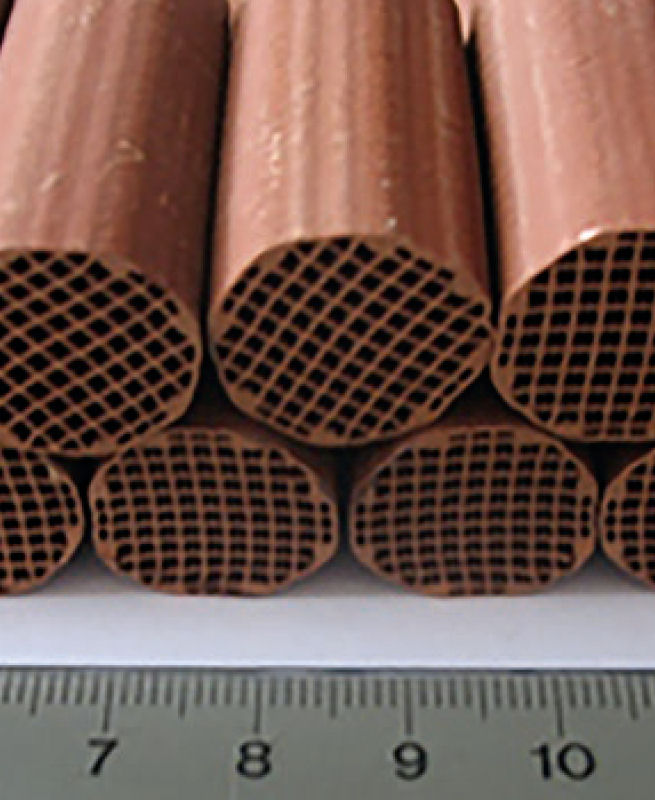
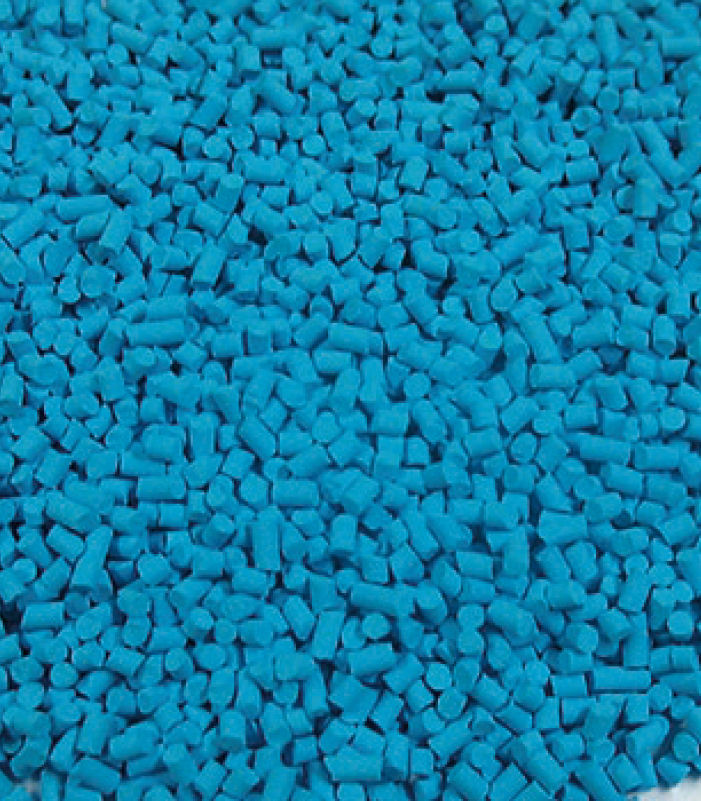
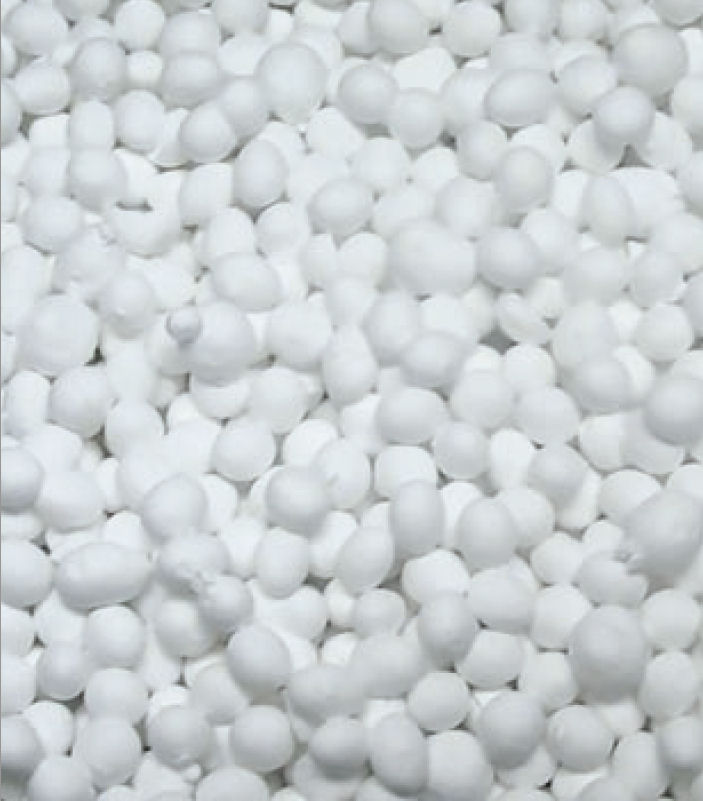
Metallorganische Gerüstverbindungen (Metal-Organic Frameworks, MOFs) sind eine neue Klasse poröser Materialien, die sich durch sehr hohe spezifische Oberflächen und Porenvolumina auszeichnen und dadurch unter anderem herausragende Gasspeichereigenschaften besitzen. Die dreidimensionalen MOF-Netzwerke bestehen aus metallischen Clustern und organischen Brückenmolekülen. In den entstehenden Zwischenräumen können andere Moleküle »gespeichert« werden. Über die Auswahl der Ausgangsmaterialien kann die Zusammensetzung und Struktur der MOFs vielfältig variiert werden, was eine anwendungsspezifische Eigenschaftseinstellung ermöglicht. Die Verarbeitung von MOF-Pulvern zu Formkörpern unterschiedlicher Größe und Geometrie ist entscheidend, wenn es darum geht, deren exzellente Materialeigenschaften einer breiten Anwendung zugänglich zu machen. Am Fraunhofer IKTS ist es gelungen, mittels pulvertechnologischer Formgebungs- und Granulierverfahren wie Extrusion, Trockenpressen, Gefrierguss und -granulation sowie Gefrierschäumung MOF-Formkörper in Form von Pellets, Granulaten oder monolithischen Waben- und Schaumstrukturen herzustellen. Diese können beispielweise in Speichersystemen für Gase, in Wärmepumpen oder als Katalysatorträger genutzt werden. Das IKTS bringt seine Kompetenzen zur pulvertechnologischen Formgebung von MOFs seit 2012 erfolgreich in entsprechende Projekte ein (u. a. Fraunhofer-internes Projekt »MOF2market«, EU-Projekt »MATESA« [Grant Agreement 608534]). In den EU-Projekten »ProDIA« (Grant Agreement 685727) und »H-CCAT« (Grant Agreement 720996) sowie dem BMBF-Projekt »MOFSchutz« (Förderkennzeichen 13N14194) werden aktuell der Einfluss der Verfahrensparameter und der Binderzusammensetzung auf die spezifische Oberfläche und die Anwendungseigenschaften der MOF-Formkörper (z. B. für NH3-Adsorption, CH4-Speicherung, H2O-Adsorption) untersucht und die Fertigungsverfahren daraufhin angepasst. Die von Projektpartnern synthetisierten MOF-Pulver, wie HKUST-1, Fe-BTC, Al-Fumarat, UiO-66, CPO-27(Ni), CAU-10 oder PCN-250 wurden zu Granulaten, Pellets oder monolithischen Formkörpern verarbeitet. Neben der mechanischen Stabilität bestand eine weitere Herausforderung darin, die originären Eigenschaften der MOF-Materialien im Formkörper möglichst vollständig zu erhalten – denn der Einsatz von Bindern und die bei der Formgebung (Extrusion, Pressen) auftretenden Scherkräfte können die Porosität bzw. die spezifische Oberfläche der MOFs und damit deren Anwendungseigenschaften (z. B. Speicherfähigkeit) negativ beeinflussen. Besonders gute Ergebnisse wurden bei extrudierten HKUST-1-Pellets erzielt, die je nach Prozessführung und Binderart spezifische Oberflächen zwischen 83 und 100 % des Ausgangsmaterials (1460 m²/g) besaßen. Für PCN-250 wurden Werte zwischen 72 und 77 % erreicht. Weitere mittels Trockenpressen, Gefriergranulierung, Gefrierguss und -schäumung erzeugte MOF-Formkörper verfügten über spezifische Oberflächen zwischen 55 und 95 % des Ausgangsmaterials. Mithilfe der angepassten Formgebungsverfahren und Formkörperzusammensetzungen ist es nun möglich, MOFs mit ihren exzellenten Materialeigenschaften für verschiedenste Anwendungen nutzbar zu machen.