Autorin: Andrea Gaal
Batteriefertigung – wo können wir besser werden?
Sicherlich haben auch Sie sich schon gefragt, ob Batterien für die E-Mobilität auch wirklich sicher sind; vor allem, wenn sie sich in Ihrem eigenen Auto befinden. Um die Qualitätssicherung zukünftig schneller und effizienter durchzuführen, entwickeln wir Röntgen- und Thermographiesysteme mit denen einzelne Batteriekomponenten bereits während der Herstellung geprüft werden können.
Mit Batteriezellen ist in Fahrzeugen eine Technologie integriert, die aus vielen Schichten sehr dünner Funktionselemente besteht. Diese sind verschiedensten Belastungen durch unsere Umwelt und Infrastruktur ausgesetzt – dazu zählen Stöße, Schwingungen, Feuchtigkeit oder Temperaturwechsel. Um eine sichere Funktion der Batterie zu gewährleisten, müssen produktionsbedingte Beschädigungen der Funktionselemente ausgeschlossen werden. Voraussetzung dafür ist, dass zu verschiedenen Zeitpunkten im Herstellungsprozess geprüft wird.
Herstellung der Batteriekomponenten
Eine Batterie ist schichtartig aus mehreren Batteriezellen zusammengesetzt. Jede Batteriezelle besteht dabei aus Anode, Kathode und einer Trennschicht, dem Separator. Die Grundstoffe für die einzelnen Schichten werden zu Pasten verarbeitet und auf Trägerfolien aufgetragen. Diese werden anschließend gewalzt und getrocknet, ehe sie zu Stapeln, den Batteriezellen zusammengefügt werden.
Prüfung bereits während der Herstellung
Bisher werden die Batteriezellen hauptsächlich am Ende des Herstellungsprozesses geprüft. Das heißt, die fertige Batterie wird auf Dichtheit und elektrische Performance getestet.
Da die Herstellung der Batteriekomponenten recht ressourcen- und energieintensiv ist, lohnt es sich, möglichst frühzeitig im Fertigungsprozess zu prüfen. So können defekte Teile bereits vor der weiteren Bearbeitung gefunden und aussortiert werden.
Hier setzen wir ein: Unsere Idee ist es, die Einzelteile der Batterie – speziell die Batteriefolien – bereits während der Herstellung auf Defekte zu prüfen. Mit der zerstörungsfreien Bauteilprüfung können grundsätzlich alle hergestellten Komponenten einer Serie geprüft werden; nicht nur Stichproben. Dies erhöht die Produktsicherheit.
Röntgen- und Thermographieverfahren prüfen zerstörungsfrei
Die Röntgentechnik und die Thermographie arbeiten sehr schnell, berührungslos und können relativ problemlos in den Herstellungsprozess der Batteriefolien integriert werden. Erste Versuche zeigen, dass beide Verfahren das Potenzial haben, eine Vielzahl von Fehlern und Inhomogenitäten sicher zu detektieren. Derzeit untersuchen wir, welche Defekte sich jeweils in welcher Qualität nachweisen lassen und welche Aussagen für die Bewertung des Prozesses relevant sind.
Obwohl beide Verfahren sehr ähnlich arbeiten und auch ähnliche Ergebnisbilder liefern, weisen sie verschiedene Defekte nach (siehe Bilder). Es zeichnet sich jedoch ab, dass die Ergebnisse jedes Verfahrens für sich genommen nicht aussagekräftigt genug sind. Hier wird eine Überlagerung der Bilder (Datenfusion) aus beiden Verfahren weitere Erkenntnisse bringen.
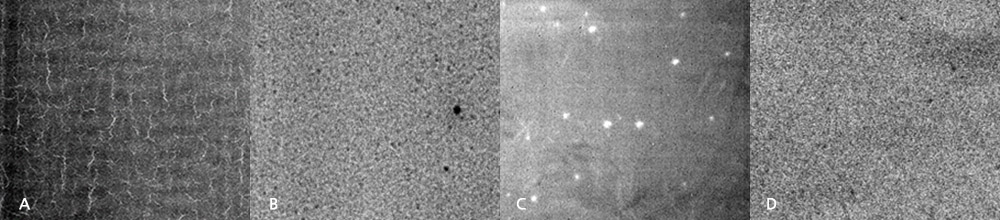
Konzepte zur Integration in den Trocknungskanal
Aktuell arbeitet unser Projektteam intensiv daran, beide Verfahren für die Prüfung von Batteriefolien zu optimieren, für die Inlineprüfung zu qualifizieren und Auswertealgorithmen zu entwickeln. Erste Prototypen der Mess-Stationen werden aufgebaut und sind bereits verfügbar. Neben umfangreichen Messungen und Auswertungen stehen die Demonstratoren auch externen Interessenten zur Verfügung.
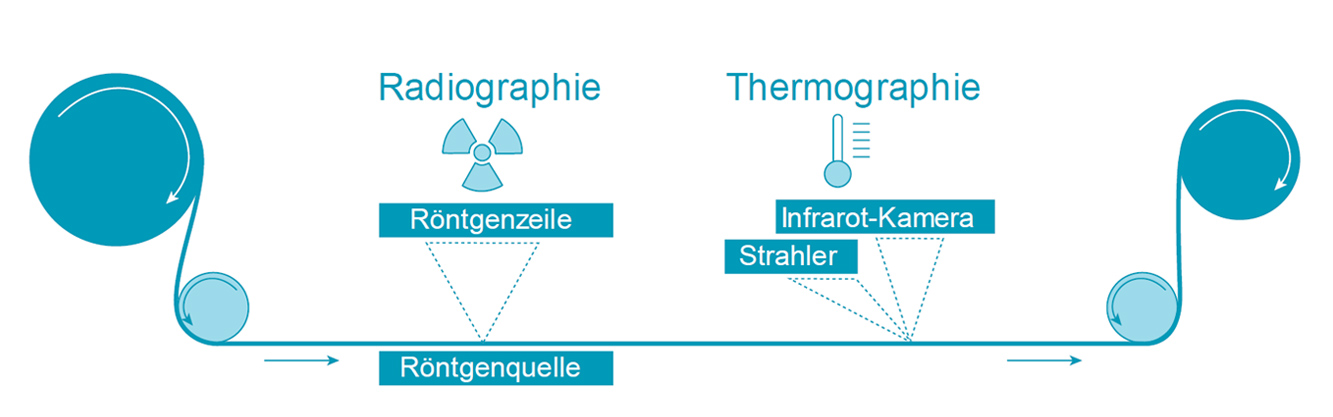
Weitere Anwendungsmöglichkeiten der Röntgentechnik
Neben der Prüfung der Batteriefolien im Herstellungsprozess bietet sich die Röntgentomographie für weitere interessante Einsatzmöglichkeiten an. So lassen sich beispielsweise Batterien zerstörungsfrei prüfen, die bereits aus ihren Einzelkomponenten zusammengefügt sind. Bei dieser abschließenden Prüfung lässt sich feststellen, ob alle Einzelteile defektfrei sind und korrekt verbunden wurden.
Auch wenn die Batterie schließlich ausgetauscht werden muss, kann die Röntgentomographie eingesetzt werden. Eine sogenannte Post-Mortem-Analyse liefert wichtige Erkenntnisse zum Alterungs- und Defektverhalten der Batterie. Diese Ergebnisse können dann für die Optimierung der eingesetzten Materialien und Komponenten verwendet werden.
Weiterführende Informationen
- Arbeitsgruppe »Elektrodenentwicklung«
- Prüftechnik für Batteriezellen
- Entwicklung von Lithium-Festkörperbatterien
- Fraunhofer-Projektzentrum für Energiespeicher und Systeme ZESS
- Fraunhofer-Technologiezentrum Hochleistungsmaterialien THM
- Batterie-Innovations- und Technologie-Center BITC
Bleiben Sie informiert: Melden Sie sich gern für unseren Newsletter an, lesen Sie in weitere Blogbeiträge rein oder folgen Sie uns auf LinkedIn, Instagram und YouTube. Wir freuen uns, mit Ihnen ins Gespräch zu kommen.