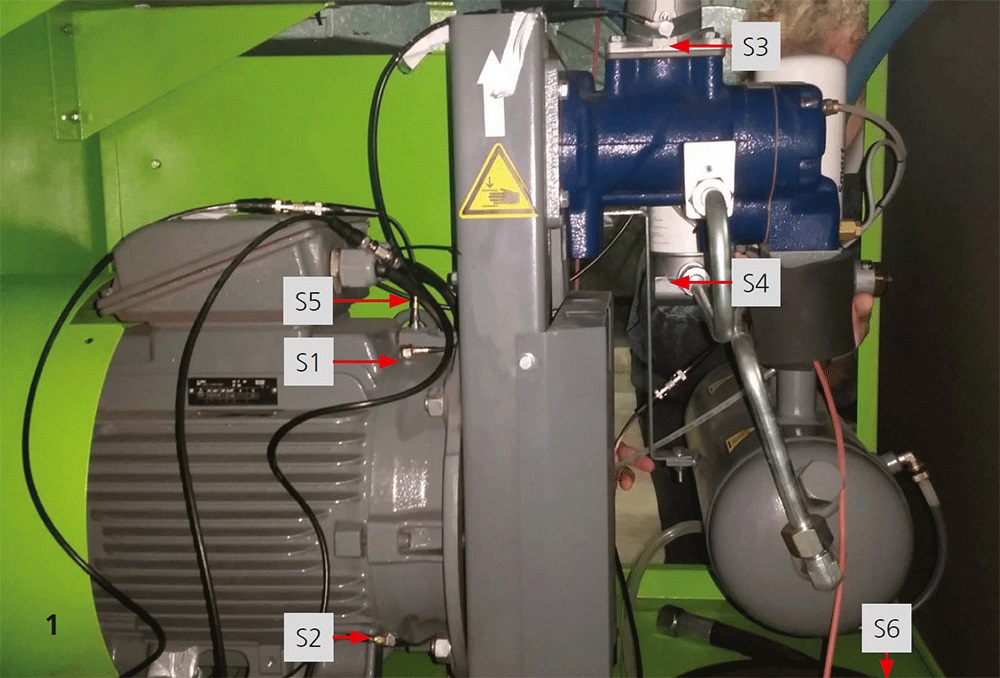
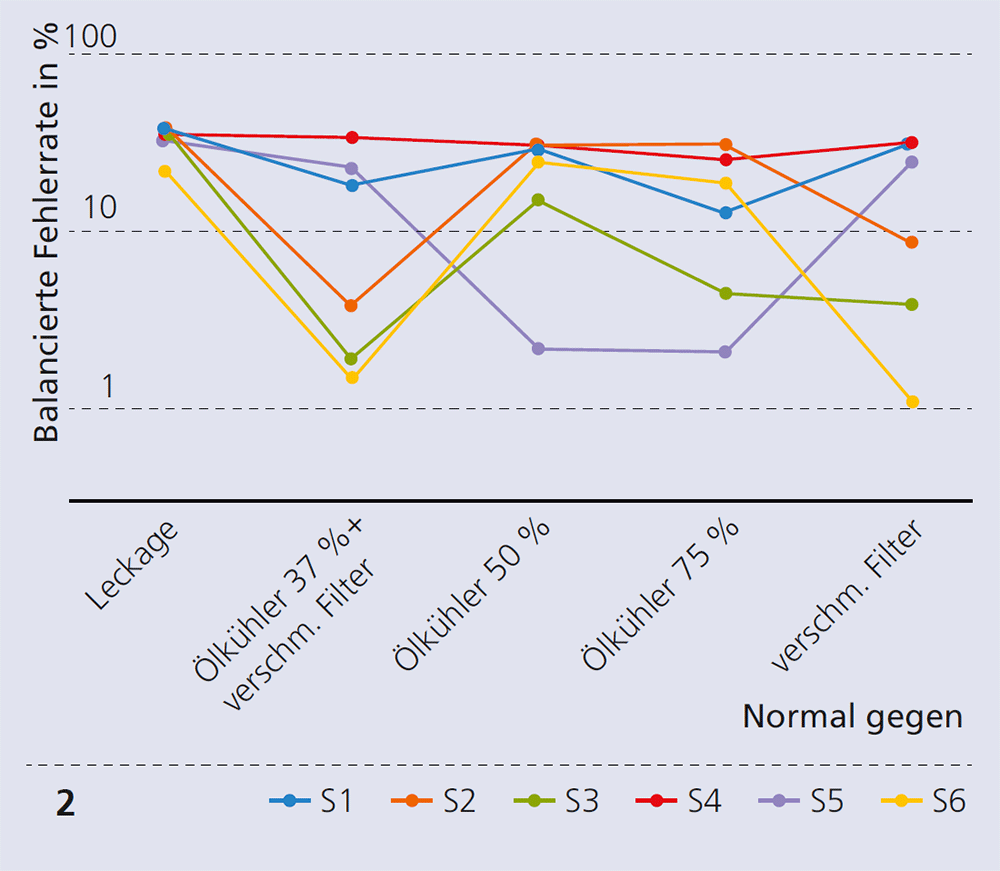
Viele Abläufe in Industrie, Verkehr und anderen Gesellschaftsbereichen setzen den stabilen Betrieb von Kompressoren voraus. Fällt ein Kompressor aus, führt das zu Stillstands- und Reparaturzeiten und damit zu einem beträchtlichen ökonomischen Schaden. Die Betriebsstabilität ist aber hinsichtlich der Instandhaltung wenig erschlossen, was einen neuen Ansatz erfordert, der verschiedene Technologien integriert.
Weniger Reparatur und Serviceaufwand, mehr Wirtschaftlichkeit und Energieeffizienz
Im Rahmen des Projekts »CompWatch« entwickeln wir gemeinsam mit den Unternehmen Petko GmbH und SONOTEC GmbH Sensoren und Verfahren, die statt fester ereignisorientierte Wartungsintervalle ermöglichen. Ziel ist die Früherkennung möglicher Ausfälle, sodass Stillstands- und Reparaturzeiten reduziert sowie unnötige Servicearbeiten vermieden werden. Das führt zu Kosteneinsparungen. Aufgrund der energetischen Relevanz der Kompressoren liefert das Projekt auch einen Beitrag im Bereich der Energieeffizienz. Das zugrunde liegende Verfahren soll darüber hinaus technologieübergreifend bei anderen Produkten einsetzbar sein.
Fehlerdetektion durch akustische Signale, künstliche Intelligenz und maschinelles Lernen
Akustische Signale und Vibrationsdaten enthalten Signaturen, die einen Rückschluss auf den Zustand eines Kompressors und dessen Entwicklung ermöglichen. Diese Daten werden mit Methoden der künstlichen Intelligenz (KI) und des maschinellen Lernens (ML) bewertet. Oft müssen dafür alle Fehler, die bei der Konstruktion der Modelle auftreten können, bekannt sein – nur so können sie später wiedererkannt werden. In unserem Ansatz sollen aber die Bestimmung und Vorhersage abnormaler Zustände (Anomalien) ohne ein solches Vorwissen möglich sein. Das ist Voraussetzung für eine schnelle und einfache Integration in neue Umgebungen und laufende Systeme.
In den im Projekt durchgeführten Experimenten kamen verschiedene Sensoren zur Anomalieerkennung zum Einsatz. Dabei wurden die Sensorpositionen (Abbildung 1) so gewählt, dass möglichst viele Bauteile überwacht werden. In Abbildung 2 sind die Fehlerraten (logarithmisch skaliert) für die Unterscheidung zwischen jeweils einer Anomalie und dem Normalzustand für alle Sensoren unter Verwendung neuronaler Netze dargestellt. Je geringer die Fehlerrate, desto seltener treten Fehlalarme auf und desto besser ist die Detektion von Defekten. Das Leck im Druckluftsystem und die Verschmutzung des Luftfilters konnten besonders gut mit einem Luftschallsensor gefunden werden. Das Leck in der Abdeckung des Ölkühlers ließ sich ebenfalls gut detektieren. Die Einzelkomponenten werden derzeit in einen Demonstrator integriert und anschließend an Kompressoren evaluiert.
Fördergeber: Bundesministerium für Bildung und Forschung (BMBF)
Projektträger: Projektträger Karlsruhe (PTKA)
Förderkennzeichen: 02K18K012
Projektpartner: Petko GmbH, SONOTEC Ultraschallsensorik Halle GmbH