermal processes is not only interesting for ceramic or hard metal production but can also be transferred to other thermal processes. “For example, on materials for batteries: We generate material characteristics, which we then use to simulate the thermal load of the batteries. Which materials are better, which are less suitable? We work together with automotive manufacturers on this, among others,” Gestrich reveals. Such data are also necessary for Industry 4.0 and the digital twin – without reliable material characteristics, thermal processes cannot be mapped.
Further examples are metal production and the production of chemicals. The starting point is often oxygen-rich compounds, such as ores, sulphates or minerals, which are thermally converted to the desired raw material with the release of CO2. If, for example, steel production is to succeed in the future without CO2 emissions, the processes must be converted from fossil fuels and reducing agents to hydrogen. “Since other temperature profiles are required for this, it is necessary to ensure that no undesirable side processes occur. Optimal final temperatures and reaction times are determined under precisely defined conditions. In addition, the reactors must be retrofitted. To implement such transformation processes in industry, we first need material data on a laboratory scale,” says Gestrich. Thermal data are also elementary for pyrolysis processes, i.e. for heat treatment, as used on cruise ships to carbonize the waste. What gases are produced in the process? And how can these be optimized in terms of their calorific values so that they can be used to generate energy? “In short, if you have questions about thermal mass transfer, you've come to the right place,” summarizes Herrmann.
The second pillar: Thermophysical analysis
If components and machines, such as turbines or engines, are to be optimally designed, the thermophysical properties must be known – such as thermal conductivity, specific heat capacity or expansion coefficient. Fraunhofer IKTS has DAkkS accreditation for these methods, which ensures the high quality of the data. “The special feature of our laboratory is its wide measuring range. We can determine physical parameters at temperatures from -100 °C to 2000 °C,” says Gestrich. “Another advantage is the complexity of our measurement equipment: not only do we look at a material sample with different probes, which gives us more detailed information on a wide range of properties, but we can also examine samples of very different sizes – up to 500 grams on the thermobalance. The results are then the basis for simulating even larger components and large furnace processes.” In doing so, the researchers are essentially focusing on two different issues: The material behavior itself and the component behavior. “Many thermal analysis laboratories are content with individual measurements. At IKTS, we use simulation calculations to determine the correlation to the components,” adds Herrmann. Another unique selling point is the measurement in defined atmospheres – from carbon monoxide, ammonia or hydrogen atmosphere to normal air with defined humidity.
Improved thermal conductivities for new substrate materials in power electronics
Thermophysical properties also play a role in power electronics. Here, Gestrich and his team are characterizing new substrate materials that dissipate heat quickly – for example, for rectifiers and inverters in cars, solar systems or wind turbines. “From low-cost raw materials, we are developing silicon nitride substrates with thermal conductivities of more than 100 watt-meter Kelvin,” Gestrich enthuses. In another project, IKTS has developed novel silicon carbide-bonded diamond materials that have thermal conductivities of over 600 watt-meter Kelvin – 50 percent more than copper. While other diamond materials have to be manufactured under high pressure, the underlying processes of Fraunhofer IKTS do not require high pressures and thus high energy input. To make such manufacturing processes reproducible as well as to achieve the excellent thermal conductivities, the know-how of the Analytics Group was also required.
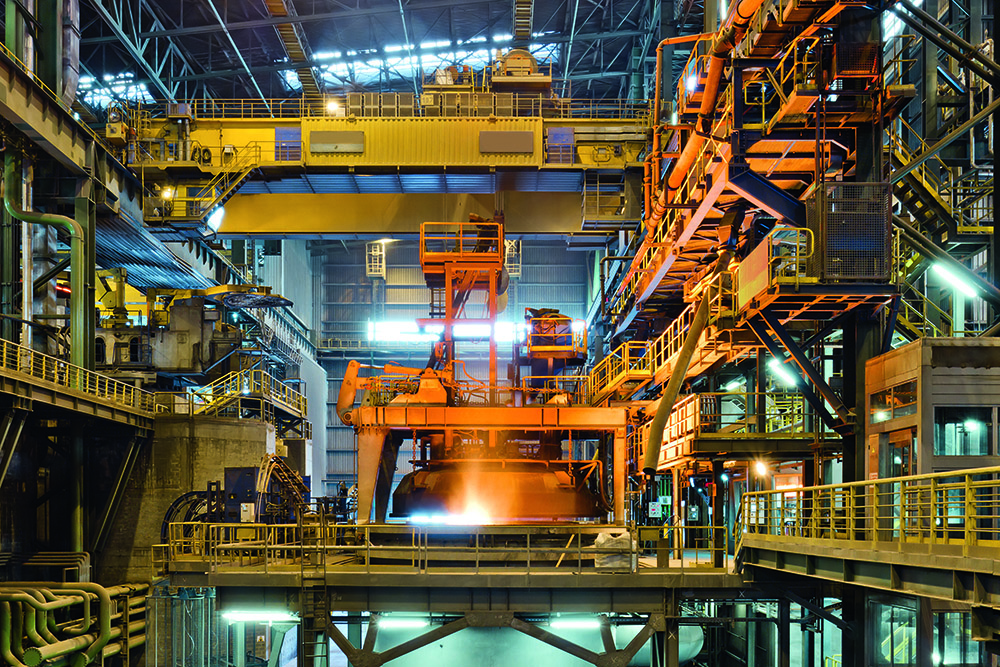
Vision for the future
Over the past 30 years, quite a bit of research work has already been done: The “Thermal Analysis and Thermophysics” working group, which currently has five employees, has worked with over 500 companies to date and carried out almost 70,000 tests. According to the researchers, in the long term, analytical skills are likely to become increasingly important for the circular economy. Herrmann points out that recycling of hardmetals, in which critical raw materials, such as tungsten and cobalt, are recovered and reprocessed, is well established. However, the recycling of technical ceramics and battery materials has still great potential. For this purpose, Fraunhofer IKTS researchers generate thermal and thermophysical data over the entire product life cycle in order to derive new strategies for resource conservation from them. “We see our future in integrating our data into thermal modeling processes – which we can then use to model, understand and optimize manufacturing and recycling processes and usage behavior in terms of heat consumption and product quality,” says Herrmann. Due to the strongly developing digitization processes (Industry 4.0), the parameters in the industrial process can increasingly be measured in real time and correlated with the data from the laboratory. In this way, effective time- and event-controlled profiles for thermal processes can be realized.
Further information
- IKTS Group "Thermal Analysis and Thermal Physics"
- IKTS Deparment "Sintering and Characterization"
- Industrial Solutions "Characterization I Analysis I Measurement I Testing"
Stay informed: You are welcome to subscribe to our newsletter, read our other blog articles and follow us on LinkedIn, Instagram and YouTube.