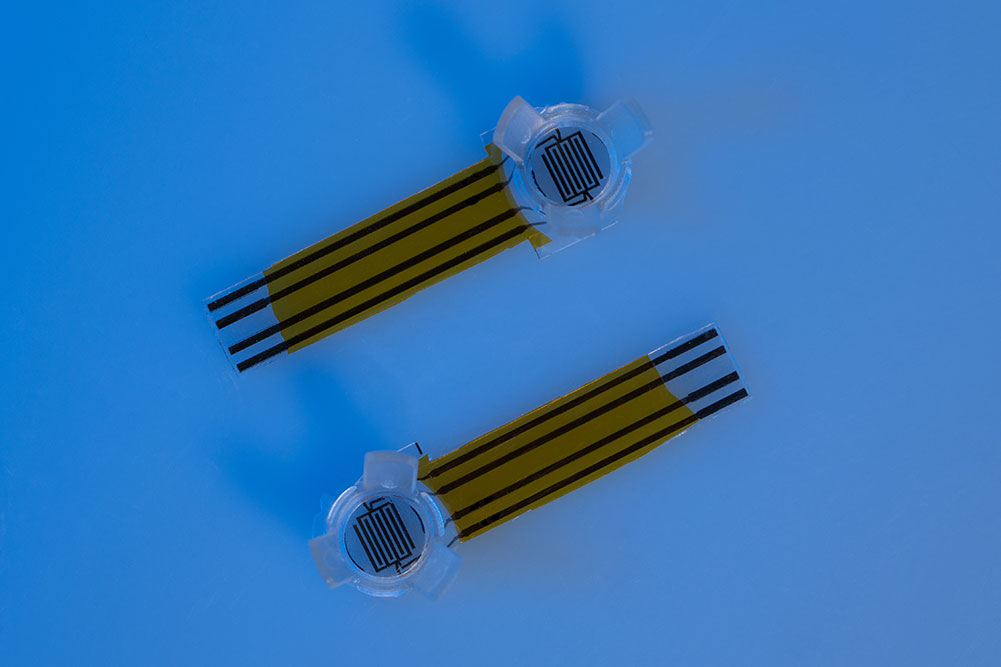
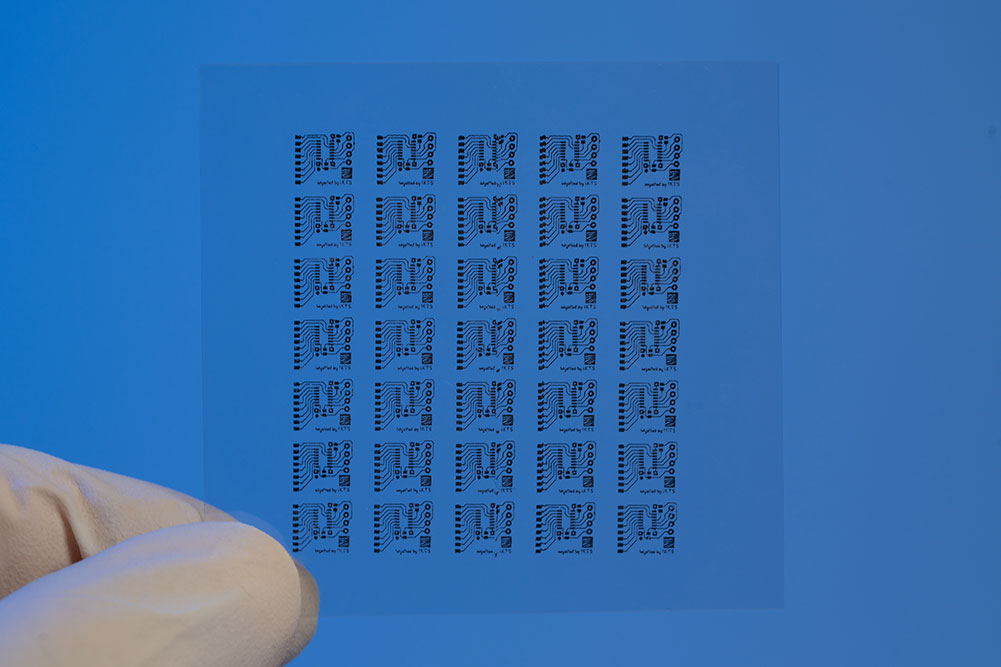
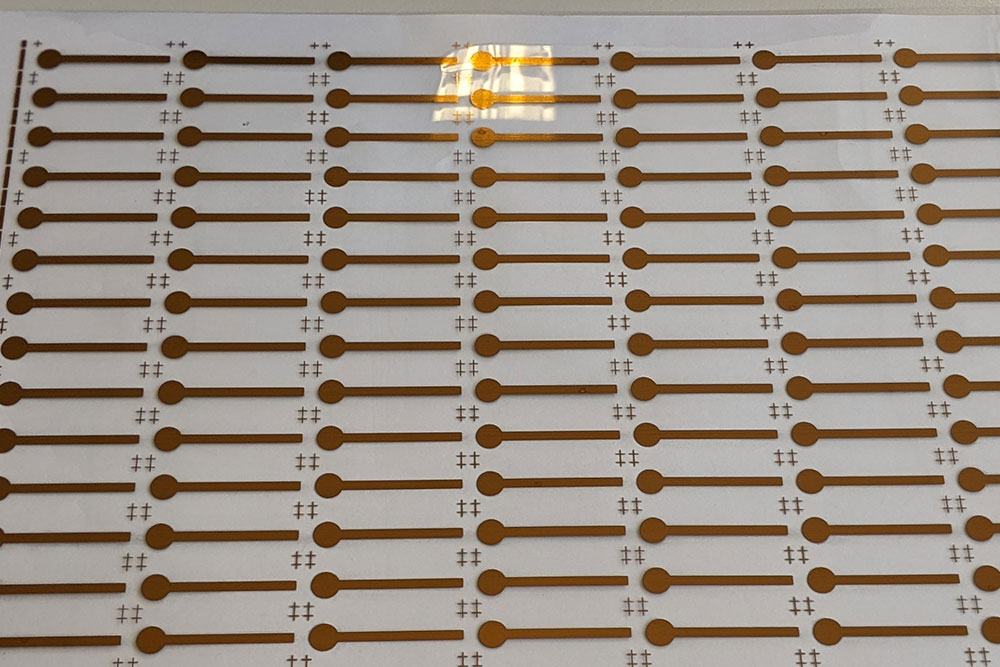
Our research in printed electronics and biocompatible electrodes is opening up exciting opportunities in medical diagnostics and sensing. Using innovative printing technologies, we can produce tailor-made electrodes for biosensors and cell model characterisation in microfluidics, among other applications. The direct printing approach offers significant advantages:
- Cost and time savings: The printing processes used, such as inkjet, aerosol jet and screen printing, avoid complex thin film processes (including masks, etching steps, ...) and are material saving.
- Flexibility and rapid prototyping: By using printing processes, prototypes and test versions of printed electrodes can be produced quickly and improved iteratively (rapid prototyping).
- Customisation through digital printing: Inkjet printing in particular allows electrode geometries and sizes to be easily adapted via software to meet the requirements of different biosensors.
- Scalability: The technological approach offers high scalability, i.e. large quantities of electrodes can be produced cost-effectively and in a short time (roll-to-roll production).
Fraunhofer IKTS has developed special inks and pastes that can also be printed on flexible substrates such as plastic or paper, enabling integration into wearable or flexible biosensor platforms. Our solutions for printable materials cover a broad spectrum:
- Gold, Platinum, Palladium for Electrodes and Sensitive Layers Our gold and platinum inks in the form of printed electrodes have been successfully tested several times for biocompatibility according to DIN EN ISO 10993-5 / -12 (Biological evaluation of medical devices - Part 5: Tests for in vitro cytotoxicity and Part 12: Sample preparation and reference materials).
- Carbon and silicon as cost-effective and alternative electrode materials.
- Other metals such as silver and copper for electrical wires and contacts.
- Marking inks for permanent marking and digital traceability of metallic or ceramic components using data matrix codes when other marking solutions such as laser marking or engraving are not an option.
- We also develop special formulations on customer request, e.g. composites with glass.
- The properties of all materials are tailored to the specific printing process and customer requirements.
We use modern, high-quality methods and processes for our research and development. These include:
- High-precision analysis to determine key material properties such as rheology and viscosity, surface tension and substrate wetting, particle size and sedimentation stability.
- Advanced inkjet (Dimatix DMP, Pixdro LP50, Ceradrop F-Series) with printheads from 2.4 pL to 80 pL, aerosol jet (Optomec M3D) and screen printing (Ekra E5, X5, HX2).
- Innovative sintering processes for the functionalisation of printed conductors using continuous line laser treatment (HDPL) and flash lamp processes (FLA).