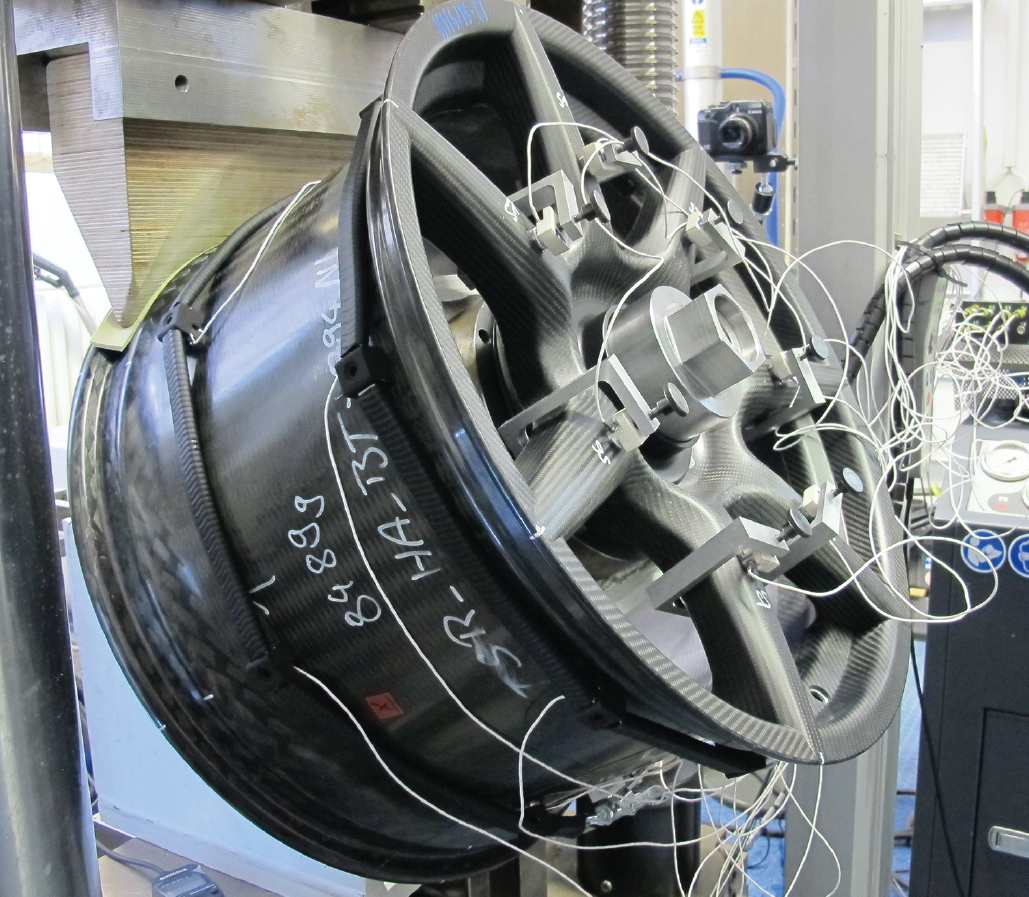
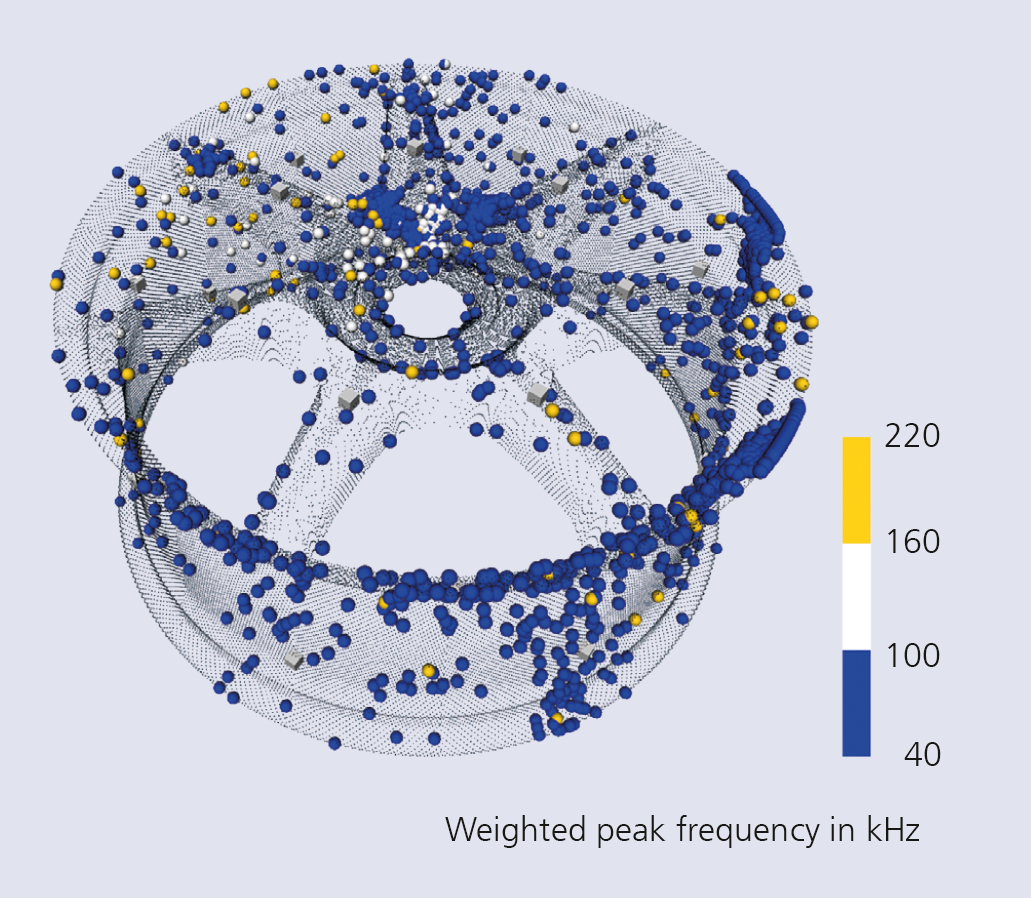
Fiber-reinforced plastics (FRP) have become an indispensable part of modern vehicle manufacturing. The reliability of these materials is paramount, especially when it comes to safety-relevant components. The service life of FRP components is affected by aging processes or improper use. Damages such as fissures in the matrix, delamination, or fiber breakage can lead to component failure.
Non-destructive testing using acoustic emissions
Acoustic emission testing (AT) is a non-destructive method for component testing. The principle is based on detecting acoustic signals at the surface of solids when energy is released under stress in the form of an elastic wave. Acoustic emission testing differs from conventional ultrasonic testing significantly since the acoustic emission is initiated by the actual damage within the material – the damage itself is the acoustic emission source. The results of testing on the coupon level showed clusters in the parametric space from the weighted peak frequency (WPF) and the partial sound power in a specific frequency range. This allows for the determination of the acoustic emission parameter, which provides information on the type of damage, its progress and therefore also on the structural integrity of the tested material samples. The attenuation effect needs to be taken into account when interpreting acoustic emission signals from the fatigue testing of complete components, in particular regarding to the frequency analysis. As the distance from the acoustic emission source to the acoustic sensor grows, the attenuation of high-frequency signal parts increases as well and therefore needs to be taken into account. For component testing, two different cluster areas of the WPF point to different mechanisms of damage: low-frequency acoustic events indicate matrix-dominated mechanisms of damage (events marked blue in Figure 2), while high-frequency burst signals point to fiber-dominated mechanisms of damage (events marked yellow in Figure 2).
Measurements at high ambient noise levels
The acoustic emission testing system developed at Fraunhofer IKTS allows for AT measurements using specially adapted measuring and analysis software – even under high ambient noise levels, e.g. in the case of dynamic fatigue testing. For instance, AT was able to successfully identify damages in a bending fatigue test.