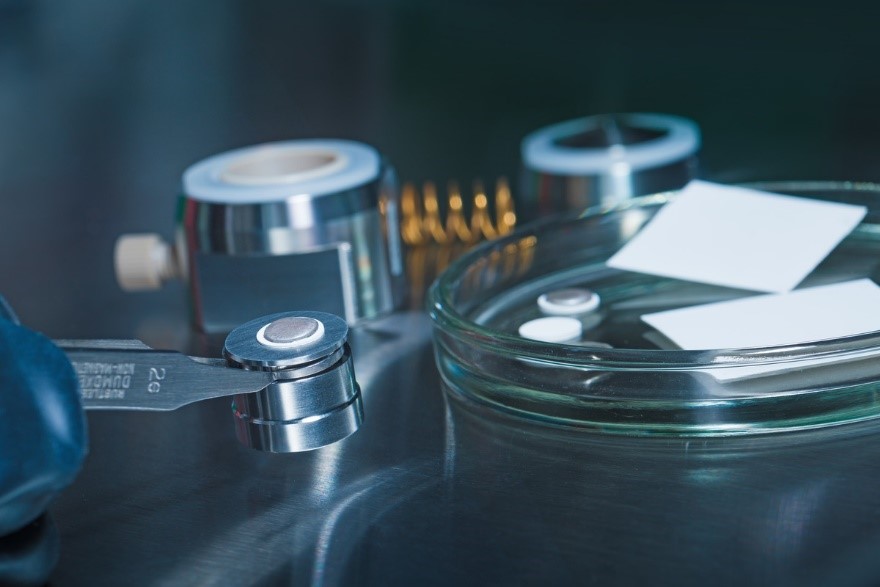
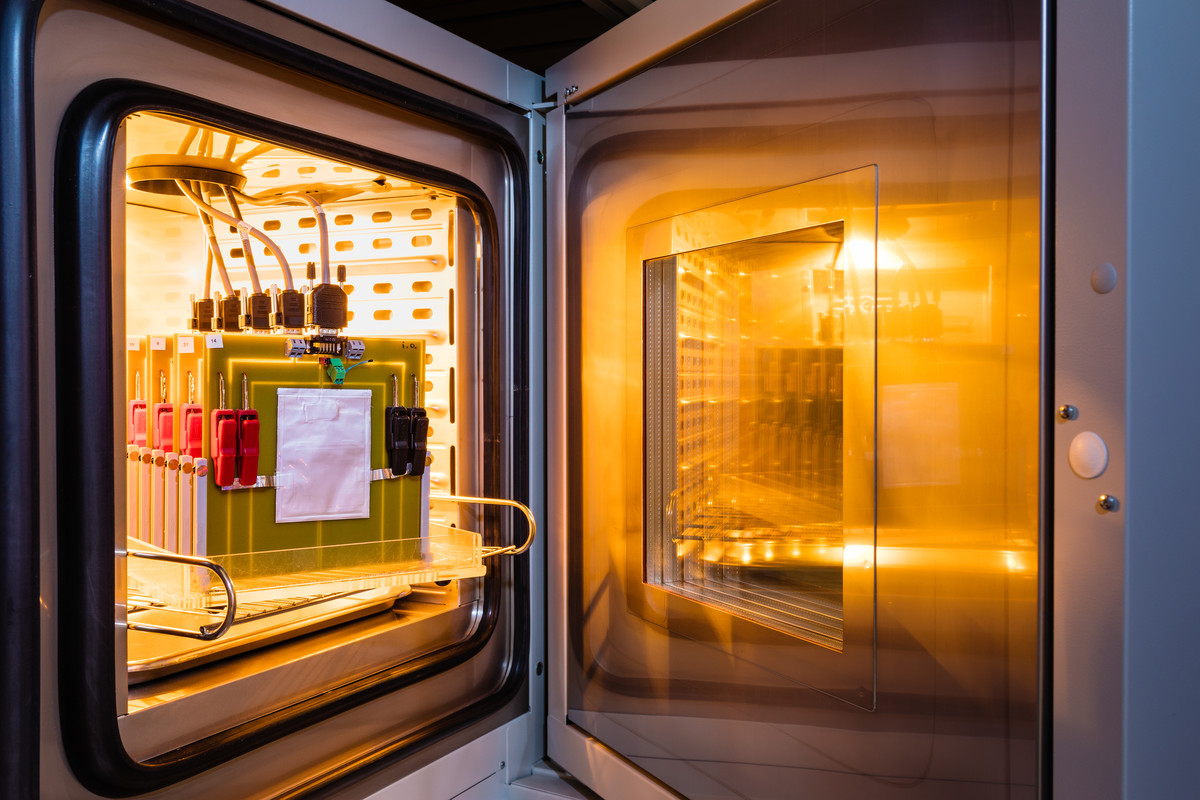
The Cell Design and Testing working group is concerned with the development, construction and characterization of test and demonstrator cells for novel battery concepts. One focus is on all-solid-state technologies in which the liquid electrolyte is replaced – ranging from polymers to completely inorganic solid electrolytes. Based on innovative materials produced and adapted at Fraunhofer IKTS, we develop new cell designs in monopolar and bipolar construction.
Another main topic is the characterization of commercial lithium-ion batteries and cells and their post-mortem analysis. A wealth of experience in investigated and evaluated cell types (button, pouch, bipolar and commercial cells) is contributed here. In addition to battery test benches, special gloveboxes and transfer facilities are available to complement the comprehensive analytical equipment available at IKTS. The focus is on the investigation of defects in the cell structure as well as material- and process-related degradation phenomena in the cell.
Services offered
- Electrical, electrochemical and material analytical characterization of materials and components for Li- and Na-solid-state batteries and lithium-ion batteries as well as next-generation cell chemistries
- Broad spectrum of electrochemical methods for determining material and component properties
- Technology assessment of solid-state batteries and consulting on cell concepts
- Post-mortem analyses of conventional cells to identify causes of cell failure and aging mechanisms and to determine simulation parameters