Autorin: Maria Kaminski
#diensttalk mit Sebastian Stark über die virtuelle Optimierung von Piezo-Systemlösungen
Piezo-Systemlösungen eignen sich für eine Vielzahl von sensorischen Anwendungen im Bereich der Medizintechnik, der Ultraschallerzeugung oder aber auch bei der zerstörungsfreien Werkstoffprüfung. Der Herstellungsprozess ist komplex und kann bei ungeeigneter Bauteilauslegung oder Fehlern in der Polungsprozessführung zu einer Zerstörung des Bauteils führen. Aus diesem Grund ist das Fraunhofer IKTS auf verschiedene Prototyping-Verfahren spezialisiert: Der Vorteil: Zeit- und Ressourcenaufwand werden durch computergestützte Methoden auf ein Minimum reduziert, bei gleichzeitiger Optimierung der Produkteigenschaften.
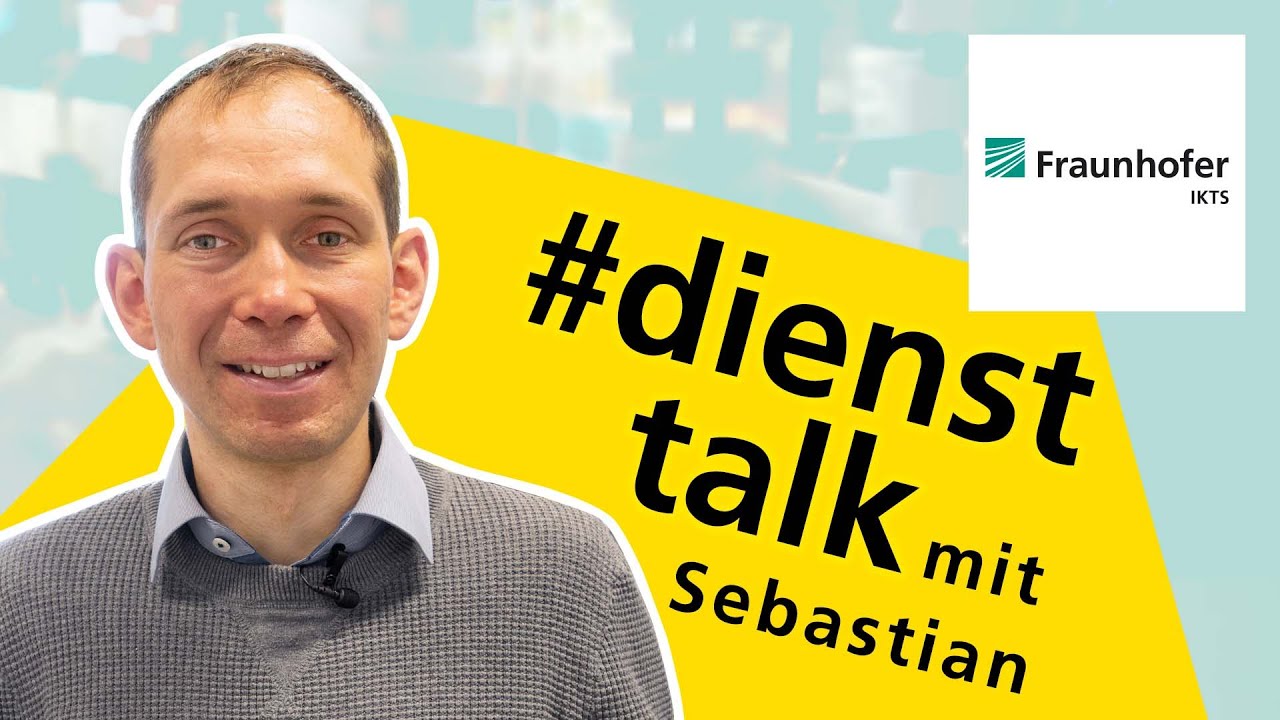
Datenschutz und Datenverarbeitung
Wir setzen zum Einbinden von Videos den Anbieter YouTube ein. Wie die meisten Websites verwendet YouTube Cookies, um Informationen über die Besucher ihrer Internetseite zu sammeln. Wenn Sie das Video starten, könnte dies Datenverarbeitungsvorgänge auslösen. Darauf haben wir keinen Einfluss. Weitere Informationen über Datenschutz bei YouTube finden Sie in deren Datenschutzerklärung unter: https://policies.google.com/privacyDer #diensttalk mit Sebastian Stark: Beim #diensttalk geben Mitarbeitende einen kleinen Einblick hinter die Kulissen des Fraunhofer IKTS und verraten, was sie bei ihrer Forschung antreibt.
Immer informiert: Melden Sie sich gerne für unseren Newsletter an, lesen Sie in weitere Blogbeiträge rein oder folgen Sie uns auf Facebook, Instagram, LinkedIn, YouTube und Twitter. Wir freuen uns, mit Ihnen ins Gespräch zu kommen.
Jeder hat es schon einmal benutzt: Ein Feuerzeug. Was die wenigsten wissen, dass in vielen Feuerzeugen der Zündfunke durch ein sogenanntes piezoelektrisches Material erzeugt wird. Durch die Druck-Belastung des Piezoelements kommt es zu einer Verschiebung von elektrischen Ladungen und damit zur Funkenbildung. Bekannt ist dieses Phänomen auch unter dem Namen piezoelektrischer Effekt, welcher sich in einer Vielzahl weiterer Anwendungen wiederfindet. So dient er u. a. der Ultraschallerzeugung in der Medizintechnik, der Reinigung verschmutzter Komponenten, wird bei der zerstörungsfreien Werkstoffprüfung und auch bei der Kraftstoffeinspritzung in Verbrennungsmotoren eingesetzt.
Neben diesen klassischen Anwendungen kommen stetig neue Einsatzgebiete hinzu: So wird beispielsweise intensiv daran geforscht, Piezo-Elemente in der Abwasserbehandlung und -analyse einzusetzen, um chemische Reaktionen zu beschleunigen. Die Erschließung neuer Anwendungsgebiete erfordert die Entwicklung von komplexen Designs, um den Anforderungen gerecht zu werden.
Dr. Sebastian Stark leitet die Gruppe Angewandte Werkstoffmechanik und Festkörperwandler. Sein Arbeitsort: Das Fraunhofer IKTS in Dresden. Seine Vision: eine prototypenfreie, vollständig virtuelle Auslegung von Piezo-Systemen. Wir haben nachgefragt, wie er seine Vision am Fraunhofer IKTS realisieren möchte.
Wie werden piezoelektrische Elemente hergestellt?
Bei der Formgebung piezoelektrischer Keramiken kommen verschiedene Verfahren, wie das Pressen, das Foliengießen oder die Dickschichttechnik zum Einsatz. Nach dem anschließenden Sintern erfolgt der sogenannte Polungsprozess. Bei diesem wird durch das Anlegen eines hohen elektrischen Feldes eine Vorzugsrichtung in das Material eingebracht, sodass die auf mikroskopischer Ebene vorhandene Verkopplung elektrischer und mechanischer Eigenschaften auch auf Bauteilebene zum Tragen kommt. Durch die Polung werden die piezoelektrischen Eigenschaften des Bauteils bestimmt. Während des Polungsprozesses treten komplexe, stark nichtlineare Effekte auf, die bei ungeeigneter Bauteilauslegung oder Polungsprozessführung zu einer Zerstörung des Bauteils führen können. Aus diesem Grund ist zur optimalen Auslegung und Herstellung von piezoelektrischen keramischen Bauteilen und Baugruppen in der Praxis häufig ein zeit- und kostenintensiver iterativer Trial-and-Error-Prozess erforderlich. Mit computergestützten Verfahren kann dieser Prozess deutlich effizienter gestaltet werden, z. B. mit der Finite-Elemente-Methode (FEM). Diese kann den Polungsprozess simulieren und die resultierenden piezoelektrischen Eigenschaften des Bauteils vorhersagen, indem die den Polungsprozess beschreibenden kontinuumsmechanischen Gleichungen numerisch gelöst werden. Dazu wird die zu berechnende Komponente in eine Vielzahl kleinerer, geometrisch einfacher Elemente (z. B. Tetraeder) zerlegt. Innerhalb dieser kann die Lösung für die interessierenden Größen durch einfache mathematische Funktionen näherungsweise beschrieben werden. Durch Kombination der Lösungen der einzelnen »finiten« Elemente ergibt sich schließlich eine Näherungslösung für das Gesamtproblem. Der große Vorteil der FEM gegenüber anderen Verfahren besteht darin, dass insbesondere komplex geformte Bauteile berechnet werden können.
Wie läuft der simulationsgestützte Auslegungsprozess ab?
Ausgangspunkt für die simulationsgestützte Auslegung ist typischerweise ein parametrisches CAD-Modell der Komponente. Durch Variation von geometrischen Parametern und eingesetzten Materialien ergibt sich eine Vielzahl möglicher Realisierungen der Komponente. Dabei ist von vornherein nicht offensichtlich, welche der Realisierungen für den vorgesehenen Einsatzzweck hinsichtlich Funktion und Kosten am besten geeignet sind. Daher wird der Polungsprozess mithilfe der beschriebenen Methode für diese Realisierungen simuliert. Die Ergebnisse werden nach vordefinierten Kriterien, wie dem Ausmaß der elektromechanischen Kopplung bewertet. Basierend darauf wird schließlich die optimale Lösung ausgewählt.
Was sind die Vorteile der Finite-Elemente-Methode (FEM)?
Beim klassischen iterativen Vorgehen wird eine Vielzahl von Prototypen hergestellt und umfangreich getestet. Mit der FEM-Methode kann dagegen das Verhalten der Prototypen beim Polungsvorgang sowie die daraus resultierenden piezoelektrischen Eigenschaften virtuell umgesetzt und untersucht werden. Zudem können mehr Parameterkombinationen und komplexere Geometrien betrachtet werden. Damit können die Anzahl nötiger Prototypen, Entwicklungszeiten und -kosten drastisch reduziert werden, was wiederum Ressourcen schont.
Das Herzstück der Simulationsmethodik ist das zugrundeliegende Materialmodell des piezokeramischen Werkstoffs. Dieses beschreibt das Werkstoffverhalten mathematisch und bildet die Basis für die FEM-Simulationen. Im Materialmodell treten eine Reihe von Materialparametern auf, die experimentell identifiziert werden müssen. Sowohl die Entwicklung der Materialmodelle als auch die Materialparameteridentifikation stellen wesentliche Kompetenzen des Fraunhofer IKTS dar. Die Materialmodelle werden unter Verwendung moderner Programmiersprachen und -umgebungen implementiert und an kommerzielle Finite-Elemente-Software-Pakete wie ANSYS oder Comsol angebunden. Mithilfe dieser erfolgen die beschriebenen Simulationen auf Komponentenebene, wobei die dafür erforderlichen Materialparameter an verschiedenen, teils eigens dafür entwickelten Versuchsständen bestimmt werden.
Wofür kann die Simulationsmethode angewendet werden?
Ein Beispiel für die Anwendung stellt die Polung von piezoelektrischen Fasern in Active-Fibre-Kompositen dar, welche entweder als Sensoren oder Aktoren zur Zustandsüberwachung und -beeinflussung von Strukturen verwendet werden. Um die notwendige Polung der Fasern in Längsrichtung zu ermöglichen, werden Kerbelektroden zur Realisierung der erforderlichen elektrischen Felder verwendet. Die Simulationsmethodik kann in diesem Zusammenhang die ideale Kerbelektrodentiefe bestimmen. Zusätzliche Experimente sind damit nicht mehr erforderlich. Darüber hinaus sind weitere Parameterstudien hinsichtlich der Form des Kerbgrundes realisierbar, um die nach dem Polungsprozess vorhandene elektromechanische Kopplung des Active-Fibre-Komposits weiter zu erhöhen.
Was wünschen Sie sich für die Zukunft?
Mein Hauptziel für die Zukunft besteht darin, den Zeit- und Ressourcenaufwand durch die Entwicklung computergestützter Methoden auf ein Minimum zu reduzieren und gleichzeitig die Produkteigenschaften zu optimieren. Vor allem die bestehenden Materialmodelle für piezoelektrische Keramiken sowie die zugehörigen Experimente zur Material-parameteridentifikation müssen weiter ausgebaut werden. Dies betrifft die Erhöhung der Vorhersagegüte der Modelle sowie die Übertragung auf neue, teils bleifreie Materialien, wie auch die Reduktion des Aufwandes für die Materialparameteridentifikation. Ein weiterer vielversprechender Ansatz ist die Kopplung der Simulationsmethode an mathematische Formoptimierungsverfahren, welche die Möglichkeiten bieten, die Bauteilform im Hinblick auf die Optimierung bestimmter Eigenschaften automatisch anzupassen.
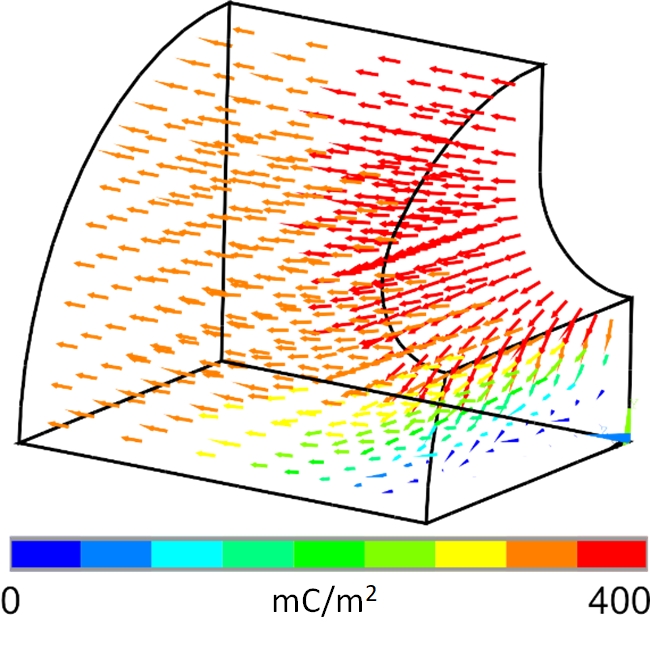
Hier geht's zu weiteren #diensttalks. Blicken Sie hinter die Kulissen des Fraunhofer IKTS.
Bleiben Sie darüber hinaus informiert: Melden Sie sich gern für unseren Newsletter an, lesen Sie in weitere Blogbeiträge rein oder folgen Sie uns auf LinkedIn, Instagram und YouTube. Wir freuen uns, mit Ihnen ins Gespräch zu kommen.