New products with multi-material 3D printing
Multi-material 3D printing with technical materials has huge potential. For example, functionalized or functionally graded products can be printed within a single process in a resource-saving manner. This significantly shortens the process chain and reduces manufacturing costs compared to conventional production routes. In order to commercialize this promising technology, the developers of the multi-material jetting technology at the Fraunhofer Institute for Ceramic Technologies and Systems IKTS founded AMAREA Technology GmbH. The spin-off has been active since February of 2023. The entrepreneurs act as system developers on the market and sell both the printing technology and the newly developed printing materials. The possibilities extend beyond technical ceramics: metals, hardmetals, glasses, composites, cermets and even polymers can be processed.
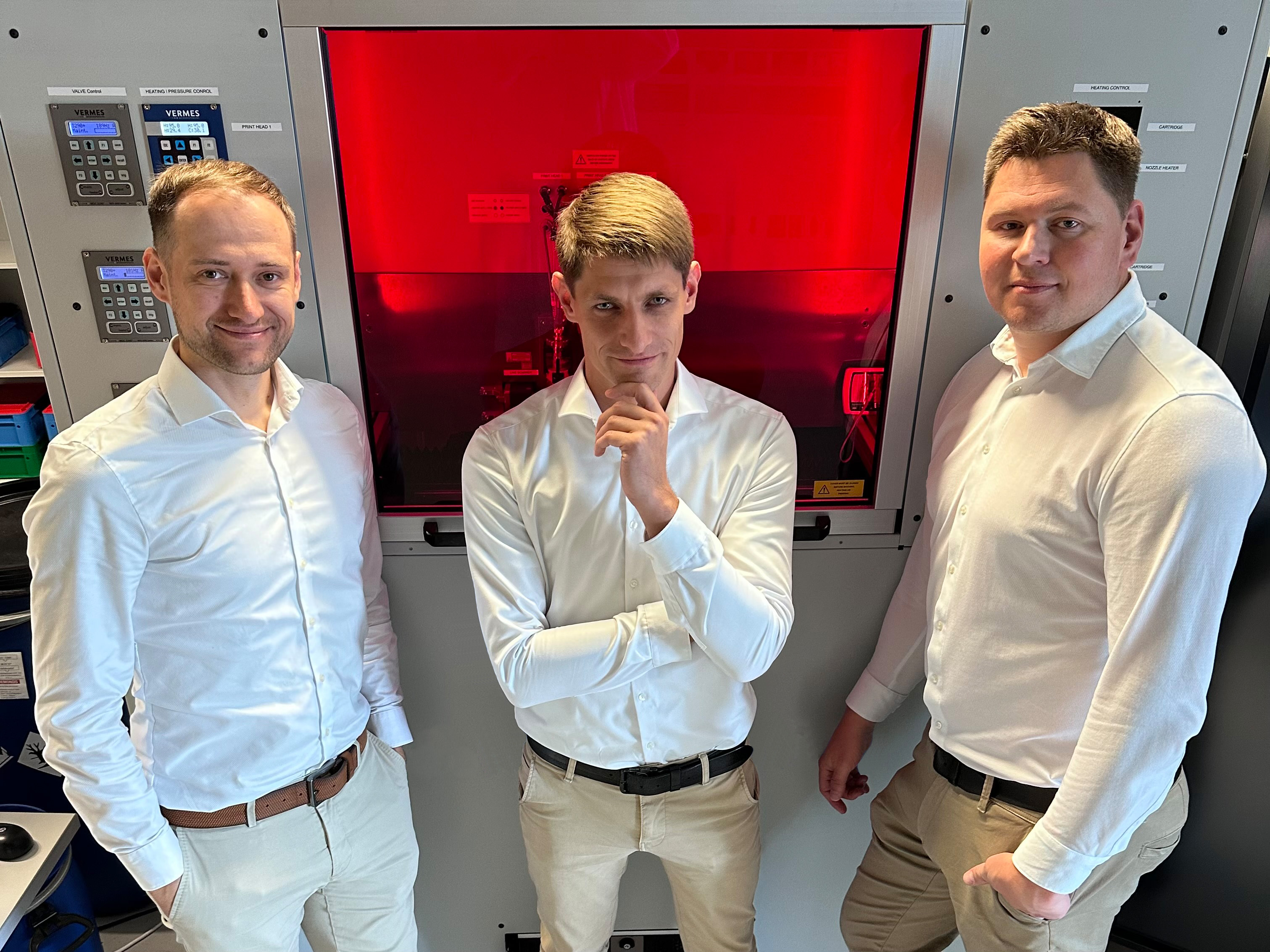
Multi-material 3D printing with high-performance materials is the next step in additive manufacturing and has been developed at IKTS since 2014. During this time, a wealth of knowledge and experience has been acquired. The potential of the multi-material jetting (MMJ) technology has already been successfully demonstrated with convincing prototypes and a wide range of industrial customers. Therefore, Steven Weingarten, Lutz Gollmer, Philipp Horn and Robert Johne founded AMAREA Technology GmbH, based in Dresden, in February 2023. As of now, they want to commercialize MMJ and transfer the 3D printers to series production. They are supported by Fraunhofer IKTS and the German Federal Ministry for Economic Affairs and Climate Protection BMWK as part of the EXIST research transfer funding program.
Key component: printing materials
The development and sale of high-tech 3D printers is – along with printing materials and service – one of the three business areas. In the latest generation of systems, up to six print heads can be installed. This means that up to six different materials can also be combined at the same time. These must be coordinated with each other – the many years of IKTS know-how in the field of material development come into play here. In recent years, more than 15 materials and material combinations have thus been qualified for MMJ technology. AMAREA Technology GmbH benefits precisely from this expertise. Thus, the spin-off can offer its customers a technology which manufactures multi-material components in a single print job – starting with the selection and development of the printing material up to the component design. IKTS and AMAREA Technology will continue to work closely together in the future and further advance the multi-material topic.
Multi-material 3D printing for functionalized and graded components
The great advantages of additive manufacturing lie in the rapid realization of innovative ideas, design freedom and extensive geometry independence. The diversity of materials in multi-material 3D printing means that there are now even fewer limits to creativity. Materials with defined properties can be produced and combined via multi-material printing, such as electrically conductive and electrically insulating, dense and porous, hard and ductile, multicolored or even magnetic and non-magnetic. In this way, functionalized components, or entire assemblies, for example with integrated sensors or actuators, can be printed within a single process – and without any cross-contamination of the individual materials. By gradually combining materials within a layer and from layer to layer with defined properties, the 3D printer is also able to create functionally graded transitions, for example porosity, within a component.
Tremendous application potential
Multi-material 3D printing opens up the opportunity for manufacturers to tailor products to user needs even better than before. By shortening the process chain, it is also possible to significantly reduce production times and costs, expand product diversity, and manufacture more powerful and robust components or assemblies. AMAREA Technology's target groups are developers and manufacturers of components made of high-performance materials from a wide range of industries such as electronics and semiconductor technology, special toolmaking, automotive technology and its supply chains, the jewelry and watchmaking industries, aerospace, medical technology and energy technology. But prototype construction and research institutions can also benefit from the advantages of multi-material 3D printing.
Laser module eliminates extensive post-processing of printed components
The new 3D printer generation is scheduled for market launch in mid-2024. The modular system concept offers the possibility to design the 3D printer according to customer specifications. With up to six print heads, and thus up to six different materials, the 3D printer currently achieves component accuracies of 70 to 100 µm. For inline process control, up to two profile sensors can be integrated to automate process parameterization and, in the future, to geometrically measure the components during the printing process. With the upcoming optional laser module, which removes material, polishes or structures the surfaces during 3D printing, surface finishes of less than 1 µm can be achieved. This eliminates the need for time-consuming post-processing of components. Manufacturers can thus further optimize their production in terms of time and costs. Other AI methods for quality assurance will also contribute to this in the future, such as defect detection and automatic adjustment of process parameters during the printing process.
Increasing productivity through intelligent route planning
Depending on the component size and geometry, the success of additive manufacturing also depends on productivity, i.e. how fast a component can be printed. Currently, the speed is 8 to 12 cm3/h per print head. The target with the new generation of 3D printers is to achieve at least double this speed via intelligent route planning. This means that the specially developed software determines the optimal route for material application per shift. This not only saves time, but also energy.
Innovators can meet AMAREA Technology at Formnext in Frankfurt, Germany, November 7-10, 2023, in Hall 12.1, Booth 121-B39A, to learn more about multi-material 3D printing.