Additive Glasformgebung verbessert Selektivität von
Photomultiplier
Um winzigste Verunreinigungen in Bierhefe oder kleinste Erbgut-Fragmente in Blutproben zu finden, werden beispielweise bei der Lebensmittelherstellung oder in medizinischen Laboren Photomultiplier genutzt. Das sind ultrapräzise Detektoren, die Lichteffekte von nur geringer Intensität erfassen und zuverlässig messen können. Damit sich diese optoelektronischen Sensoren künftig noch viel breiter einsetzen lassen, haben das Messtechnik-Unternehmen ProxiVision und Ingenieure vom Fraunhofer-Institut für Keramische Technologien und Systeme IKTS gemeinsam additiv gefertigte Photomultiplier entwickelt. Damit wird es möglich sein, die Sensoren schnell und flexibel auf immer neue Einsatzszenarien anzupassen.
Im Interview geben Prof. Dr. Rolf-Jürgen Ahlers (Geschäftsführer ProxiVision GmbH), Dr. Tassilo Moritz (Abteilungsleiter »Verfahren und Bauteile«, Fraunhofer IKTS) und Dr. Jochen Schilm (Gruppenleiter »Fügetechnik und AVT«, Fraunhofer IKTS) einen Einblick, wie dieses Forschungsprojekt begann, welche technologischen Pfade sie beschritten und welche Perspektiven sie für neue Anwendungen sehen.
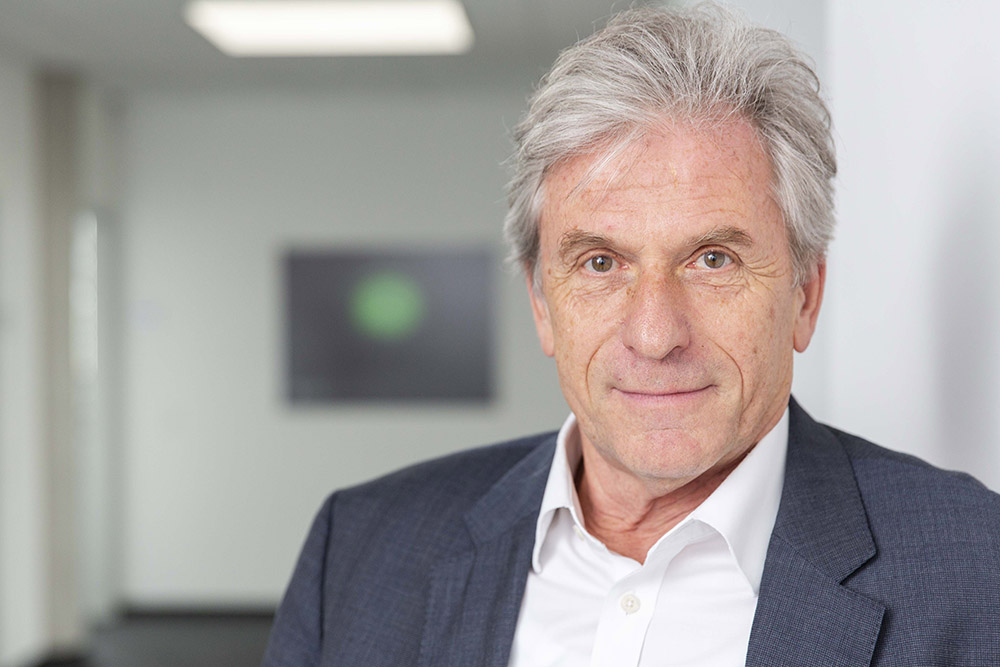
Wie kam es zur Kooperation zwischen ProxiVision und dem Fraunhofer IKTS?
Tassilo Moritz: Mitarbeiter von ProxiVision hatten unseren Stand bei einer Pulvermetallurgie-Messe besucht. Wir hatten dort gezeigt, welche neuen pulvertechnologischen Formgebungsverfahren es inzwischen für den Werkstoff Glas gibt – und das stieß bei ProxiVision auf Interesse.
Rolf-Jürgen Ahlers: Dazu muss man wissen, wie wir unsere Photomultiplier bisher formen: Wir erwärmen Glasrohre, biegen sie zurecht und weiten sie nach hinten zu Trichtern auf. Das heißt aber auch: Wir sind hier in der Geometrievielfalt und Feinheit der Strukturen beschränkt. So kam es zu der Idee, durch neue Fertigungsmethoden flexibler zu werden. Der Glas-Spritzguss, den das IKTS auf der Messe gezeigt hatte, erschien da zunächst vielversprechend.
Doch dieser hat sich als Sackgasse erwiesen?
Tassilo Moritz: So würde ich das nicht sagen. Aber tatsächlich ist uns recht rasch klar geworden, dass wir solche komplexen Strukturen viel besser durch additive Fertigung erzeugen können. Die Frage war bloß, welches der uns zur Verfügung stehenden Verfahren, die wir für Keramik nutzen, das Beste für das Glasbauteil von ProxiVision sein würde. Deshalb haben wir gemeinsam Projektmittel aus dem »Zentralen Innovationsprogramm Mittelstand« beantragt und im Zuge dieses ZIM-Projekts drei verschiedene additive Verfahren erprobt.
Welche Verfahren waren das konkret?
Tassilo Moritz: Wir haben es unter anderem mit »CerAM FFF« versucht. Dabei verrät das Kürzel »Cer« schon, dass diese Technologie eigentlich für keramische Bauteile entwickelt wurde. AM steht für »Additive Manufacturing« und FFF für »Fused Filament Fabrication«. In diesem Verfahren legt der 3D-Drucker Glasfilamente ähnlich wie Zahnpasta-Stränge nach und nach zur gewünschten Geometrie übereinander. So entsteht ein sogenannter Grünkörper, der dann beim Sintern bis auf die geforderte Bauteilgröße schwindet. Das Ergebnis war hier allerdings, dass FFF einfach nicht die strukturellen Details erzeugen kann, die für einen Photomultiplier gebraucht werden. In anderen Versuchen haben wir »CerAM MMJ« eingesetzt, auch »Multi Material Jetting« genannt. Dabei wird das Bauteil aus winzigen Tröpfchen aufgebaut, in denen Glaspulver und thermoplastische Binder vermischt sind. Doch die Oberfläche der damit hergestellten Bauteile war für den Einsatzzweck zu rau.
Und das dritte AM-Verfahren hat schließlich das Rennen gemacht? Was waren die Vorteile?
Tassilo Moritz: Ja, tatsächlich hat sich »CerAM VPP«, also Vat Photopolymerization, als Treffer erwiesen. Dabei handelt es sich um eine additive Fertigungsmethode, bei der Monomere – also kurze Kunststoff-Moleküle – durch Licht ausgehärtet werden. Konkret sieht das so aus: Wir bestreichen den Boden einer durchsichtigen Wanne mit einer dünnen Schicht aus einer Glaspulver-Monomer-Suspension. Von unten strahlt ein Projektor mittels »Direct Light Processing« die Schicht durch den Wannenboden mit einer bestimmten Lichtwellenlänge an und härtet an den gewünschten Stellen die Monomere aus, wie man das von Kunststofffüllungen beim Zahnarzt kennt. Dann hebt eine Plattform die gerade erzeugte Bauteilebene ein Stückchen hoch, die nächste Suspensionsschicht wird auf den Wannenboden gestrichen, die Plattform senkt sich wieder auf Kontakt zur Suspension ab, die Schicht wird wieder angestrahlt. Dies wird so lange wiederholt, bis der Grünkörper fertig ist. Dabei hat sich gezeigt: Mit diesem Ansatz lassen sich komplexere Strukturen erzeugen – mehr Krümmungen und Kanäle – als beim traditionellen Herstellverfahren, was zu einem höheren Verstärkungseffekt führt. Damit haben wir künftig die Möglichkeit, viel bessere und genauere Photomultiplier herzustellen als bisher.
Rolf-Jürgen Ahlers: Das kann ich nur unterstreichen. Mit dem neuen Ansatz sind wir nicht mehr durch unsere Formgebung begrenzt. Vielmehr können wir die Geometrie so designen, dass wir das Optimum hinsichtlich der Funktionsweise eines Photomultipliers erreichen. Konkret: Wir können so die Intensität und Rauscharmut des Sensors weiter steigern.
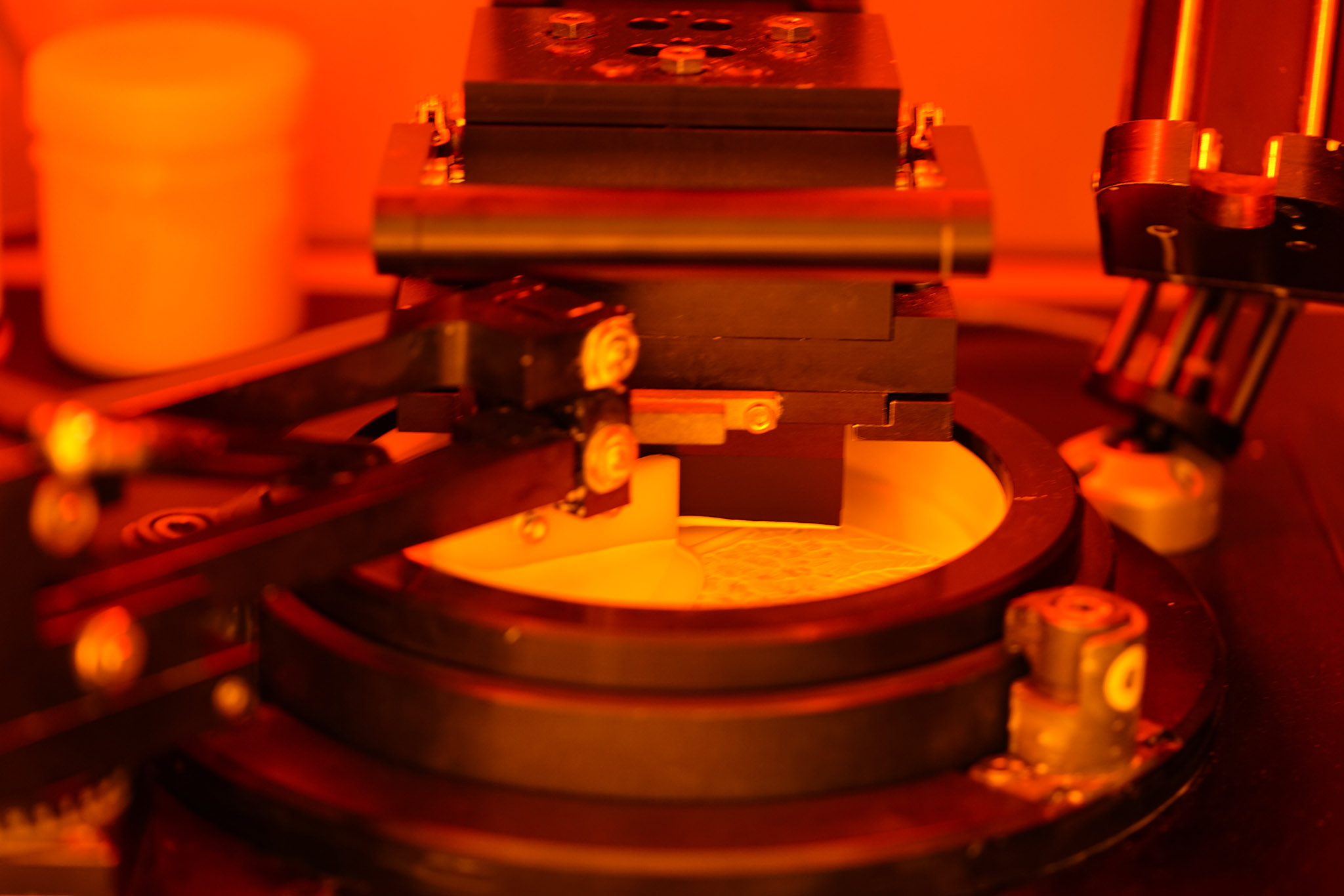
Eignet sich das Verfahren für die Industrie, wenn man die Geschwindigkeit betrachtet, mit der ein Bauteil gedruckt wird?
Jochen Schilm: Es sind bereits Anlagen mit größeren Wannen und Bauflächen in der Entwicklung. Darauf können mehrere Bauteile auf einmal hergestellt werden und damit verkürzt sich dann auch die Herstellungszeit pro Teil drastisch. So wird man auf Geschwindigkeiten kommen, die bisher dem Spritzguss vorbehalten waren.
Rolf-Jürgen Ahlers: Außerdem müssen Sie bedenken: Bei uns geht es nicht um Massenprodukte. Wir stellen kleine Serien her, die wir immer wieder an die ganz verschiedenen Wünsche unserer Kunden anpassen. Von daher bringt uns dieses additive Verfahren voraussichtlich genau die Flexibilität, die wir uns gewünscht haben. Dadurch rechnen sich dann auch kleinere Serien für Anwender.
Welche verfahrenstechnischen Hürden galt es bei der Anpassung von CerAM VPP zu überwinden? Sicher kann es nicht 1:1 von Keramik auf Glas übertragen werden.
Jochen Schilm: Da die Glaspartikel in der Suspension im Gegensatz zu Keramikpartikeln durchsichtig sind, mussten wir die Belichtungsparameter anpassen. Am herausforderndsten war es aber, den optimalen Sinterprozess einzustellen, so dass am Ende ein dichtes Bauteil entsteht. Die Glaspartikel dürfen nämlich nur langsam erweichen, aber nicht anfangen zu schmelzen. Denn dann würden sich die Bauteile verziehen oder die Bauteilkanten verrunden.
Welche neuen Anwendungen könnten Sie durch den Einsatz dieses Verfahrens möglichweise erschließen?
Rolf-Jürgen Ahlers: In Zukunft könnten Photomultiplier zum Beispiel in Kläranlagen messen, wie stark die Abwässer mit Hormonen, Antibiotika oder anderen problematischen organischen Substanzen belastet sind. Auch in der Raumfahrt, Umwelttechnik, Medizintechnik, Lebensmittelindustrie und in vielen anderen Branchen sehe ich viel Potenzial.
Tassilo Moritz: Denkbar wäre auch, dadurch verschiedene medizinische Untersuchungsmethoden miteinander zu kombinieren wie MRT mit Tumormarkern.
Wie geht es nun weiter? Wird ProxiVision dieses additive Fertigungsverfahren schon demnächst in der Produktion einsetzen?
Tassilo Moritz: Ganz so weit sind wir noch nicht. Es wird bestimmt noch anderthalb Jahre dauern, bis wir diesen Punkt erreicht haben. Bis dahin müssen wir das Verfahren noch produktionstechnisch optimieren. Zusätzlich könnte man auch in einem Projekt untersuchen, wie sich die Produktion um weitere Fertigungsschritte wie Laserbearbeitung oder Laserlöten ergänzen ließe.
Rolf-Jürgen Ahlers: Da kann man zum Beispiel auch an die Beschichtung denken, an elektrisch leitendes Glas oder integrierte Widerstände. Generell sehe ich jedenfalls gute Chancen, mit diesem Ansatz in Zukunft ganz neue Anwendungsfelder für Photomultiplier zu erschließen.
|
Weitere Informationen
- IKTS Abteilung »Verfahren und Bauteile«
- IKTS Gruppe »Fügetechnik und AVT«
- Glas lernt selbst zu leuchten und zu heizen
- Additive Fertigung mit Keramik, Hartmetall und Glas
- Badbasierte Photopolymerisation (VPP): Mit blauem Licht zu hochkomplexen Strukturen
- Multi Material Jetting (MMJ): Vier Werkstoffe – ein Bauteil
Bleiben Sie informiert: Melden Sie sich gern für unseren Newsletter an, lesen Sie in weitere Blogbeiträge rein oder folgen Sie uns auf LinkedIn, Instagram und YouTube. Wir freuen uns, mit Ihnen ins Gespräch zu kommen.