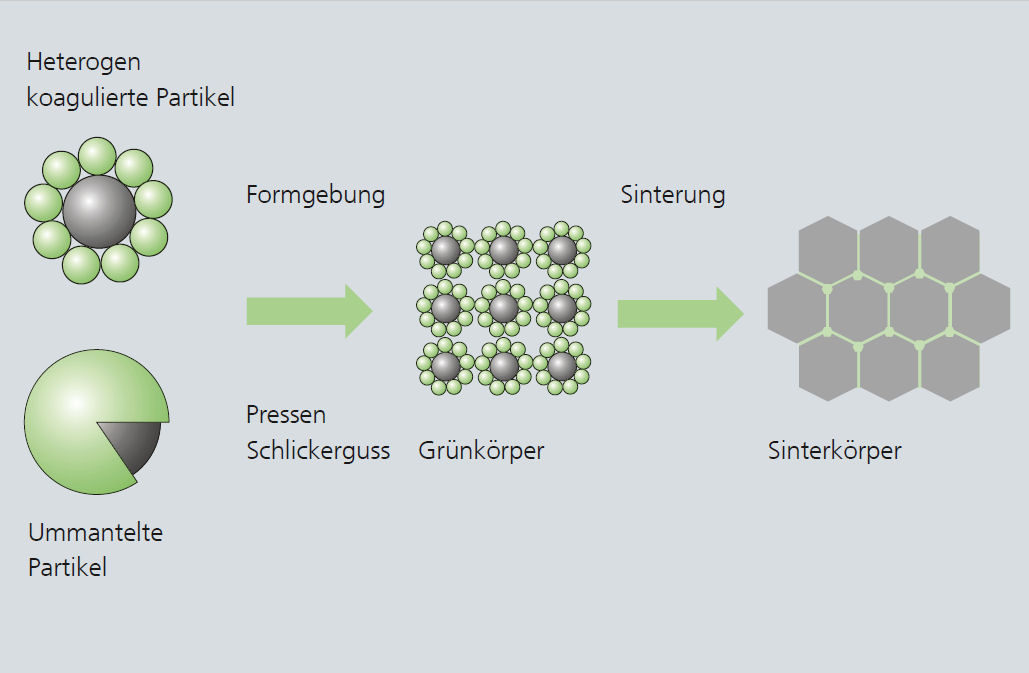
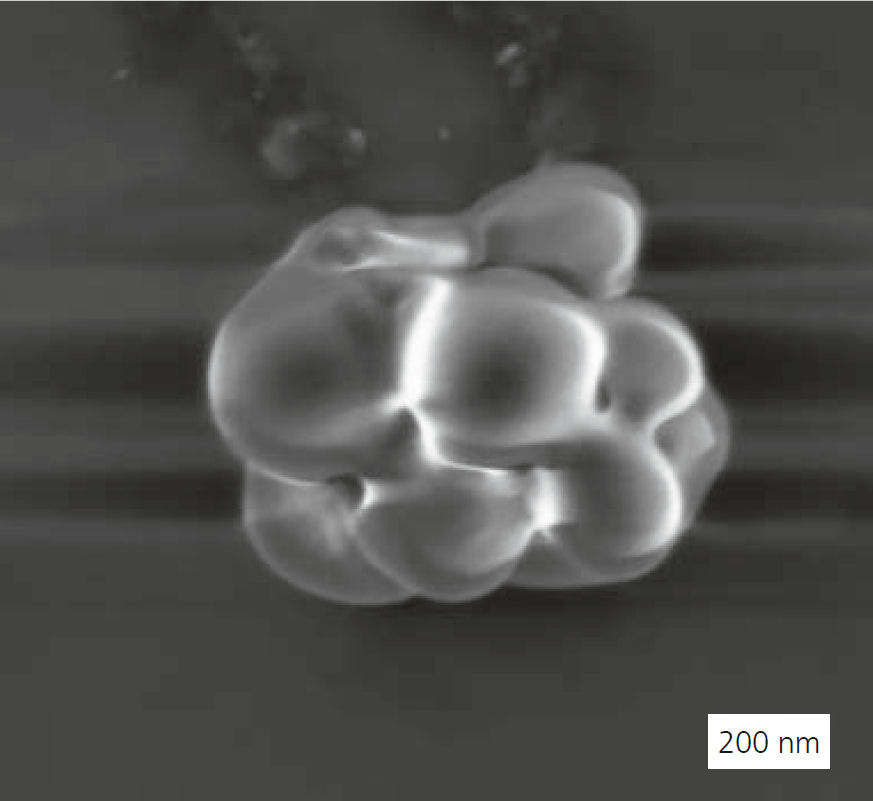
Zirkoniumdioxid verstärkte Aluminiumoxidkeramiken (ZTA) besitzen eine Vielzahl exzellenter Materialeigenschaften. Sie neigen beispielsweise weniger als reine Zirkoniumdioxidkeramiken zur hydrothermalen Degradation und sind somit sehr gut für medizinische Anwendungen geeignet. Darüber hinaus werden höhere Festigkeiten als bei unverstärkten Aluminiumoxidkeramiken erreicht. Zudem sind sie preiswerter herzustellen. Der entscheidendste Einflussfaktor auf die späteren mechanischen Eigenschaften von solchen Mischoxidkeramiken ist allerdings die Verteilung der einzelnen Phasen. Die Arbeiten im Rahmen des Wachstumskerns »pades – Partikeldesign Thüringen« fokussierten daher auf die Entwicklung von ZTA-Keramiken mit einer homogeneren Phasenverteilung (bei vergleichbarer Korngröße und Materialdichte), um möglichst größere Festigkeiten und Härten zu erreichen.
Bei der nasschemischen Beschichtung von Partikeln kommt zum einen die Methode der heterogenen Koagulation von verschiedenen festen Partikeln durch Variation der Oberflächenladungen und zum anderen die Ummantelung eines festen Partikelkerns mit einer flüssigen Zweitphase (Flüssigphasenbeschichtung) zum Einsatz. Im Rahmen des vorgestellten Projekts wurde letzteres Verfahren genutzt. Dabei wurde zunächst der kommerziell verfügbare pulverförmige Rohstoff Aluminiumoxid (Al2O3) nasschemisch mit der Zweitphase Zirkoniumdioxid (ZrO2) beschichtet. Neben Kleinstmengen (< 100 g) – hergestellt in einem Rotationsverdampfer – sind auch größere Mengen im Drehrohrofen produzierbar. Die auf einem Aluminiumoxidpulver erzeugte Partikelbeschichtung (Core-Shell) zeigt bereits die gleichmäßige Verteilung der Zweitphase (Bild 2). Im Anschluss wurde das Material vorwiegend durch uniaxiales Pressen weiterverarbeitet. Die so hergestellten Keramiken weisen nach dem Sinterprozess, verglichen mit konventionell produzierten Keramiken aus kommerziellen Rohstoffen, eine bis zu 20 % geringere Korngröße und eine homogenere Phasenverteilung auf. Die entwickelte Technologie zur Verfeinerung des Materialgefüges (Bild 1) ist vergleichsweise kostengünstig und großtechnisch nutzbar sowie einfach auf weitere Materialklassen übertragbar.
Leistungs- und Kooperationsangebot
- Werkstoffsynthese und -entwicklung auf Basis kommerziell verfügbarer Rohstoffe und Werkstoffneuentwicklungen: dichte ein- und mehrphasige Oxidkeramiken auf Basis von Sinterkorund (Al2O3), Spinell (MgO·Al2O3), Zirkoniumdioxid (ZrO2) oder andere Oxide (Y2O3, Y3Al5O12, etc.), Dispersionsgefüge oder Werkstoffverbunde
- Werkstoffspezifische Formgebung und Entwicklung von prototypischen Bauteilen und Pilotserien
- Begleitende Charakterisierung und Analyse
- Beratung zu werkstoff-, konstruktions- und einsatzspezifischen Fragestellungen