Autor: Anika Peucker
SHM: die Gesundheitsprüfung für Leichtbauautos
Haben Sie schon mal von »kohlenstofffaserverstärktem Kunststoff, kurz CFK« gehört? Erinnern Sie sich an Ihre letzte Flugreise? Im Tragwerk von Flugzeugen, z. B. im Flügel, werden Faserverbundwerkstoffe seit längerem verbaut. Denn solche Materialien sind leichter als Metall. Sie sparen Gewicht. Der Kerosinverbrauch wird reduziert.
CFK – ein zukunftsträchtiger Werkstoff
Falls sie CFK noch nicht kennen: Bei diesem Werkstoff handelt es sich um einen Verbund aus Kohlenstofffasern und einer sogenannten Matrix. Die Matrix hält die Fasern zusammen und stabilisiert sie. Hergestellt werden die Verbundwerkstoffe beispielsweise per RTM-Injektionsverfahren. RTM steht für Resign Transfer Moulding und ist eine Harzinjektion. Im ersten Schritt wird dabei eine Preform gefertigt. Preforms sind vorgeformte Werkstücke aus ungetränkten Faserlagen. Solch eine Preform wird in ein zweiteiliges Injektionswerkzeug, ähnlicher einer Presse, eingespannt, das Werkzeug geschlossen und Harz injiziert. Das Harz durchtränkt die Fasern und muss zum Schluss aushärten.
Als zweiten Prozess zur Herstellung von CFK-Komponenten gibt es das Faserwickeln. Beim Wickeln werden mittels eines automatisierten Werkzeugs bereits imprägnierte Endlosfasern auf einen drehenden Kern abgelegt. Anschließend werden die Fasern ebenfalls ausgehärtet.
Während der Herstellung der CFK-Bauteile können außerdem Elektronikkomponenten, wie Sensoren und Leiterbahnen, in die Struktur eingebracht werden. Die elektronischen Komponenten verbinden sich beim Aushärten des Harzes direkt mit dem Gewebe, was als Co-Bonding bezeichnet wird. Nach dem Aushärten erhält man Bauteile, die zusätzliche Funktionen übernehmen. Sie sind »intelligent«. Ein solches »intelligentes« CFK-Bauteil kann anschließend als Tragstruktur in einem Fahrzeug verbaut werden. Typische gewickelte CFK-Komponenten sind z. B. Drucktanks in Erdgasfahrzeugen. Wasserstoffspeichertanks für Brennstoffzellenfahrzeuge, wie sie im Zuge neuer Antriebskonzepte entwickelt werden, sind ebenfalls gewickelte, funktionalisierte CFK-Komponenten. Die »intelligenten« Bauteile können aber auch metallische Bauteile versteifen. Der Fachbegriff hierfür heißt Hybridstruktur. Eine Motorhaube kann beispielsweise eine solche Hybridstruktur sein.
CarbonSafe
»Motorhaube« fragen Sie sich jetzt vielleicht? Wir sprachen doch eingangs von der Luftfahrt. Ja: Motorhaube. Denn auch die Automobilindustrie tendiert dazu, mehr und mehr CFK-Strukturen in Fahrzeuge zu integrieren. Bereits heute werden einige Fahrzeuge, beispielsweise der BMW i3 oder der VW XL1, großteils aus Verbundwerkstoffen gefertigt. Branchenkenner gehen davon aus, dass der Leichtbauanteil innerhalb der nächsten elf Jahre auf bis zu 70 Prozent steigen wird. Die Leichtbauweises senkt bei Autos mit Verbrennungsmotor den Spritverbrauch. Bei Elektrofahrzeugen hilft CFK, das Gewicht der Batterien auszugleichen. Allerdings ist der Materialwechsel von Leichtmetall auf Kunststoffverbünde nicht trivial. CFK weist nämlich ein gänzlich anderes Schädigungsverhalten auf. Sowohl durch plötzliche Stoßbelastungen, z. B. einen Auffahrunfall, als auch in der Bauteilherstellung können Schäden wie Matrix- oder Faserbrüche auftreten. Solche Defekte zeigen sich häufig zwischen den Faserlagen. Sie erkennen sie meist nicht auf den ersten Blick. Vergleichen können Sie es mit einer Art inneren Verletzung. Diese entdeckt Ihr Arzt auch nur durch spezielle Tests, indem er in den Körper hineinschaut. So verhält es sich auch beim Auto.
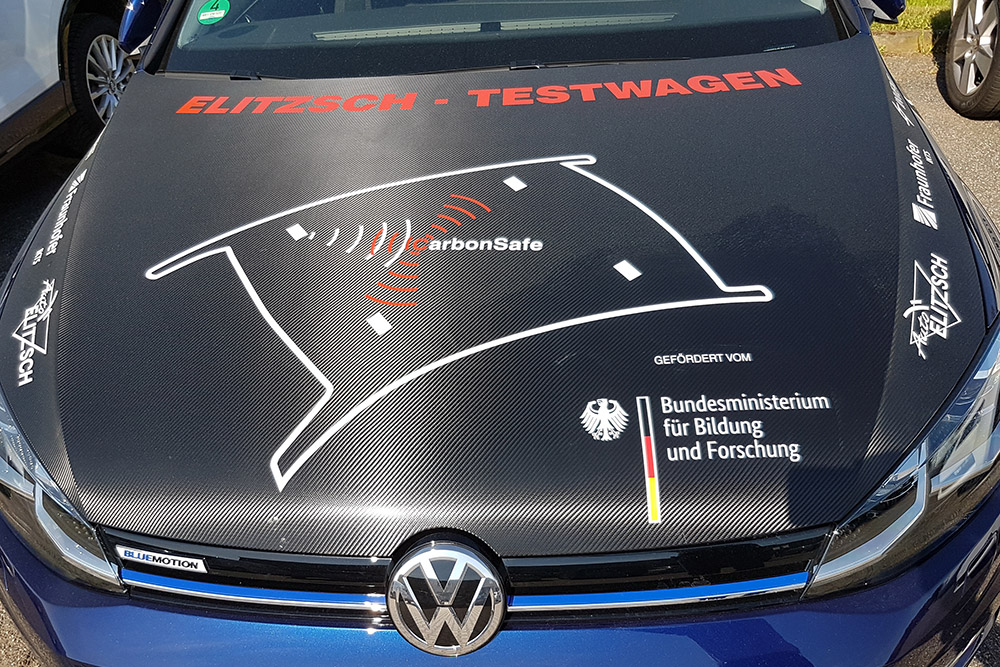
Wie finden wir nun die »innere Verletzung« sicherheitsrelevanter Autobauteile? Zum Auffinden verborgener Fehler entwickelten die Physiker und Ingenieure des Fraunhofer IKTS gemeinsam mit der Industrie ein sensorgestütztes, zerstörungsfreies Prüfsystem, das auf einem Structural Health Monitoring (SHM)-Verfahren mit aktiv geführten Ultraschallwellen beruht. Das Verfahren wurde so konzipiert, dass es einerseits bereits zur Qualitätssicherung der Bauteile während ihrer Produktion eingesetzt werden kann. Andererseits lässt es sich ebenso in Autowerkstätten im Rahmen der Wartungsintervalle schnell und zuverlässig anwenden.
Wie funktioniert Structural Health Monitoring?
Die im Bauteil integrierten piezoelektrischen Sensoren bilden ein gemeinsames Netzwerk. Sie sind in der Lage, Ultraschallwellen zu senden und aus verschiedenen Richtungen zu empfangen. Woher wissen die Forschenden aber, wo sie die einzelnen Sensoren platzieren müssen? Sie bedienen sich zuvor umfangreicher Simulationen der Wellenausbreitung in dem jeweiligen Bauteil. Damit legen sie das Sensornetz optimal aus. Ein solches Sensornetz kann während der Fertigung in ein CFK-Bauteil eingebracht werden. Oder aber es wird nachträglich auf die Struktur appliziert als Prüfsystem für Werkstätten.
Die piezoelektrischen Sensoren zeichnen die empfangenen Signale entweder automatisiert im Fahrbetrieb oder im Rahmen einer Wartung auf, um so Schäden in der Bauteilstruktur zu identifizieren und zugleich zu lokalisieren. Die aufgenommenen Daten werden an ein angeschlossenes Diagnosegerät geleitet, weiter verarbeitet und die Ergebnisse mit einer systemimmanenten Fehlerdatenbank verglichen. Die Analyse- und Visualisierungssoftware signalisiert dem Prüfer, ob und wo ein Defekt vorliegt. Der Mechaniker kann sich die Ergebnisse sowohl auf dem Bildschirm seines PC’s als auch per App auf seinem Tablet oder Smartphone anzeigen lassen.

Wichtig für die Ultraschallwandler ist: Sie müssen genauso lange halten wie das Bauteil, in das sie integriert wurden. Wir sprechen dabei von deutlich mehr als zehn Jahren. Gute Nachrichten: Das SHM-System bestand den ersten Praxistest. Eingebaut in eine Motorhaube absolvierte es monatelange Testfahrten. Dabei wurde es verschiedensten Belastungen und Umweltbedingungen ausgesetzt. Die Mechaniker schlossen währenddessen regelmäßig das Diagnosegerät an. Sie untersuchten dabei die CFK-Struktur nicht nur auf Schäden, sondern überprüften auch die Funktionsfähigkeit der Sensoren. Gleichzeitig unterzogen die Entwickler in ihren Labors die eingebetteten Komponenten in einer Klimakammer einer beschleunigten Alterung. Die Praxistauglichkeit des entwickelten SHM-System konnte bei den Tests bestätigt werden.
Das gesamte System lässt sich auch sehr einfach an verschiedene Anforderungen und Fahrzeugmodelle anpassen. Das Diagnosegerät, welches momentan noch nicht in das Auto integriert ist, kann perspektivisch direkt in neue Fahrzeuge eingebaut werden. Im Zusammenspiel mit den »intelligenten« CFK-Bauteilen liefert das am IKTS entwickelte SHM-System einen Beitrag dazu, die Sicherheit im Fahrzeug noch weiter zu erhöhen. Besteht Ihr Fahrzeug bereits zu einem erheblichen Teil aus Faserverbundmaterial?
Die Arbeiten wurden vom Bundesministerium für Bildung und Forschung (BMBF) im Rahmen des Schwerpunktprogramms KMU Innovativ als Förderprojekt »CarbonSafe« (Förderkennzeichen: 16ES0333) unterstützt.
Bleiben Sie informiert: Melden Sie sich gern für unseren Newsletter an, lesen Sie in weitere Blogbeiträge rein oder folgen Sie uns auf LinkedIn, Instagram und YouTube. Wir freuen uns, mit Ihnen ins Gespräch zu kommen.