Autor: Anika Peucker
Laser-Speckle-Photometrie: Inline-Fehlersuche in der Hochleistungselektronik
Stellen Sie sich eine Keramikplatte vor, oben und unten mit Kupfer beschichtet, die mit metallischen Leiterbahnen bedruckt werden kann. Dann blicken Sie auf Ihren Monitor und sehen das unten gezeigte gesprenkelte Bild. Ziemlich viele Sprenkel. Zumindest an einigen Stellen. An anderen wiederum keine. Kaum zu glauben, dass die funktionalisierte Keramikplatte mit der Aufnahme etwas gemein haben könnte. Und noch abwegiger vielleicht: Wie lesen Wissenschaftler aus solchen Bilder nur Werkstoffkennwerte und Fehler ab?
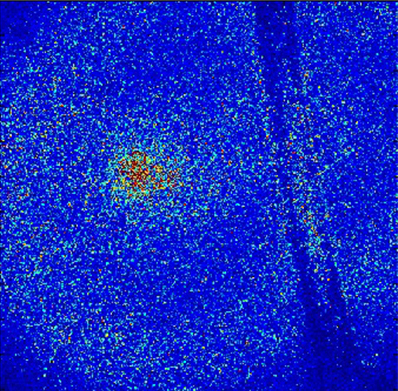
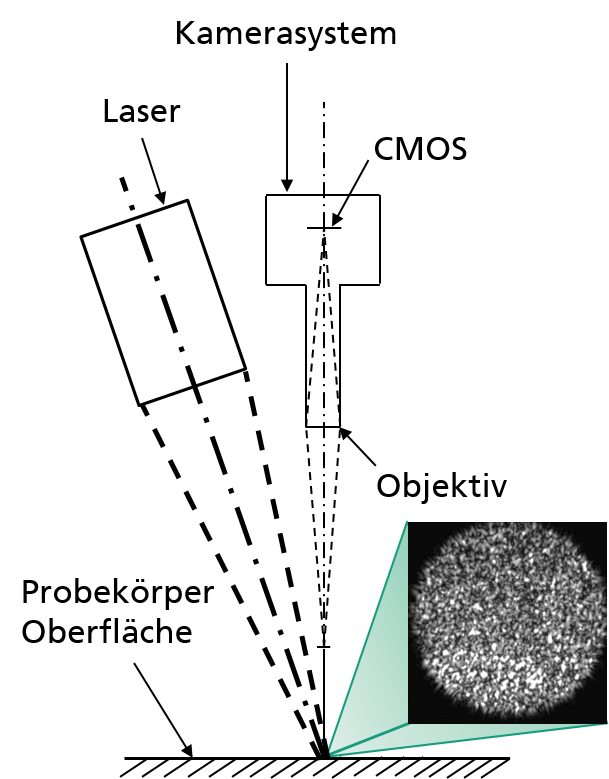
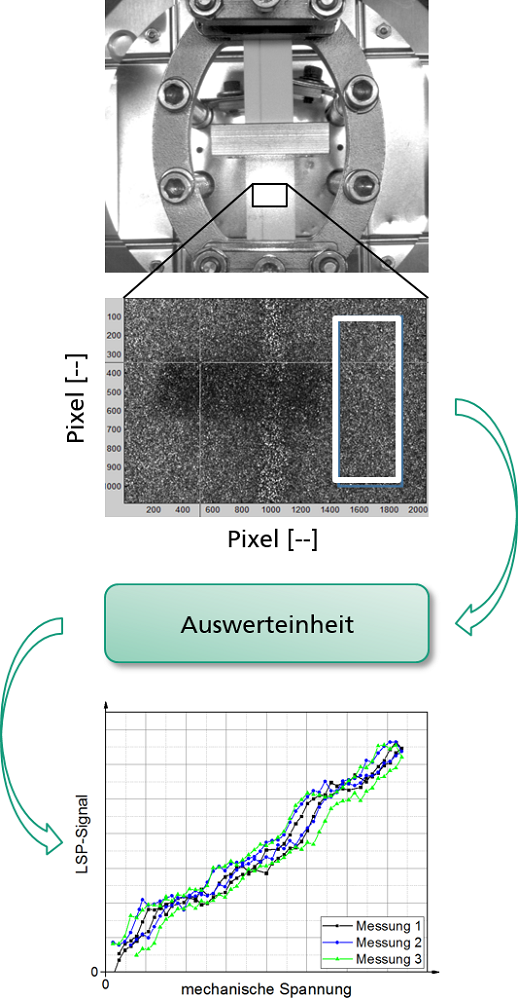
Die Entstehung von Speckle-Mustern
Doch so ähnlich könnte ein Ergebnisbild einer Leistungselektronik aussehen, die während ihrer Produktion inline – und zwar mit der Laser-Speckle-Photometrie (LSP) – überprüft wird. An stark belasteten Stellen ändert sich die Intensität des Signals. Sie leuchtet je nach Softwareeinstellung hell oder farbig kontrastreich auf und verursacht die dichten körnigen Flächen. Um solche Signale zu messen, muss in die bestehende Anlage ein einfaches, kompaktes aber robustes LSP-System eingebaut werden. Es besteht aus einer Lichtquelle, etwa einer Laserdiode, einer Kamera, den Auswertealgorithmen sowie der Steuerungs- und Regelungssoftware.
Speckle entstehen dann, wenn eine raue Oberfläche mit kohärentem Licht, beispielsweise Laserlicht, beleuchtet wird. Licht wird an der Oberfläche reflektiert. Es interferiert in der Beobachtungsebene und bildet räumliche Strukturen mit zufällig verteilten Intensitäten. Diese Intensitätsunterschiede werden mit einem CMOS-Sensor aufgezeichnet, algorithmisch verarbeitet und liefern dann eben diese speziellen Bilder. So ein Speckle-Bild zeigt uns die Oberflächeninformationen, anhand derer wir das Bauteil charakterisieren können. Wir erkennen Bauteilverformungen, die für das menschliche Auge nicht wahrnehmbar sind, und können die dadurch hervorgerufenen mechanischen Spannungen bestimmen. Kurz gesagt: Die LSP wertet die lokalen Interferenzmuster der Prüflinge aus und ermittelt daraus die Materialbelastung.
Der Vorteil der Methode liegt in den kurzen Messzeiten. Außerdem funktioniert sie völlig berührungslos, berechnet die Ergebnisse in Echtzeit und ist im Vergleich zu anderen Verfahren preiswert. Noch dazu bedient sie ein breites Anwendungsfeld. Eines davon stelle ich Ihnen vor.
Qualitätsmessung: LSP in der Leistungselektronik
Keramikbasierte Leistungselektronik finden Sie in der Automobilindustrie, in der Hochfrequenztechnik und in vielen anderen Feldern, in denen widrige Umfeldbedingungen herrschen. Denn Temperaturbeständigkeit und Stabilität zeichnen Keramiken aus, den vorherrschend harschen Bedingungen zu trotzen. Nehmen wir beispielsweise kupferbeschichtete Aluminumoxidkeramiken: Sie sind bei der Herstellung Extrembelastungen ausgesetzt. Die mechanische Bearbeitung und das Sintern stressen das Bauteil. Defekte entstehen, die während der Massenproduktion kaum auffallen. Beispielsweise platzt Kupfer ab, vorzugsweise an den Ecken. Die Keramik bricht muschelig. Selten wird alle Ausschussware bereits während der Produktion aussortiert, ausgenommen sie fällt bei der Qualitätskontrolle auf. Das Problem zeigt sich im laufenden Betrieb, nämlich dann, wenn das Teil im System verbaut ist. Pech. Zu spät. Durchs Raster gefallen. Wieder Geld und Ressourcen »verbrannt«. Das hat bei Konkurrenzdruck und sich verschärfenden Marktbedingungen keiner so recht übrig.
In dem Fall kann die LSP helfen. Das kompakte, anforderungsangepasste Prüfsystem wird in die bestehende Anlage integriert und misst während der Produktion die mechanischen Spannungen, die zu den Brüchen führen. Nachweislich! Die Ergebnisse bildet der Monitor in Echtzeit ab. So kann der Arbeiter im nächsten Schritt das kaputtgehende Bauteil gleich aussortieren oder bei Auffälligkeiten im Prozess die Maschinenparameter justieren.
Dass sich die LSP zur zerstörungsfreien Prüfung von Leistungselektronik eignet, wiesen unsere Wissenschaftler nach. Wie? Sie belasteten eine Aluminiumoxidkeramik mechanisch. Simulierten damit eben die Realbedingungen. So gewannen sie Kenntnisse über die Bruchmechanik und die Kräfte, wie die Eigenspannung, die währenddessen im Bauteil herrschen. Den Test führten die Forscher mit der dynamisch-mechanischen Analyse durch. Darin »gefangen«, setzten sie das Bauteil einer kontrolliert induzierten Belastung aus und überwachten den »Stresstest« via LSP. Im Ergebnis erhielten sie eine exzellente Übereinstimmung zwischen dem LSP-Messsignal und der applizierten Belastung. Um Unkenrufen vorzubeugen: Mögliche Einflüsse von Umfeldbedingungen, etwa Raumbeleuchtung, Belichtungszeit, Winkel- und Abstandsänderung, auf das Messergebnis widerlegten die Kollegen in einer Kontrollstudie.
Vielleicht fragen Sie sich jetzt, was an dem entwickelten Konzept so besonders ist, schließlich existiert die LSP als Prüfverfahren schon eine ganze Weile. Die Antwort: Es gibt augenblicklich kein Verfahren, dass die Stressbedingungen und Fehler in der Aufbau- und Verbindungstechnik inline abbilden kann. Schlussendlich konnte das Team um Dr. Mike Röllig und Dr. Beatrice Bendjus belegen, dass LSP für eine solche Inline-Überwachung in Produktionsprozessen von Leistungselektronik hervorragend funktioniert. Im industriellen Wettbewerb bedeutet das klar: Zeiteinsparung, Kostensenkung durch Inline-Qualitätssicherung sowie intakte Bauteile in der Kontrolle nicht zu zerstören. In zwei Worten: Nachhaltig wirtschaften.
Das optische Verfahren kann aber noch mehr. Eine integrierte LSP zur Überwachung des additiven Fertigungsprozesses beispielsweise sowie die Bestimmung, Fehleranalyse und Vermessung des Edelmetallgehaltes beim Mikro-Laserauftragsschweißen bieten Potenzial. Oder nehmen Sie biologische Prozesse: Ein vollautomatischer, nichtinvasiver Sensor, der die Biomassekonzentration und wichtige morphologische Parameter in biologischen Systemen kontrolliert, wäre ein Gewinn. Über einiges werden wir noch ausführlicher im Blog berichten. Weitere Ansätze gibt es viele. Ideen auch. Welche sind die Ihren?
Mehr zur Laser-Speckle-Photometrie
Münch, S.; Röllig, M.; Cikalova, U.; Bendjus, B.; Chen, L.; Sudip, S. (2017). A Laser Speckle Photometry based Non-Destructive Method for Measuring Stress Conditions in Direct-Copper-Bonded Ceramics for Power Electronic Application. In Institute of Electrical and Electronics Engineers –IEEE (editor) 18th International Conference on Thermal, Mechanical and Multi-Physics Simulation and Experiments in Microelectronics and Microsystems (EuroSimE), 2017, Dresden, Germany.
Bleiben Sie informiert: Melden Sie sich gern für unseren Newsletter an, lesen Sie in weitere Blogbeiträge rein oder folgen Sie uns auf LinkedIn, Instagram und YouTube. Wir freuen uns, mit Ihnen ins Gespräch zu kommen.