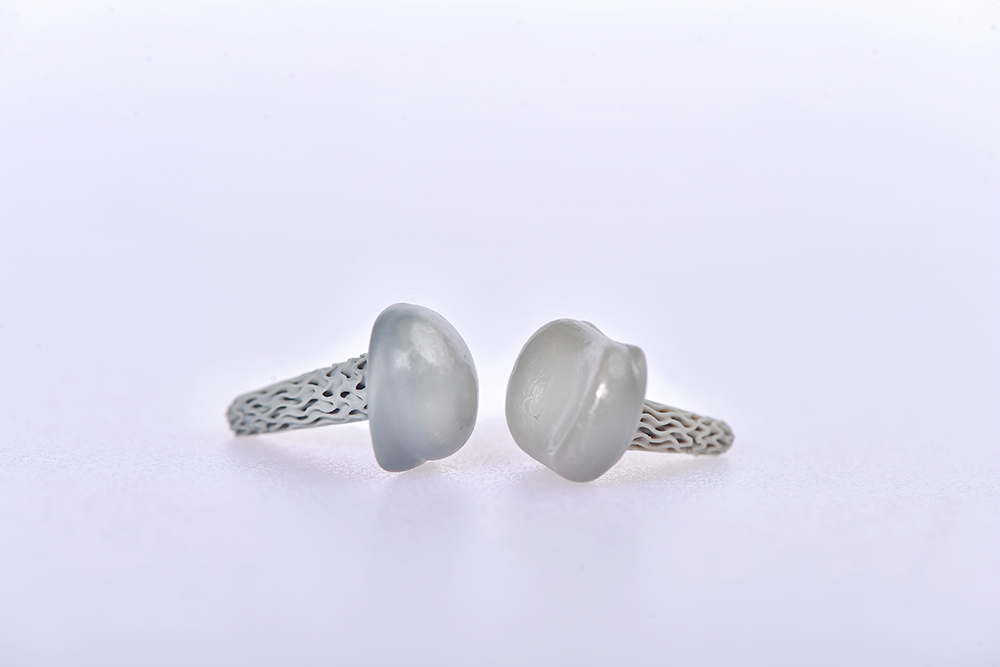
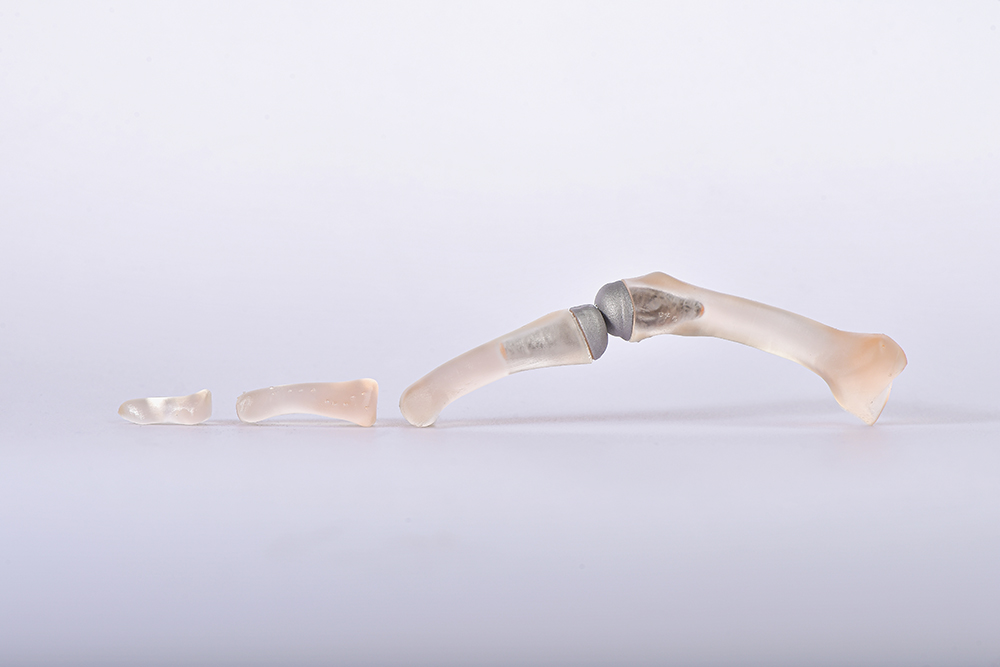
The tailored treatment of patients with a view to a long and active life is closely linked to the individualization of implants. Criteria such as the greatest possible accuracy of fit for the individual bone, custom-made products in facial surgery and even cases in which the bone substance no longer permits a standard revision implant, lead to solutions for patient-specific implants and instruments in combination with individual 3D surgical planning.
Ceramic materials for excellent strength and high biocompatibility
The technical possibilities of 3D printing are perpetuating visions of patient-specific implants on the market. The solutions on offer are mostly based on titanium or PEEK. However, the additive manufacturing of ceramic implants, with the exception of oxide dental implants, is still largely in its infancy. In addition to excellent mechanical properties and high wear resistance, ceramics are also highly biocompatible. Due to the abrasion that occurs with metallic implants, they are considered to be better tolerated. New studies have shown that silicon nitride, for example, has an antibacterial effect thanks to its unique surface chemistry and is therefore considered particularly promising alongside the established aluminum oxide-reinforced zirconium oxide (ATZ).
3D printing for patient-specific finger joint implants
Individualized implants are a great source of hope, especially in the area of small joints, where there are hardly any standard implants and fusion is the standard therapy. This is because joint fusion restricts the patient's freedom of movement, which leads to a major loss of quality of life. As part of the "FingerKIt" research project, we worked with our Fraunhofer partners to research the remobilization of finger joints and develop ceramic solutions. Using additive processes, patient-specific finger joint implants can be manufactured from silicon nitride. For this purpose, we use high-resolution 3D printing technologies such as DLP-based Vat photopolymerization. This allows filigree structures and structuring to be implemented with a high degree of precision. The prerequisite for this is the silicon nitride suspensions developed at Fraunhofer IKTS, which make printing the biocompatible silicon nitride quality possible in the first place.
Fraunhofer IKTS covers the entire technology chain for the production of silicon nitride ceramics, from powder preparation to hot isostatic post-compaction for the highest requirements and safety.
Services offered
- Development of silicon nitride materials adapted to mechanical strength, osseointegration and implant design
- 3D printing of finger joint implants in biocompatible silicon nitride quality and optimized fit
- Hot isostatic redensification
- Standard-compliant testing of the implants