Membrane Technology Application Center: Customized membrane testing for industrial and mining waters
Used correctly, modern membrane technologies can treat polluted industrial wastewater better than classical treatment technologies alone can. Our Membrane Technology Application Center in Schmalkalden operates at the interface between science and industry. Fraunhofer IKTS operates more than 20 laboratory and pilot plants on an area of around 370 m², which have been specially designed for specific application scenarios. Here, new membrane prototypes are characterized, effective cleaning strategies are developed, and feasibility studies and field tests are carried out for industrial customers and research partners.
Technology intermediary between science and industry
„Our work at the Membrane Technology Application Center is very application-oriented. We see ourselves as technology mediators for state-of-the-art membrane technologies into industry," emphasizes environmental scientist Christian Pflieger. The Application Center of Fraunhofer IKTS covers the entire spectrum of classical and advanced membrane technologies. These include, on the one hand, polymer membranes, which today dominate the world market for membranes because they are inexpensive, easy to shape, and inexpensive to produce. On the other hand, the Application Center focuses on membranes made of oxide and non-oxide ceramics such as Al2O3, ZrO2, TiO2 or SiC. Compared to polymer membranes, they are better able to withstand high temperatures and pressures, aggressive or hot media, and abrasive materials in the process water, which makes them attractive for many applications. With well-coordinated cleaning processes and robust ceramic membranes, it has been shown in customer-specific laboratory and field tests, for example, that dyeing water from the textile industry, washing water from textile cleaning or rinsing water from the ceramics industry can be purified to such an extent that they can be fed back into the factory cycle as service water. If pilot tests are successful, as in these cases, the researchers then develop concepts for integrating these effective membrane processes into the customer-specific process. In the process, the IKTS team led by Christian Pflieger not only determines the optimum operating parameters such as temperature, pressure and overflow speed, but also looks at how the membranes can be cleaned again later in the process.
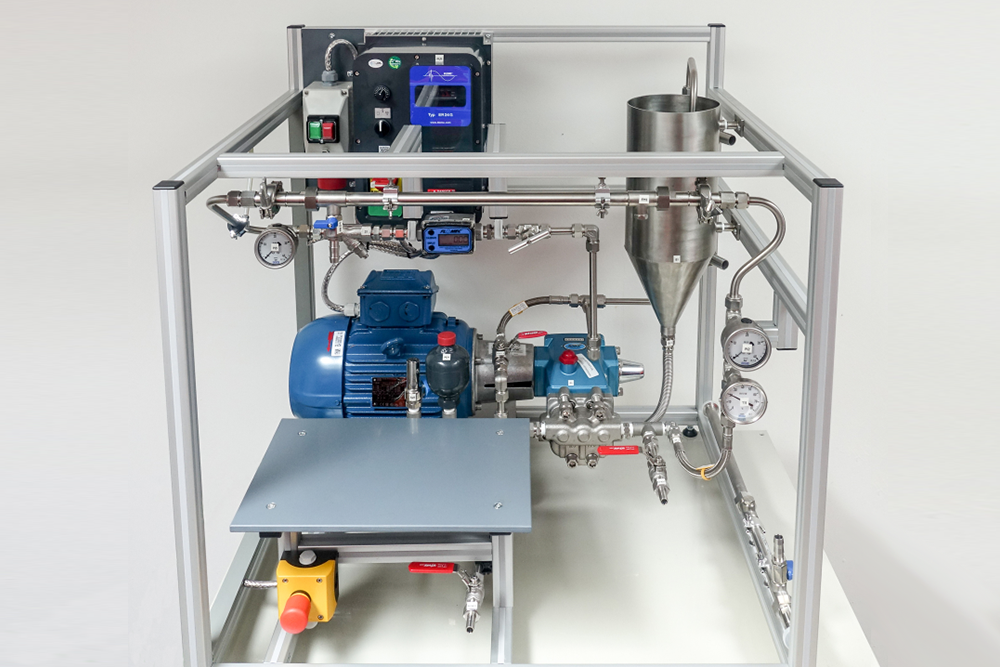
Bringing young membrane processes to market
The Membrane Technology Application Center also develops technologies that have rarely been used to date: If, for example, silver or zinc are washed out of old mining dumps, the so-called membrane extraction can be used to recover heavy metals as raw materials. The relatively new membrane distillation process can be used, for example, to remove high salt loads from wastewater from the dairy industry. Steam pressure driven membrane distillation can bring a saline liquid close to the limit of crystallization of the dissolved salt by constant water removal. This highly saline liquid is then either further processed or disposed of. The advantage is that the water separated up to this point can be reused. For this process, the researchers are not only developing the optimum process control, but also special ceramic membranes with a water-repellent coating.
Ceramic membranes are becoming increasingly affordable
Despite the numerous advantages offered by ceramic membranes, they are often not used today for cost reasons. Nevertheless, in view of the high technological potential, several companies in Japan and Germany are striving to noticeably reduce the manufacturing costs of ceramic membranes. Also, the Membrane Technology Application Center is aiming at a broader and less expensive application. The IKTS team's approaches focus on increasing the active membrane area by developing ever larger multichannel elements. This can significantly increase the achievable wastewater throughput. Early membrane elements had an effective membrane area of 0.25 m²; this value has now been increased to 4.5 m². Tests are currently underway with prototypes with a membrane area of up to 10 m². The larger the membrane area of an element, the lower the manufacturing costs in comparison, which should lead to a further increase in market acceptance for ceramic membranes. The technological challenges lie in the more complex shaping of the ceramic substrate and its uniform coating with the various membrane layers. This also changes the requirements for the membrane housing. This is another focus of the Application Center. Matched to the respective membrane geometry, the IKTS employees design the appropriate membrane housing for installation in the specific wastewater treatment plant.
Further information
- IKTS Group "Membrane process technology and modeling"
Stay informed: You are welcome to subscribe to our newsletter, read our other blog articles and follow us on LinkedIn, Instagram and YouTube.