Autorin: Fanny Pohontsch
Multi Material Jetting (MMJ): Vier Werkstoffe – ein Bauteil
1. Station der vierteiligen Fotoserie: Additive Fertigung mit Keramik, (Hart)-Metall und Glas
Eine Komponente aus unterschiedlichen Materialien, die mehrere Funktionen, wie beispielsweise elektrische Isolation und Leitfähigkeit, vereint – derartige multifunktionale Strukturen ließen sich bislang nur mithilfe mehrerer kombinierter Herstellungsverfahren aus gefügten Einzelteilen fertigen. Aus diesem Grund entwickelten Steven und seine Kollegen das Multi Material Jetting, kurz MMJ.
»MMJ ist weltweit einzigartig und ermöglicht es erstmals, bis zu vier Materialien in einem einzigen Bauteil zu vereinen – mit hoher Güte und in nur einem Prozessschritt. Neben oxid- und nitridkeramischen Werkstoffen können auch Gläser und Metall-Keramik-Komposite verarbeitet und miteinander kombiniert werden. Oder Hartmetalle: Mit MMJ können daraus endkonturnahe Werkstücke gedruckt werden, die fast gar nicht mehr nachbearbeitet werden müssen. Das spart Zeit und Geld«, hebt Steven Weingarten hervor.
Die Fertigung basiert auf partikelgefüllten thermoplastischen Massen, sogenannte Feedstocks, die aufgeschmolzen und über Mikrodosiersysteme Tropfen für Tropfen hochpräzise abgelegt werden.
Lesen Sie dazu in der Bildstrecke zum MMJ:
Feedstock-Aufbereitung und Konstruktion
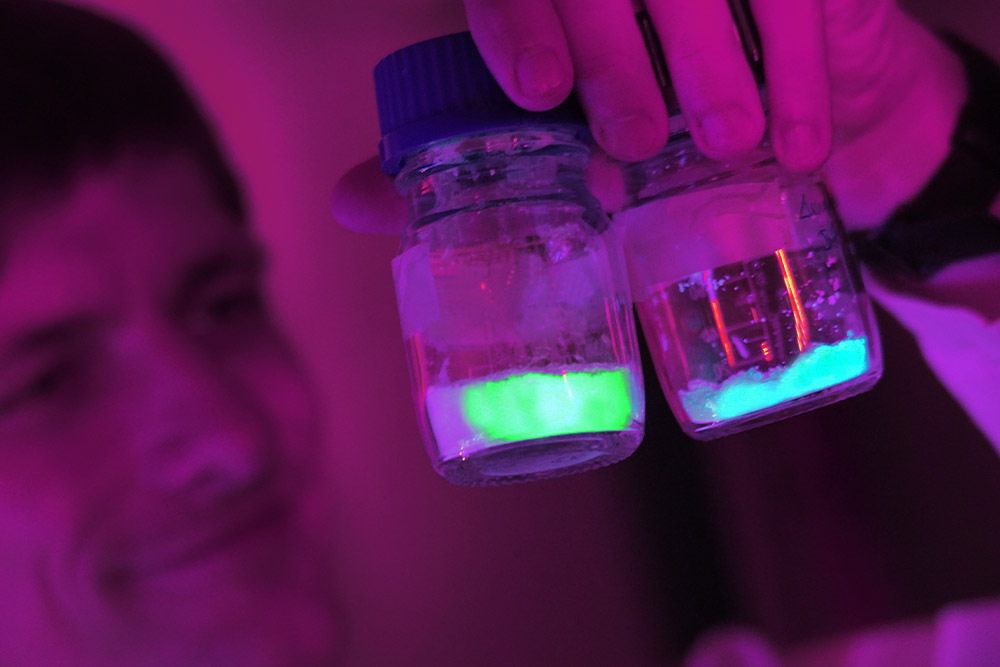
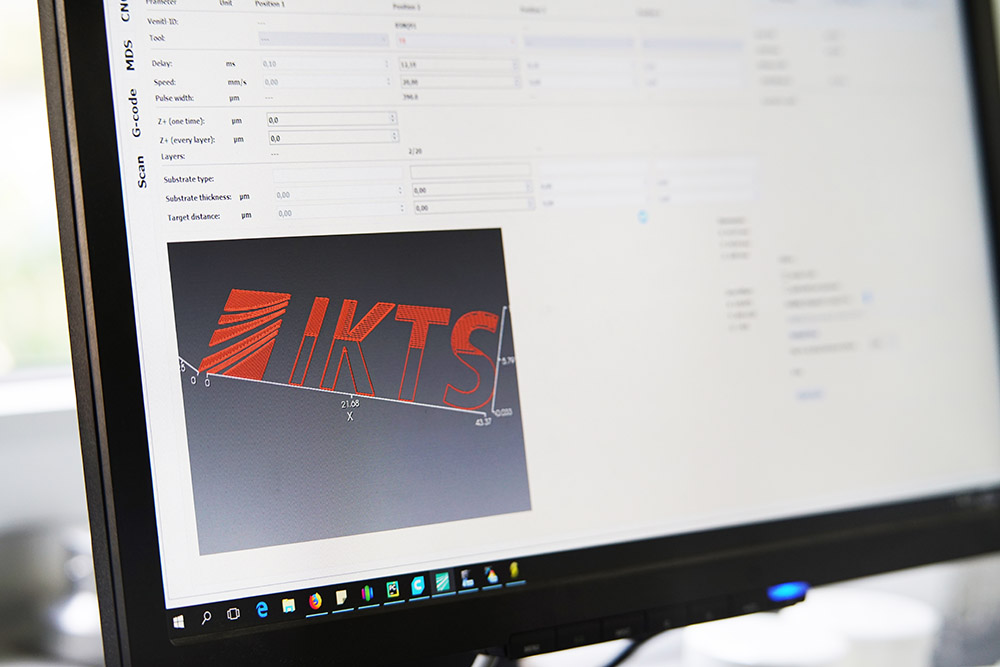
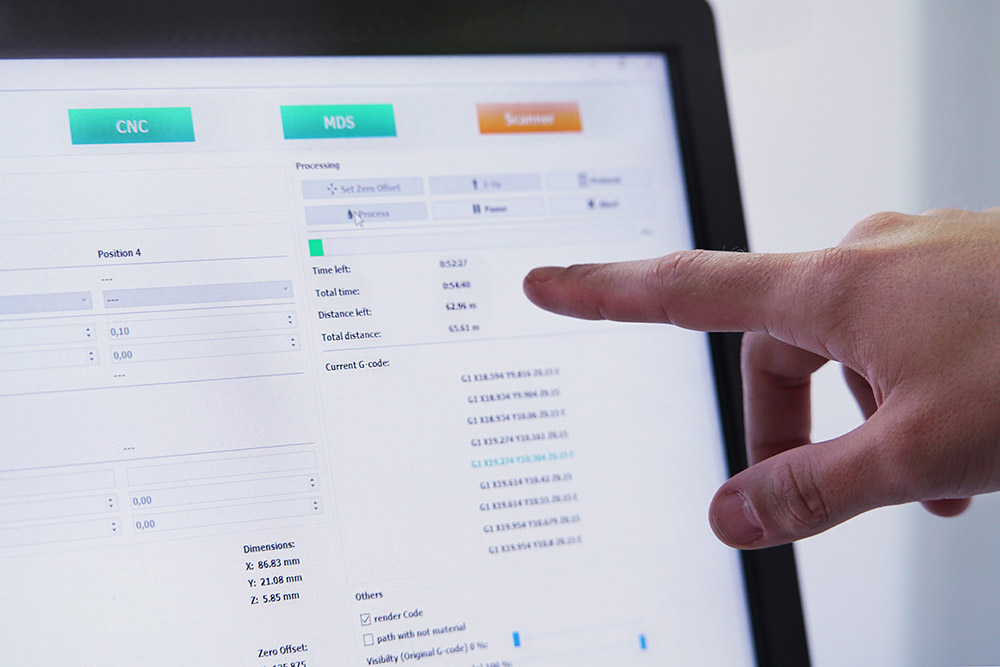
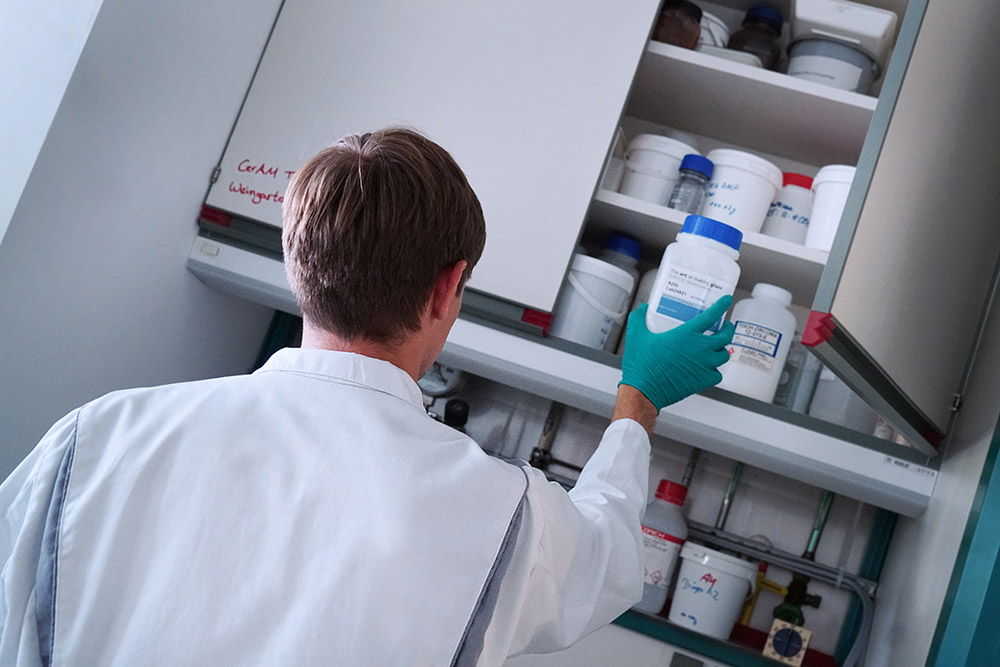
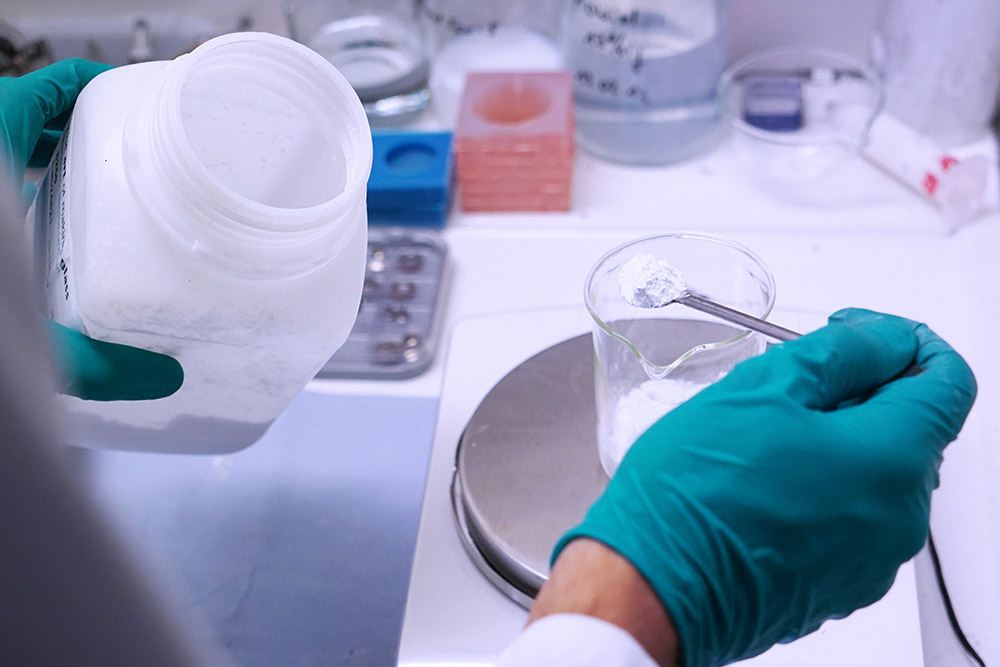
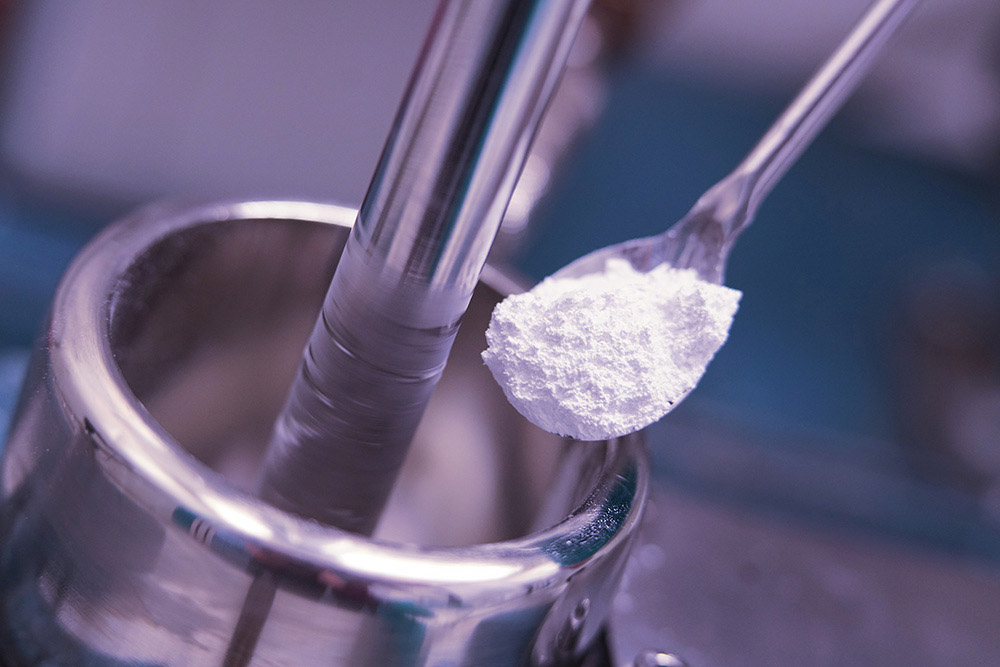
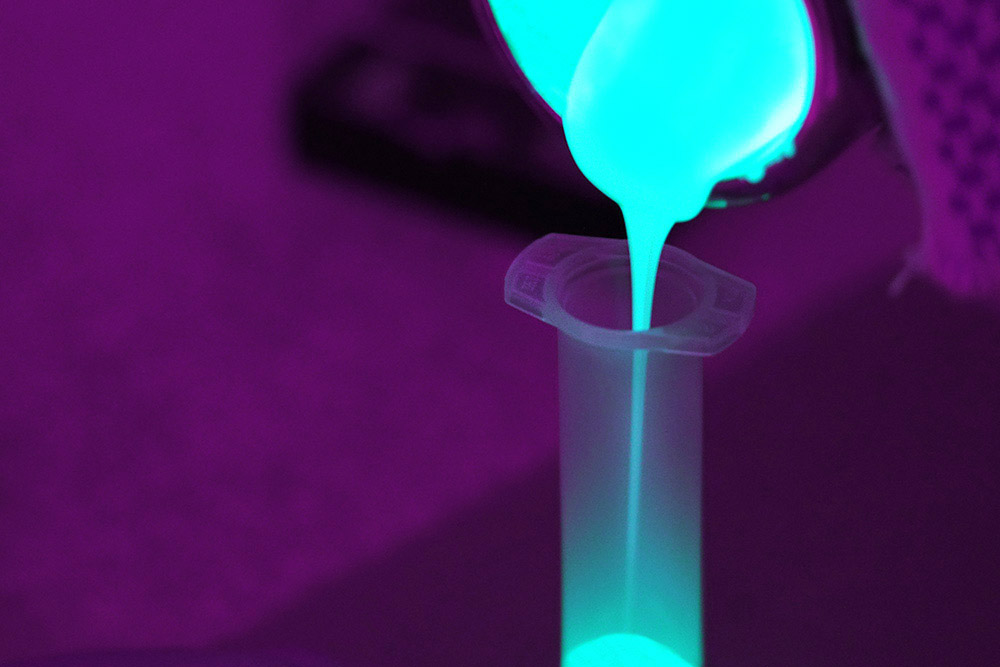
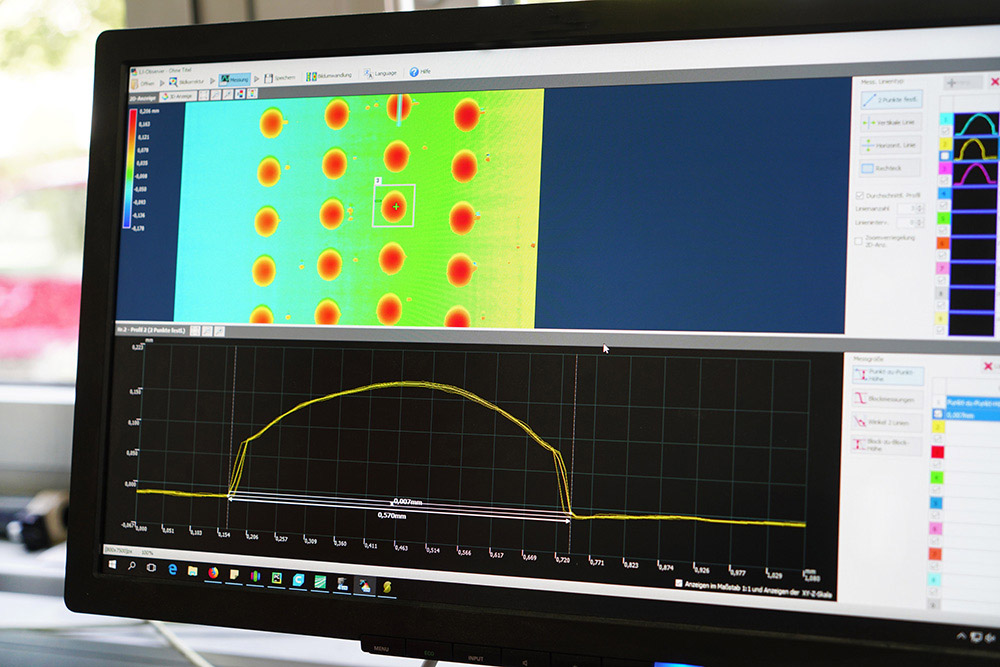
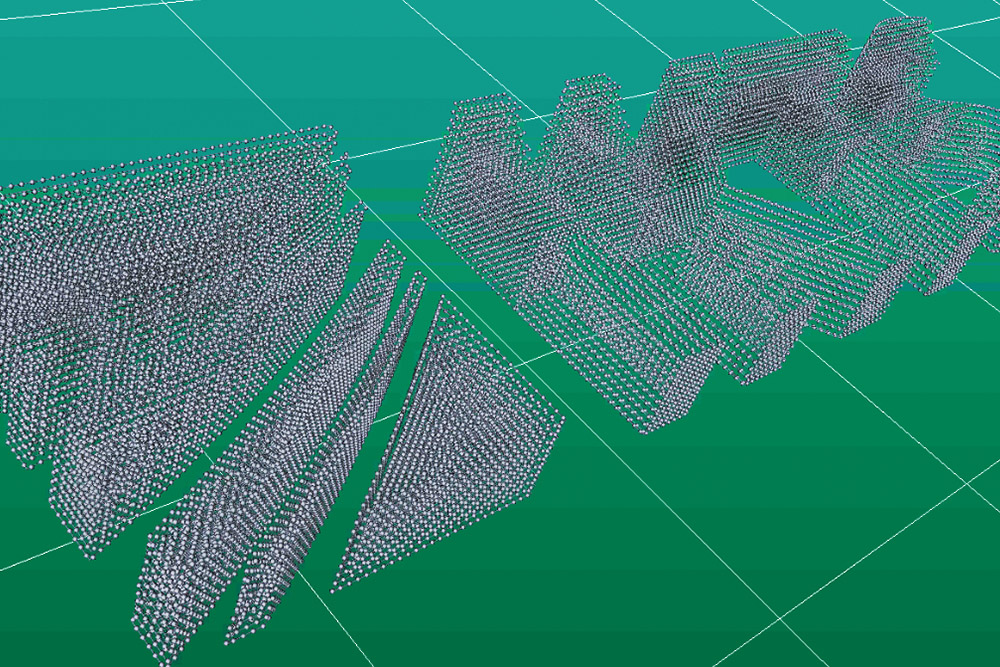
Additive Fertigung von Multifunktions-Bauteilen mittels MMJ
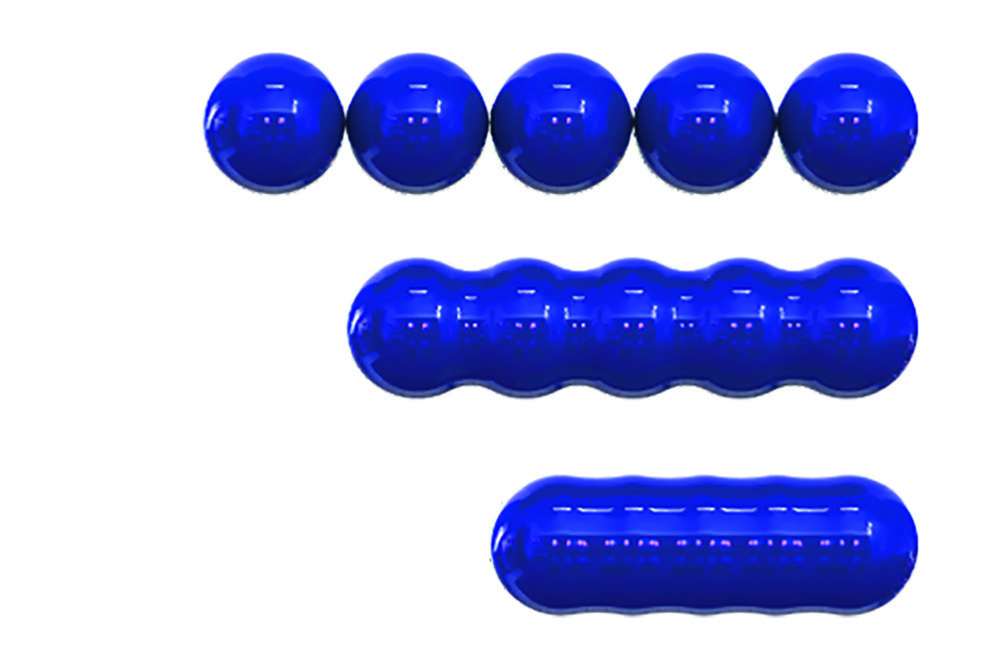
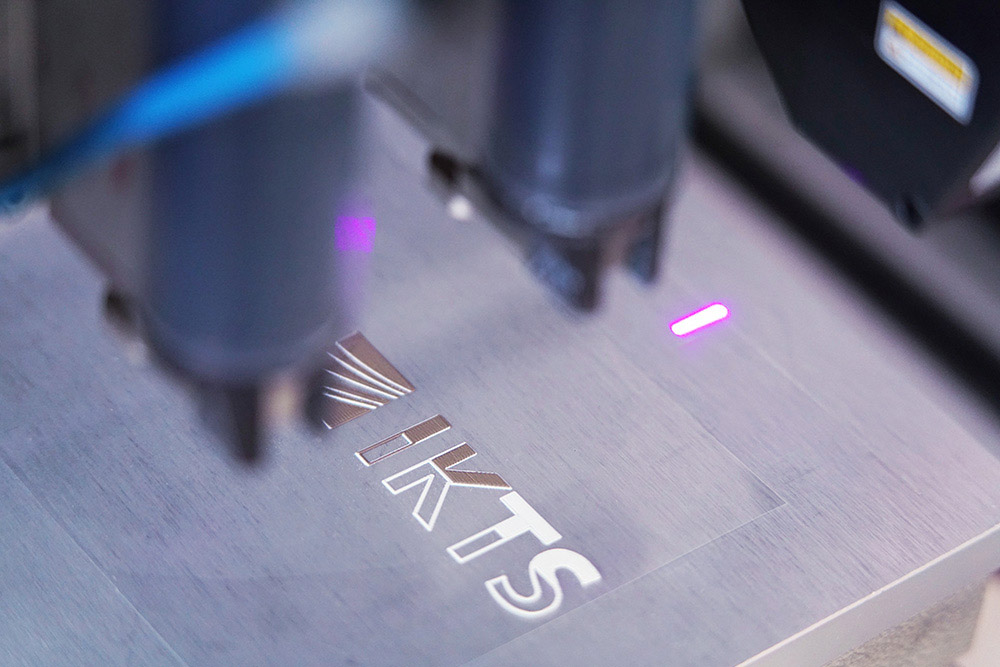
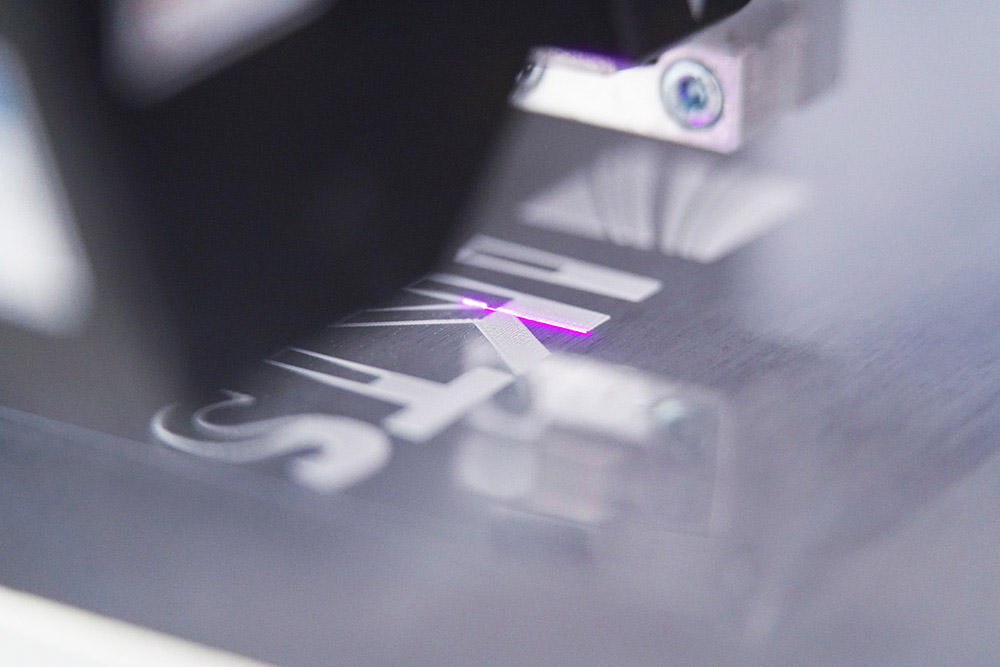
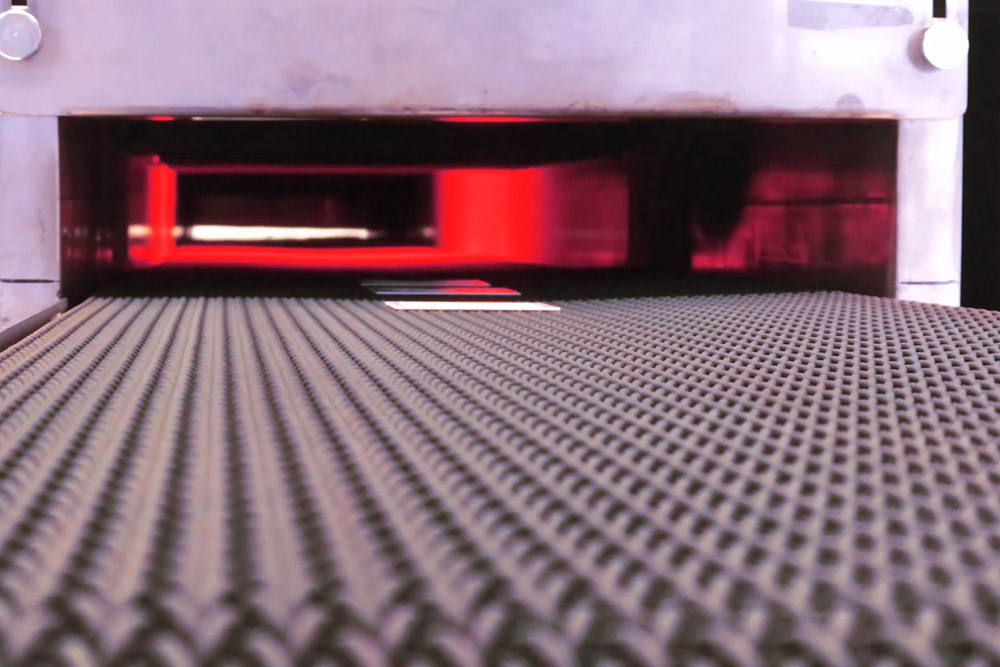
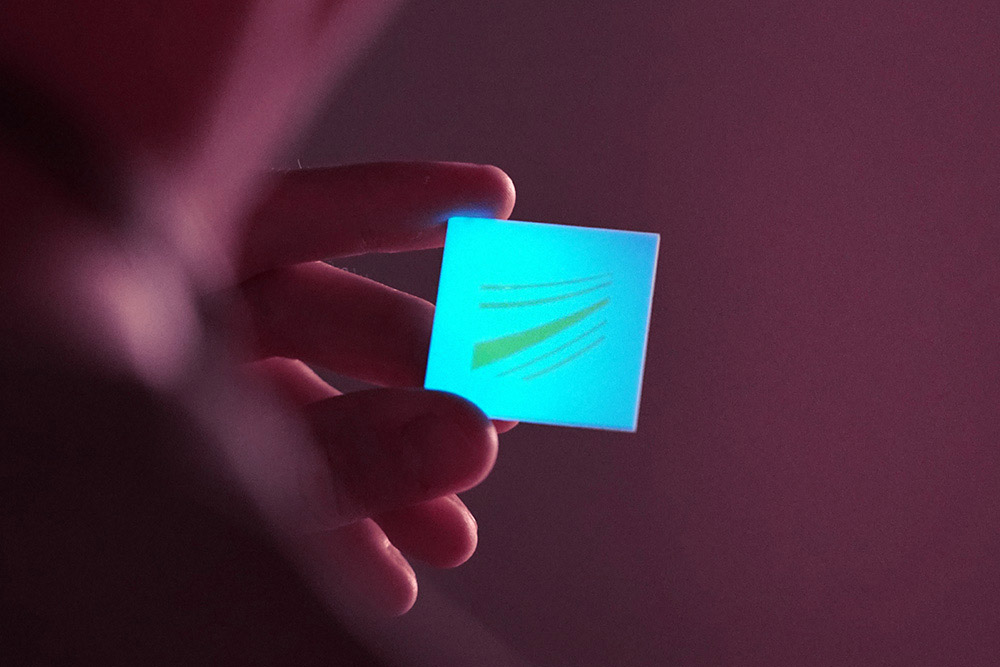
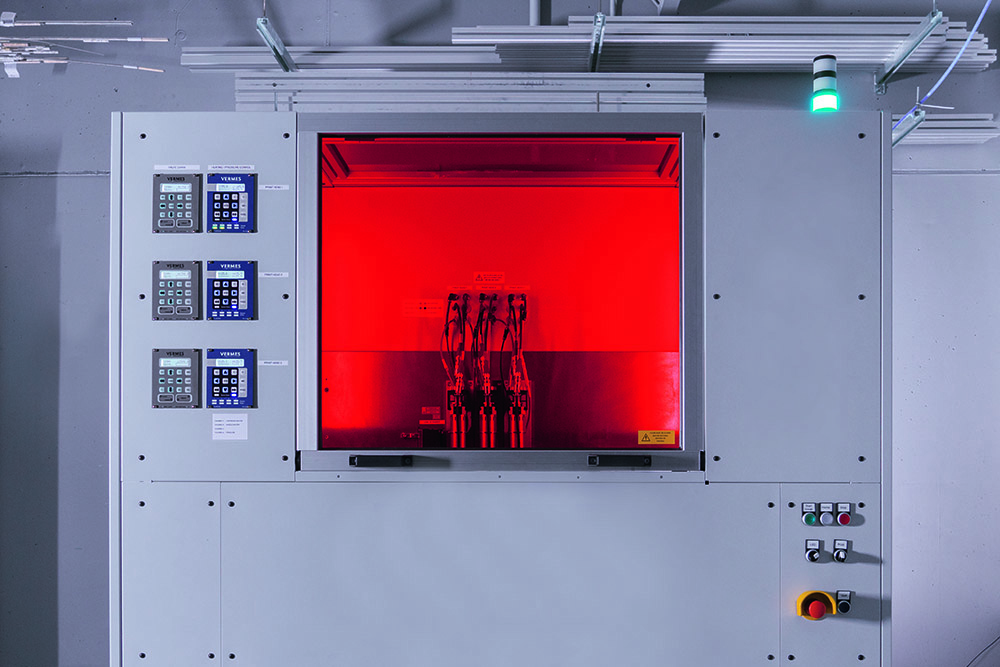
Weitere Informationen
- IKTS-Gruppe »Software für Prüfsysteme«
- IKTS-Gruppe »Systemverfahrenstechnik«
- IKTS-Gruppe »Pulver- und Suspensionscharakterisierung«
- IKTS-Gruppe »Validierung«
- Blogbeitrag »Badbasierte Photopolymerisation (VPP): Mit blauem Licht zu hochkomplexen Strukturen«
- Blogbeitrag »Additive Fertigung mit Keramik, Hartmetall und Glas«
Bleiben Sie informiert: Melden Sie sich gern für unseren Newsletter an, lesen Sie in weitere Blogbeiträge rein oder folgen Sie uns auf LinkedIn, Instagram und YouTube. Wir freuen uns, mit Ihnen ins Gespräch zu kommen.