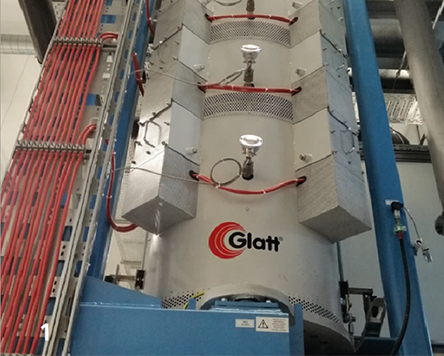
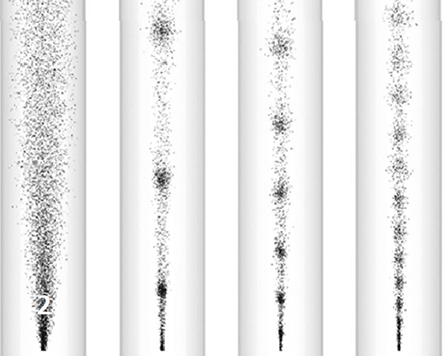
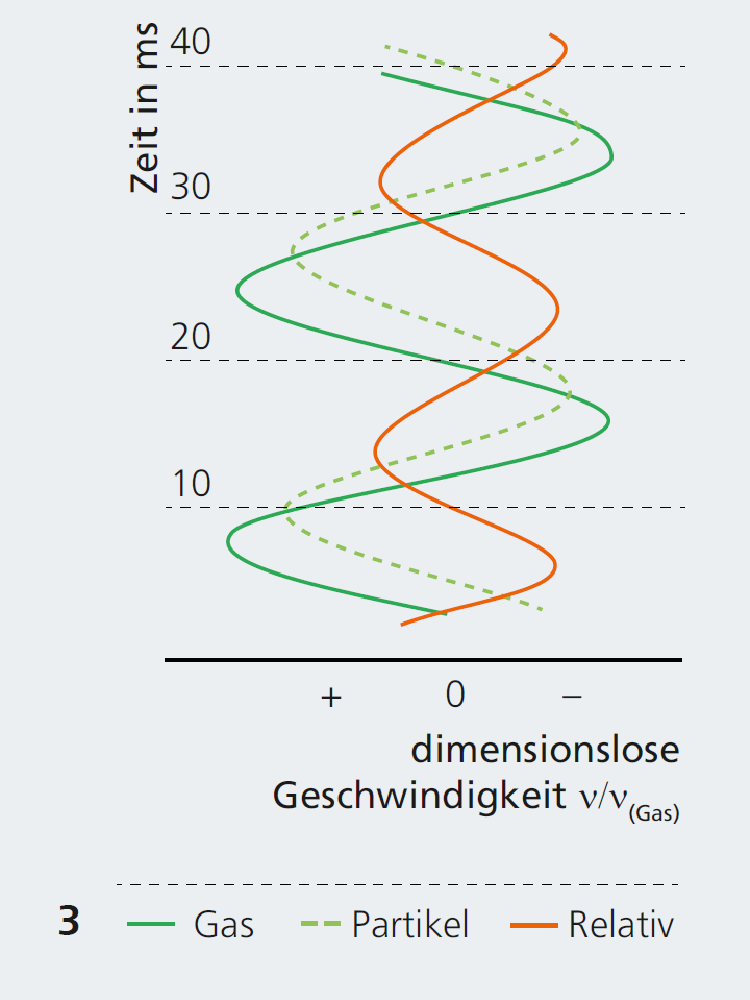
Oxidische Hochleistungskeramiken für die Medizintechnik oder für Optikkomponenten erfordern hohe mechanische und optische Eigenschaften. Diese werden durch spezielle Pulvereigenschaften erzielt: Neben der Partikelgröße (< 100 nm) spielen ein hoher Reinheitsgrad, eine enge Korngrößenverteilung und die Kornform eine wesentliche Rolle. Am Fraunhofer IKTS wurde weltweit die erste Anlage zur Herstellung von maßgeschneiderten, oxidischen Nanopulvern im Kilogramm-Maßstab aufgebaut, die auf einem flammenlosen Konzept mit pulsierender Gasströmung beruht (ProAPP®, Glatt Ingenieurtechnik GmbH, Patent DE102018205152A1).
Das Syntheseprinzip basiert auf der Sprühpyrolyse, wobei das Prozessgas mittels einer Pulsationseinheit in eine dynamische Druckschwingung versetzt wird. Die Frequenz und Amplitude kann von 0–400 Hz bzw. 0–60 mbar eingestellt werden. Nach einer Vorheizphase strömt das pulsierende Gas in ein vier Meter langes Rohr aus Al2O3. Dabei kann es über elektrisch betriebene Heizer auf bis zu 1300 °C erhitzt werden. Der Rohstoff in Form von Pulvern, einer Lösung, Suspension oder Emulsion wird über eine Zweistoffdüse in den Reaktionsraum eingebracht. Das Besondere hierbei ist, dass die aufgeprägte Pulsation eine turbulente Strömung erzeugt, die den Wärme- und Stoffübergang im Vergleich zu einer laminaren Strömung um den Faktor 2–5 erhöht [1]. Dadurch können die thermoschockartige Zersetzung und die darauffolgende Kristallisation in kürzester Zeit stattfinden. Im Gegensatz zu einer laminaren Strömung, bei der die Strömungsgeschwindigkeit zum Querschnittsmittelpunkt zunimmt, erfahren die eingedüsten Rohstoffe bei einer turbulenten Strömung eine über den Querschnitt gleichbleibende Behandlungsintensität, so dass jeder Partikel dieselben Bedingungen erfährt. Dies hat eine geringere Streuung der Pulvereigenschaften zur Folge. Je nach Produktwunsch kann das Prozessgas inert, reduzierend oder oxidierend gewählt werden. Der entscheidende Vorteil liegt in der kontrollierten Einstellungsmöglichkeit der Prozessparameter, um gezielt den Phasenzustand, Morphologie, Korngröße- und Verteilung zu verändern. Nach der Reaktionszone wird, infolge einer schlagartigen Abkühlung mit Luft sichergestellt, dass keine weiteren Reaktionen ablaufen. Ergänzt wird der Synthesereaktor durch eine Glasapparatur zur Vorbereitung der Präkursoren.
Mit diesem Verfahren können ZrO2/Al2O3-Pulver für die Medizintechnik (z. B. Gelenkersatz) hergestellt werden, die aufgrund des feinen Gefüges eine erhöhte Festigkeit und Zuverlässigkeit aufweisen. Polykristallline Mg-Al-Spinellpulver können zu Linsen oder Scheiben verarbeitet werden und hohe Transmissionswerte bei gleichzeitig hohen mechanischen Eigenschaften gewährleisten. Außerdem bietet dieses Verfahren die Möglichkeit zur Synthese von Pulvern für YAG-Laser, Katalysatoren und Core- Shell-Partikeln.
[1] Kudra, T.; Mujumdar, A.S. Advanced Drying Technologies, 2nd ed.; CRC Press: Boca Raton, FL, USA, 2009.