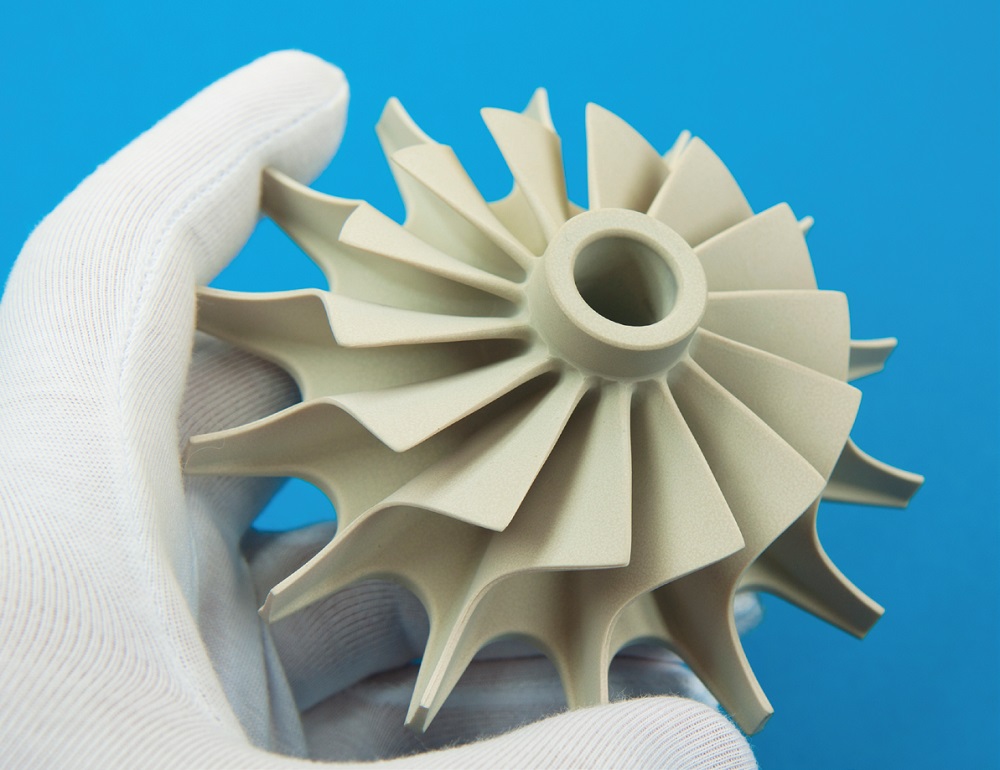
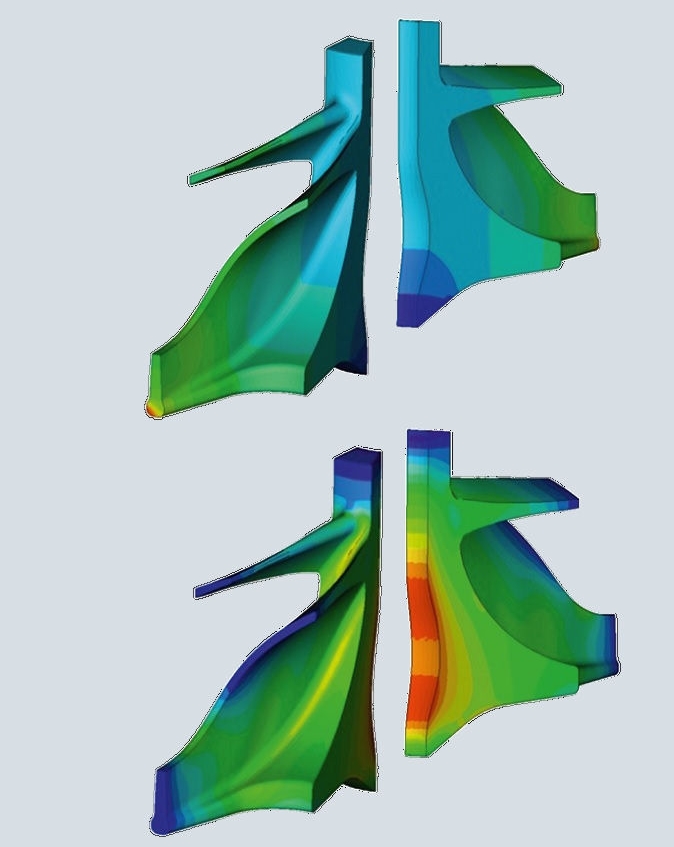
Hochleistungskeramiken finden in Gasturbinen neben diversen elektrischen Anwendungen hauptsächlich als Wärmedämmschutz Verwendung. In Flugzeugtriebwerken und stationären Gasturbinen werden sie in Form von Kacheln oder Beschichtungen auf metallischen Bauteilen eingesetzt und ermöglichen so eine Anhebung der Brenngastemperatur oder einen verminderten Kühlbedarf. Beides führt zu einer Erhöhung des Wirkungsgrades und somit zur Verminderung des Treibstoffverbrauchs und der Schadstoffemissionen.
Mit vollkeramischen Bauteilen kann der Wirkungsgrad von Triebwerken und Gasturbinen noch weiter gesteigert werden. Unter den Keramikwerkstoffen eignet sich dafür besonders Siliciumnitrid. Si3N4 besitzt herausragende thermomechanische Eigenschaften – auch bei sehr hohen Temperaturen.
Leistungsangebot
- Entwicklung speziell angepasster keramischer Werkstoffe für den Hochtemperatureinsatz sowie in oxidativen und korrosiven Atmosphären und Medien
- Applikationsorientierte Charakterisierung von Werkstoffen und Bauteilen
- Mechanische Prüfung von Raumtemperatur bis Hochtemperatur (1550 °C)
- Oxidationstest bis 1600 °C
- Heißgaskorrosionstest bis 1450 °C unter gasturbinenähnlichen Bedingungen
- Prototypenentwicklung und Tests unter anwendungsnahen Bedingungen